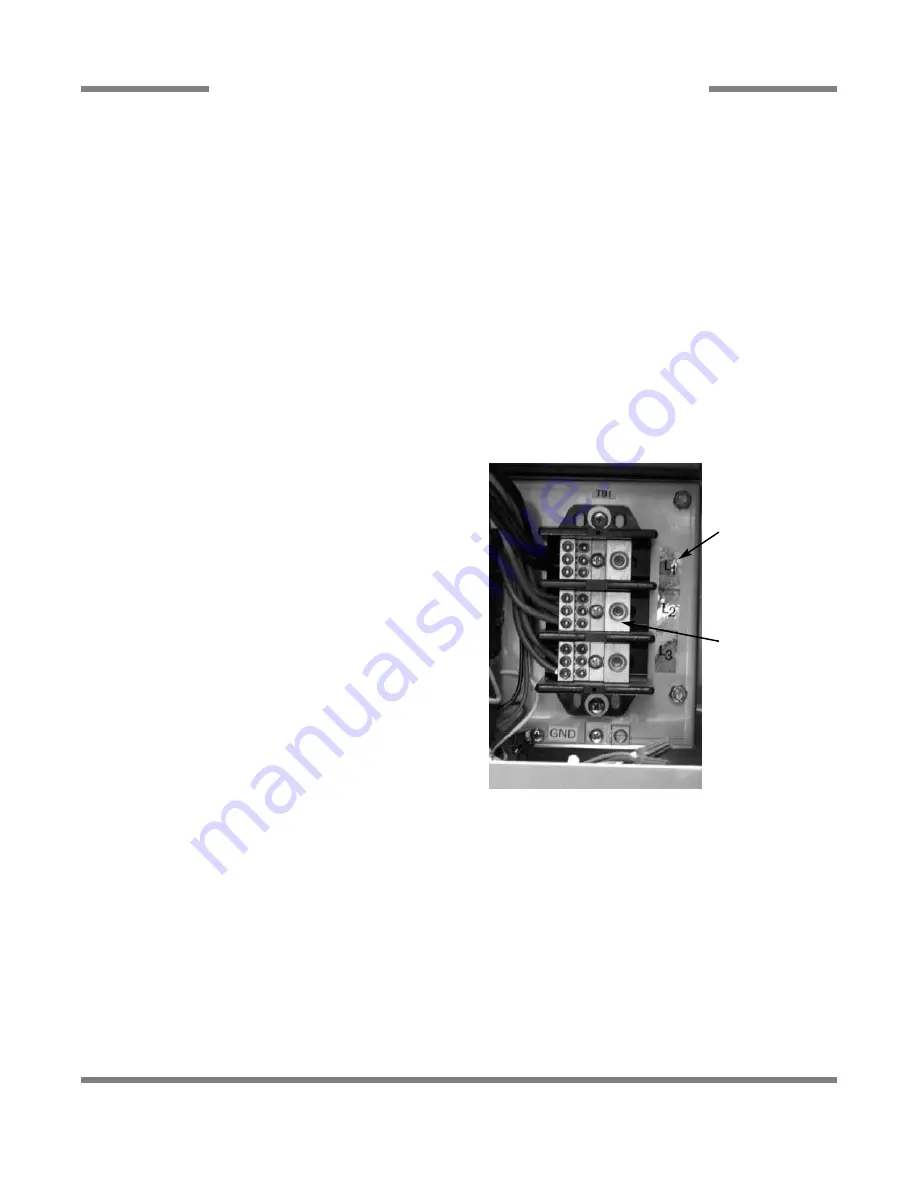
STEAM LINE CONNECTIONS:
Some machines covered in this manual are designed to use low pressure steam as a source
of heat for wash tank water. The machines come with lines by which outside source steam needs to be connected. Connect all
incoming steam lines in accordance with the steam booster manufacturer’s instructions. Ensure that all applicable codes and
regulations are adhered to. See machine data plate for information concerning steam flow pressure.
PLUMBING CHECK:
Slowly turn on the water supply to the machine after the incoming fill line and the drain line have been
installed. Check for any leaks and repair as required. All leaks must be repaired prior to placing the machine in operation.
ELECTRICAL POWER CONNECTION:
Electrical and grounding connections must comply with the applicable portions of the
National Electrical Code ANSI/NFPA 70 (latest edition) and/or other electrical codes.
Disconnect electrical power supply and place a tag at the disconnect switch to indicate that you are working on the
circuit.
The dishmachine data plate is located on the right side and to the front of the machine. Refer to the data plate for machine
operating requirements, machine voltage, total amperage load and serial number.
To install the incoming power lines, open the control box. Install conduit into the pre-punched holes in the back of the control
box. Route power wires and connect to power block and grounding lug. Install the service wires (L1, L2, and L3 (3 phase only))
to the appropriate terminals as they are marked on the terminal
block. Install the grounding wire into the lug provided. Tighten
the connections. It is recommended that “DE-OX” or another
similar anti-oxidation agent be used on all power connections.
VOLTAGE CHECK:
Ensure that the power switch is in the OFF
position and apply power to the dishmachine. Check the incom-
ing power at the terminal block and ensure it corresponds to the
voltage listed on the data plate. If not, contact a qualified service
agency to examine the problem. Do not run the dishmachine if
the voltage is too high or too low. Shut off the service breaker
and mark it as being for the dishmachine. Advise all proper per-
sonnel of any problems and of the location of the service break-
er. Replace the control box cover and tighten down the screws.
VENTILATION OF DISHMACHINE:
The dishmachine should be
located with provisions for venting into an adequate exhaust
hood or ventilation system. This is essential to permit efficient
removal of the condensation exhaust. Ensure that the exhaust
system is acceptable in accordance with all applicable codes
and standards.
NOTE: Any damage that is caused by steam or moisture due
to improper ventilation is NOT covered under the warranty.
This units covered in this manual have the following exhaust requirements:
Load End:
200 CFM
Unload End:
400 CFM
The exhaust system must be sized to handle this volume for the dishmachine to operate as it was designed to.
ELECTRIC HEAT:
The thermostats for the machines covered in this manual are factory set. They should not be adjusted except
by an authorized service agent.
CHEMICAL FEEDER EQUIPMENT:
Detergent may be introduced into the unit through the removal of the bulkhead plug in the
rear of the tub and replacing it with the third party detergent injection fitting. Remove the bulkhead plug in the side of the tub to
AJX-44 & AJX-54 Series Technical Manual 7610-003-60-98
Issued: 01-19-2009 Revised: 01-30-2009
SECTION 2: INSTALLATION/OPERATION INSTRUCTIONS
INSTALLATION INSTRUCTIONS (CONTINUED)
22
Incoming Power Connection
Decal showing
“L1”, “L2”, & “L3”
(3 phase models
only).
Terminal Block
Summary of Contents for AJX-44 Series
Page 8: ...1 SECTION 1 SPECIFICATION INFORMATION ...
Page 27: ...20 SECTION 2 INSTALLATION OPERATION INSTRUCTIONS ...
Page 38: ...31 SECTION 3 PREVENTATIVE MAINTENANCE ...
Page 42: ...35 SECTION 4 TROUBLESHOOTING SECTION ...
Page 45: ...38 SECTION 5 PARTS SECTION ...
Page 92: ...85 SECTION 6 ELECTRICAL SCHEMATICS ...
Page 103: ...96 SECTION 7 JACKSON MAINTENANCE REPAIR CENTERS ...
Page 110: ...AJ 44T Series Technical Manual 7610 003 07 21 Issued 03 21 2006 Revised N A ...