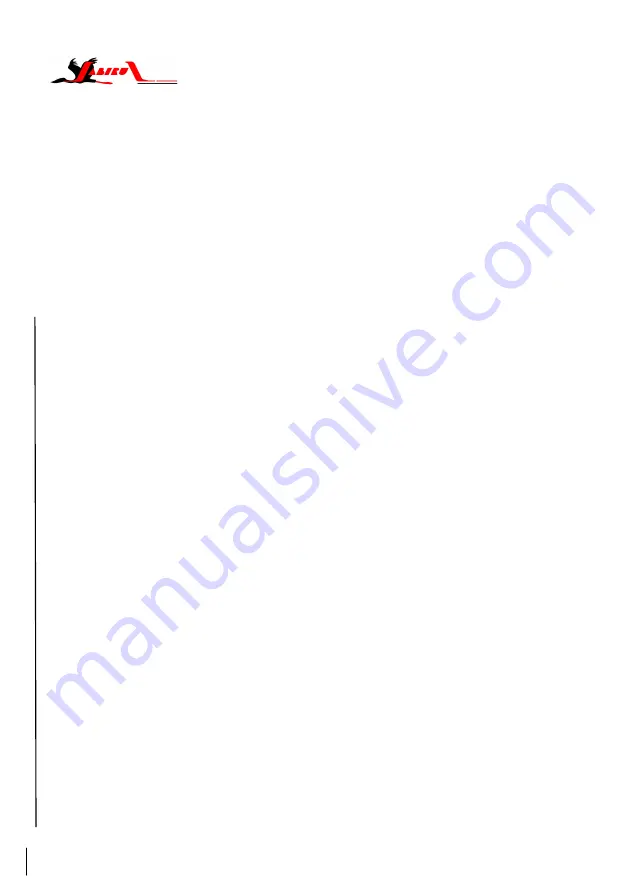
Jabiru Aircraft
SECTION 7
Model J160-C
AIRCRAFT AND SYSTEMS
JP-FM-06
Revision:
0
1
2
3
1 Dec 2008
Page 7-8
7.12.9
Cooling System
Ram air for engine cooling enters through two intakes at the front of the engine cowl. The
cooling air is directed around the cylinders and other areas of the engine by appropriate baffles
and is then exhausted through an opening in the rear of the lower cowl. Air for oil system cooling
enters the lower intake chamber and flows through an oil cooler mounted below the sump. The
air then exhausts out the lower cowl opening with the engine cooling air.
7.13 PROPELLER
The aircraft is equipped with a two blade Jabiru propeller. The propeller is made of 3 laminations
of hoop pine sheathed in GRP. The propeller has a diameter of 60” and a pitch of 42”. A
Urethane leading edge is moulded into the propeller to provide protection from damage caused
by small rock strikes, operating in the rain etc.
7.14 FUEL SYSTEM
The aircraft has a fuel tank in the inboard section of each wing, and a small header tank which is
located in a sealed compartment underneath the baggage shelf. The wing tanks gravity feed into
the header tank and there is no provision for the pilot to select and/or isolate a particular wing
tank. A single shut off vale is provided to stop all fuel flow to the engine. Figures 7.14.3 and
7.14.4 are schematic diagrams of the fuel system.
The engine is equipped with a Bing altitude compensating carburettor. There is no mixture
control adjustment available to the pilot. A choke is provided for engine starting purposes only
Two slightly different systems are used depending on the age of the aircraft – details of both are
presented below.
System #1:
Fuel gravity feeds from the front and rear inboard corner of each tank. The two
delivery pipes from each side join together in the fuselage wall below the wing. Then the single
delivery line continues to the header tank under the passenger’s side of the baggage shelf.
Breathers for the wing tanks run from the outboard end of the tank and are connected with lines
that run between the tanks. The header tank breather is also connected into this breather line.
System #2:
Fuel gravity feeds from the front and rear inboard corner of each tank. The two
delivery pipes and the vent line for each wing tank run directly to the header tank located under
the passenger’s side of the baggage shelf behind the seats.
Both Systems:
From the sump tank fuel flows through an electric boost pump then forward
through the filter and shutoff valve to the engine driven mechanical fuel pump and carburettor.
All wing and sump tank outlets have finger filters. The three fuel tanks are fitted with fuel drains.
The wing tanks are fitted with vented caps located at the outboard end of the tank. The vent for
each cap is directional and provides a small pressure head to the tanks. This system ensures
that the air space pressure in each tank is the same, minimising uneven fuel feed rates.
The J160-C may use either two fuel sight gauges (one in each wing root) or two electric fuel
gauges on the instrument panel to show fluid levels in each wing tank. The sump tank does not
have a fuel gauge as its contents are deemed to be unusable and should not to be considered for
flight planning. As an option, a low level warning light may be installed in the header tank.
Refer to Figures 7.14.3 and 7.14.4 for schematic drawings of the system.
Summary of Contents for J160-C
Page 2: ...This page intentionally left blank...
Page 3: ......
Page 5: ...This page intentionally left blank...
Page 7: ...This page intentionally left blank...
Page 9: ...This page intentionally left blank...