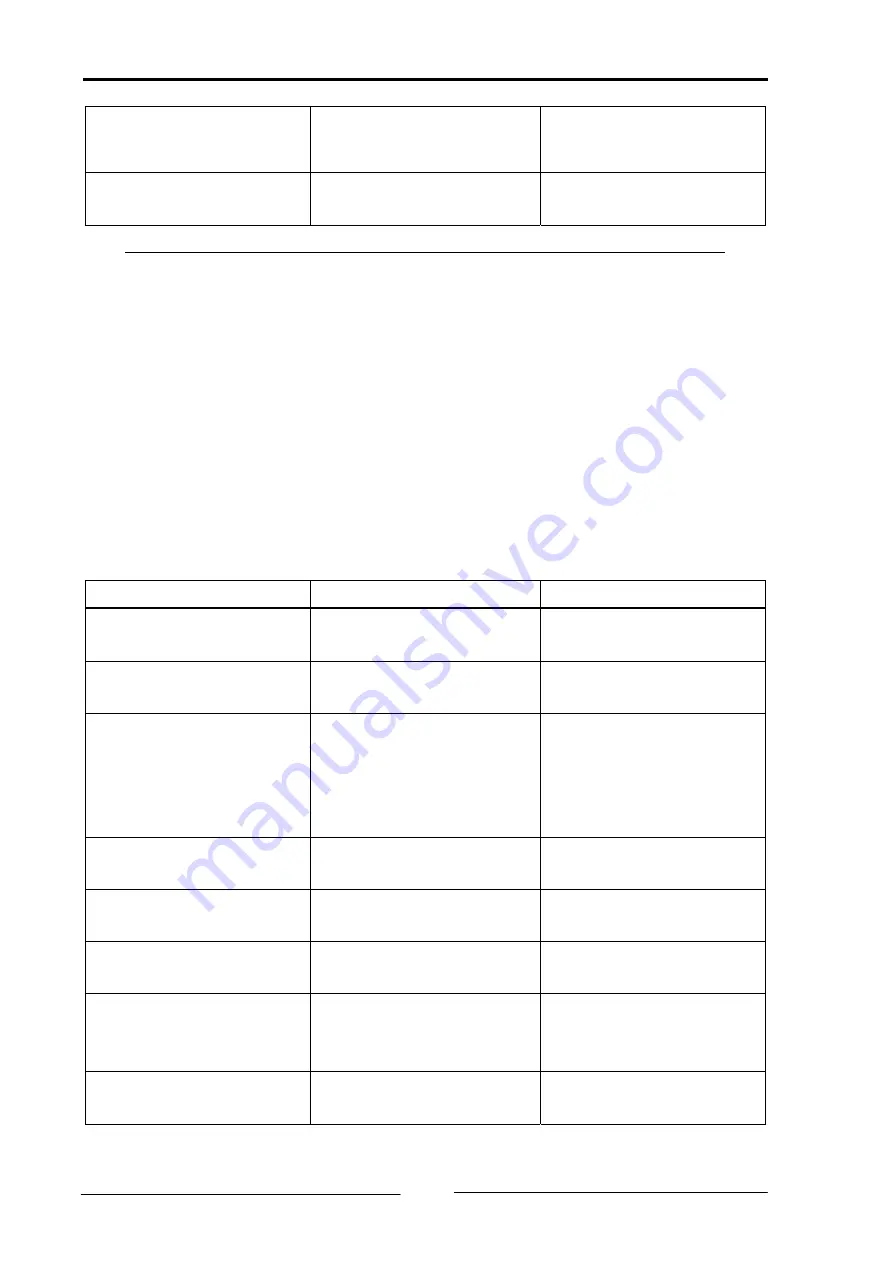
Description of functions
CAN identifier for transmis-
sion of the data to the CAN
bus
All CAN identifiers are possible SendID
(under [CANlink])
CAN identifier for receiving
data from CAN bus
All CAN identifiers are possible ReceiveID
(under [CANlink])
Table 4-1
In the CANlink mode, the device transmits the data that arrive on the serial port
to the CAN bus under a configurable identifier. In the same way, data that are
received via CAN by means of another configurable identifier are passed on to the
serial port.
4.3 RS232-CANopen
gateway
Table 4-2 shows the functions and the associated key words, relevant for the
COPlink mode.
Function
Possible settings
Key words
Operation mode
COPlink
OperationMode
(under [General])
Timeout
0 - 6,5 s
Timeout
(under [General])
RS232 parameter
1. Baudrate
2. Number of databits
3. Parity
4. Flow control
RS232baudrate
Databits
Parity
Handshake
(all under [RS232])
CANopen baudrate
CiA baudrates are possible
CANopenBaudrate
(under [COPlink])
CANopen node number
1-127
CANopnNode
(under [COPlink])
Heart Beat Time
0- 32 s
HBTime
(under [COPlink])
Receive PDO
PDO ID – all free CANopen Ids
PDO Type – 0..240, 252..255
RxPDO
RxPDOtype
(under [COPlink])
Transmit PDO
PDO ID – all free CANopen Ids
PDO Type – 0..240, 252..255
TxPDO
TxPDOtype
Copyright IXXAT Automation GmbH
CANlink II - Manual, V1.3
18
Summary of Contents for CANlink II
Page 6: ......