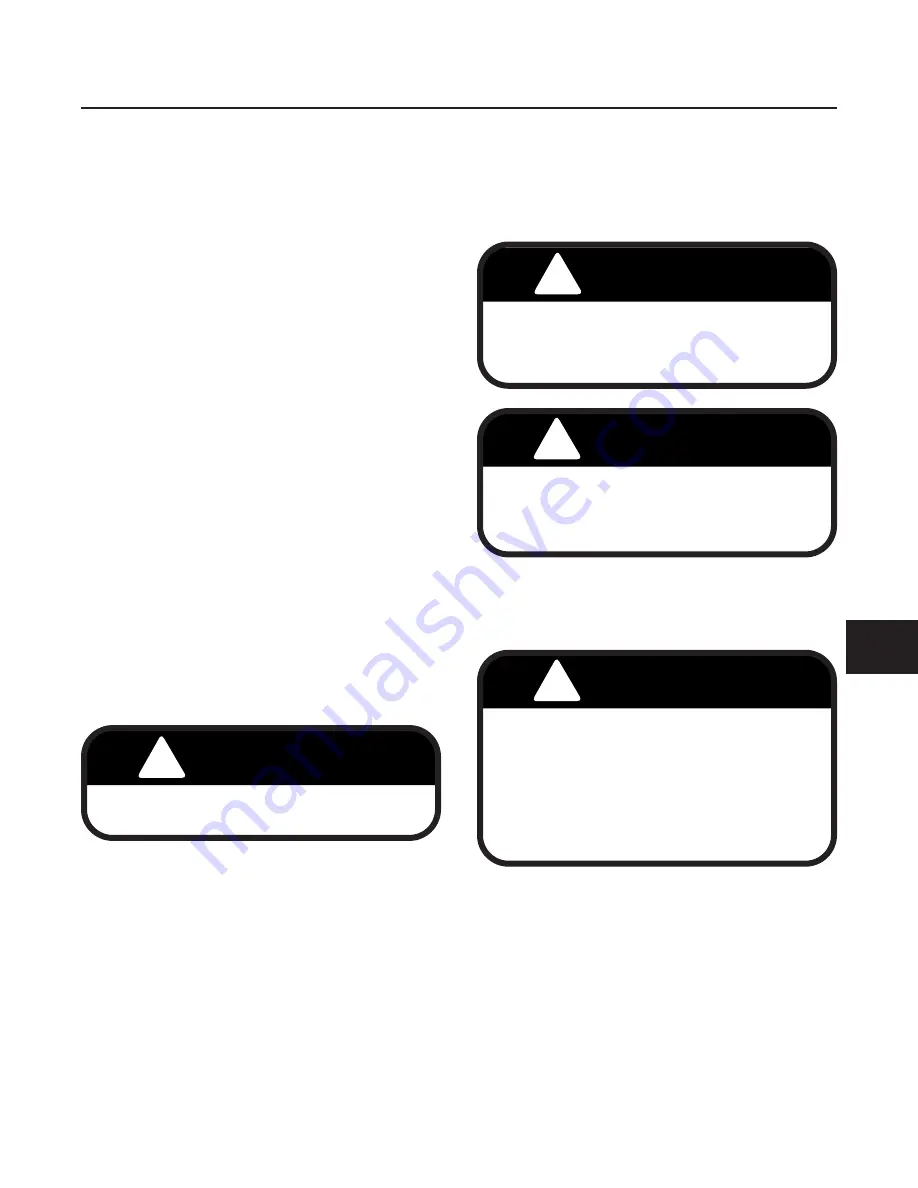
GENERAL
NOTE
Component location illustrations and hydraulic
diagrams are located at the end of this section.
The following general instructions apply to all hy-
draulic system service procedures. Carefully read and
adhere to each precaution.
•
Dirt in the hydraulic system will cause damage to
system components and reduce the life of the ma-
chine. Clean all dirt from around fittings and compo-
nents
before
disconnecting any hydraulic lines or
removing components.
•
Relieve system pressure at components or hy-
draulic lines by slightly loosening the line fitting
before removing.
•
Immediately after disconnecting a hydraulic line,
cap the line fitting and plug the port of the removed
component from the machine. This not only pre-
vents the entry of dirt into the system but also elimi-
nates the loss of hydraulic fluid.
•
Identify and label all linkages, hydraulic lines and
component parts. Mark the pump and valve sections
before removal and disassembly. This will ensure
the correct order of parts during reassembly and
installation.
•
Drain hydraulic fluid from components before disas-
sembly.
•
Discard all seals and O-rings as they are removed.
Install new seals and O-rings during reassembly.
Most seals are available in component kit form from
your Jacobsen Distributor.
•
All parts should be thoroughly cleaned in a suitable
non-flammable solvent and air blown dried before
beginning repair or reassembly.
•
Perform repair procedures in a clean work area using
clean tools.
•
Do not force or pry components apart or together.
Light tapping with a plastic mallet is recommended
unless otherwise specified in the repair instruction.
•
Unless otherwise indicated, apply a light coat of clean
hydraulic fluid to parts as each is reassembled. Ap-
ply clean grease to O-rings, if necessary, to hold them
in position during reassembly.
•
Hydraulic hose and tube lines should be inspected
daily to check for loose connections, kinks, worn or
cut hoses, etc. Be sure tubes and hoses do not con-
tact other frame parts which could cause abrasive
wear. Always replace worn hose or tube assemblies
before operating machine.
HYDRAULIC TUBE AND HOSE FITTING
37° FLARE FITTINGS
Torque Recommendations
1. Assemble tube nut adapter to fitting with minimum
torque (finger tight) until flare contacts seat on fit-
ting body.
2. For tightening reference, mark a line lengthwise
on the flats of both the nut and adapter fitting with
a marker as shown in Figure 8C-1.
HYDRAULICS
SECTION 8C. GENERAL INSTRUCTIONS
8C-1
8C
!
CAUTION
Do not use steam or high pressure washers to
clean hydraulic components.
!
CAUTION
If, during the disassembly of any hydraulic com-
ponent metal chips or damage is found the hy-
draulic system must be drained, thoroughly flushed
with clean oil and then refilled.
!
WARNING
Always check hydraulic tank level after removing
and installing a hydraulic component or line. Se-
vere damage to system components can result if
they are allowed to run dry.
!
WARNING
To avoid serious bodily injury, always lower mow-
ers fully, place all controls in neutral and shut off
engine before inspecting hydraulic lines or hoses.
Never run hands across tubes, hoses or fittings
to check for leaks. Hydraulic fluid escaping under
pressure can have sufficient force to penetrate
skin and may cause infection in a minor cut or
opening in the skin.
Summary of Contents for HR 5111
Page 2: ......
Page 4: ......
Page 6: ......
Page 12: ......
Page 14: ......
Page 26: ......
Page 28: ......
Page 30: ......
Page 32: ......
Page 40: ......
Page 42: ......
Page 44: ......
Page 46: ......
Page 49: ...GENERAL See Figure 4E 1 DRIVE TRAIN SECTION 4E AXLE 4E 1 4E Figure 4E 1 Axle Assembly...
Page 60: ......
Page 62: ......
Page 64: ......
Page 66: ......
Page 68: ......
Page 70: ......
Page 72: ......
Page 74: ......
Page 76: ......
Page 88: ......
Page 90: ......
Page 94: ...STEERING SECTION 6E STEERING CYLINDER 6E 4 Figure 6E 4 Steering Cylinder Assembly...
Page 96: ......
Page 98: ......
Page 100: ......
Page 102: ......
Page 106: ......
Page 108: ...HYDRAULICS SECTION 8A REPAIR AND SERVICE TOOLS AND MATERIALS 8A 2 Figure 8A 1 Wheel Restraint...
Page 116: ......
Page 120: ......
Page 124: ......
Page 126: ......
Page 128: ......
Page 136: ......
Page 137: ...REPAIR HYDRAULICS SECTION 8J REAR TRACTION MOTOR 8J 1 8J Figure 8J 1 Rear Traction Motor...
Page 138: ...HYDRAULICS SECTION 8J REAR TRACTION MOTOR 8J 2 Figure 8J 2 Seal Assembly...
Page 139: ...HYDRAULICS SECTION 8J REAR TRACTION MOTOR 8J 3 8J Figure 8J 3 O Rings and Seals...
Page 140: ......
Page 142: ......
Page 145: ...HYDRAULICS SECTION 8L LIFT CYLINDER 8L 3 8L Figure 8L 3 Lift Cylinder Assembly...
Page 148: ...HYDRAULICS SECTION 8L LIFT CYLINDER 8L 6 Figure 8L 6 Wing Cylinder Assembly...
Page 154: ......
Page 156: ......
Page 160: ...HYDRAULICS SECTION 8Q HYDRAULIC FIELD TEST PROCEDURES 8Q 4...
Page 163: ...HYDRAULICS SECTION 8Q HYDRAULIC FIELD TEST PROCEDURES 8Q 7 Figure 8Q 5 Reel System 8Q...
Page 185: ...HYDRAULICS SECTION 8R INSTRUMENT TEST 8R 21 8R Figure 8R 19 Left Wing Motor Circuit Tests...
Page 186: ...HYDRAULICS SECTION 8R INSTRUMENT TEST 8R 22 THIS PAGE INTENTIONALLY LEFT BLANK...
Page 191: ...HYDRAULICS 8S 1 8S Figure 8S 1 Flow Diagram...
Page 192: ...HYDRAULICS 8S 3 Figure 8S 2 Schematic Early...
Page 193: ...HYDRAULICS 8S 5 8S Figure 8S 3 Schematic Later...
Page 202: ...HYDRAULICS 8S 7 Figure 8S 4 Traction System 1 of 4...
Page 203: ...HYDRAULICS 8S 9 8S Figure 8S 5 Power Steering System 2 of 4...
Page 204: ...HYDRAULICS 8S 11 Figure 8S 6 Lift System 3 of 4...
Page 205: ...HYDRAULICS 8S 13 8S Figure 8S 7 Mower System 4 of 4...
Page 206: ......
Page 208: ......
Page 210: ......
Page 212: ......
Page 214: ......
Page 216: ......
Page 218: ......
Page 226: ......
Page 249: ...ELECTRICAL SYSTEM SECTION 10G SWITCHES 10G 5 10G Figure 10G 5 Ignition Switch Test Step 4...
Page 268: ......
Page 272: ......
Page 280: ......
Page 284: ......
Page 286: ......
Page 288: ......
Page 292: ......
Page 302: ......
Page 310: ......
Page 312: ......
Page 314: ......
Page 316: ......
Page 318: ......
Page 323: ...ATTACHMENTS SECTION 12D MOWERS 12D 5 12D Figure 12D 5 Motor Rotation By Code Letter...
Page 328: ...ATTACHMENTS SECTION 12F CASTER WHEELS 12F 2 Figure 12F 2 Caster Wheel Repair...
Page 329: ...13 THIS SECTION INTENTIONALLY LEFT BLANK SECTION 13 OPTIONS...
Page 330: ......
Page 332: ......
Page 335: ...MISCELLANEOUS SECTION 14A PRECAUTION DECAL LOCATIONS 14A 3 14A MOWER Part No J T338141 1...
Page 336: ......
Page 337: ...MISCELLANEOUS SECTION 14B CONVERSION CHARTS 14B 1 14B MILLIMETERS TO DECIMALS...