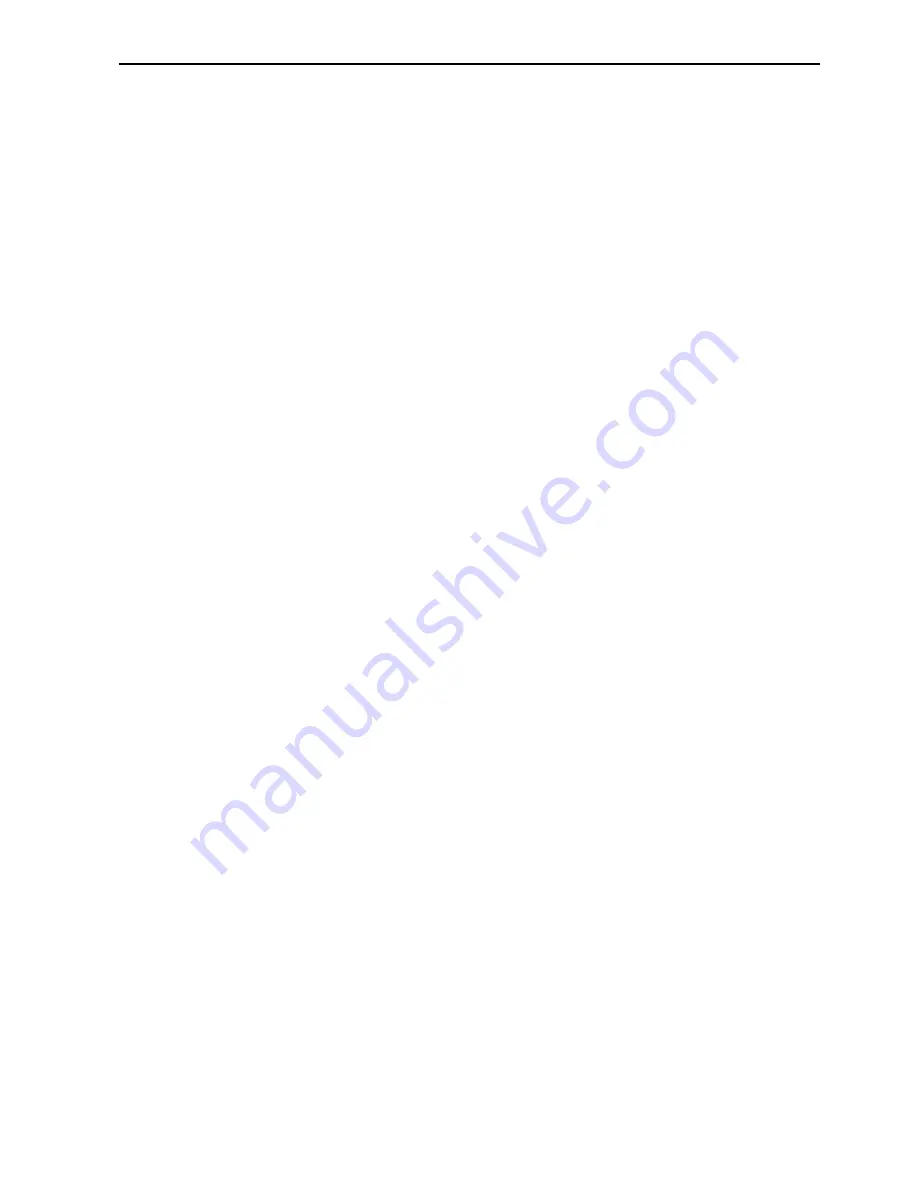
en-17
LABELS 4
A.
009034920
Caution, Stay Away From Hot Surfaces.
B.
009034880
Caution, Fan Blade, Do Not Open Or Remove The Safety Shields While The Engine Is
In Operation.
C.
009034900
Caution, Drive Belt, Do Not Remove The Safety Shields While The Engine Is In
Operation.
D.
009114340
Caution, Diesel Fuel.
E.
009114100
Caution, Battery.
F.
4333660
Slope Angle.
G.
009034960
Caution, Rotating Blades.
H.
009114380
Caution, Fasten Seat Belt.
J
4153197
Caution, Stop The Engine And Remove The Starter Key Before You Pressure Wash
The machine.
K.
4164860
Caution, Hydraulic Oil.
L.
4181865
Decal, Warning.
Summary of Contents for ES Series
Page 8: ...en 8 2 INTRODUCTION NOTES...
Page 45: ...en 45 5 CONTROLS NOTES...
Page 95: ...en 95 QUALITY OF CUT 10 NOTES...
Page 98: ...en 98 11 FUSES AND RELAYS NOTES...
Page 111: ...en 111 SPECIFICATIONS 12 NOTES...