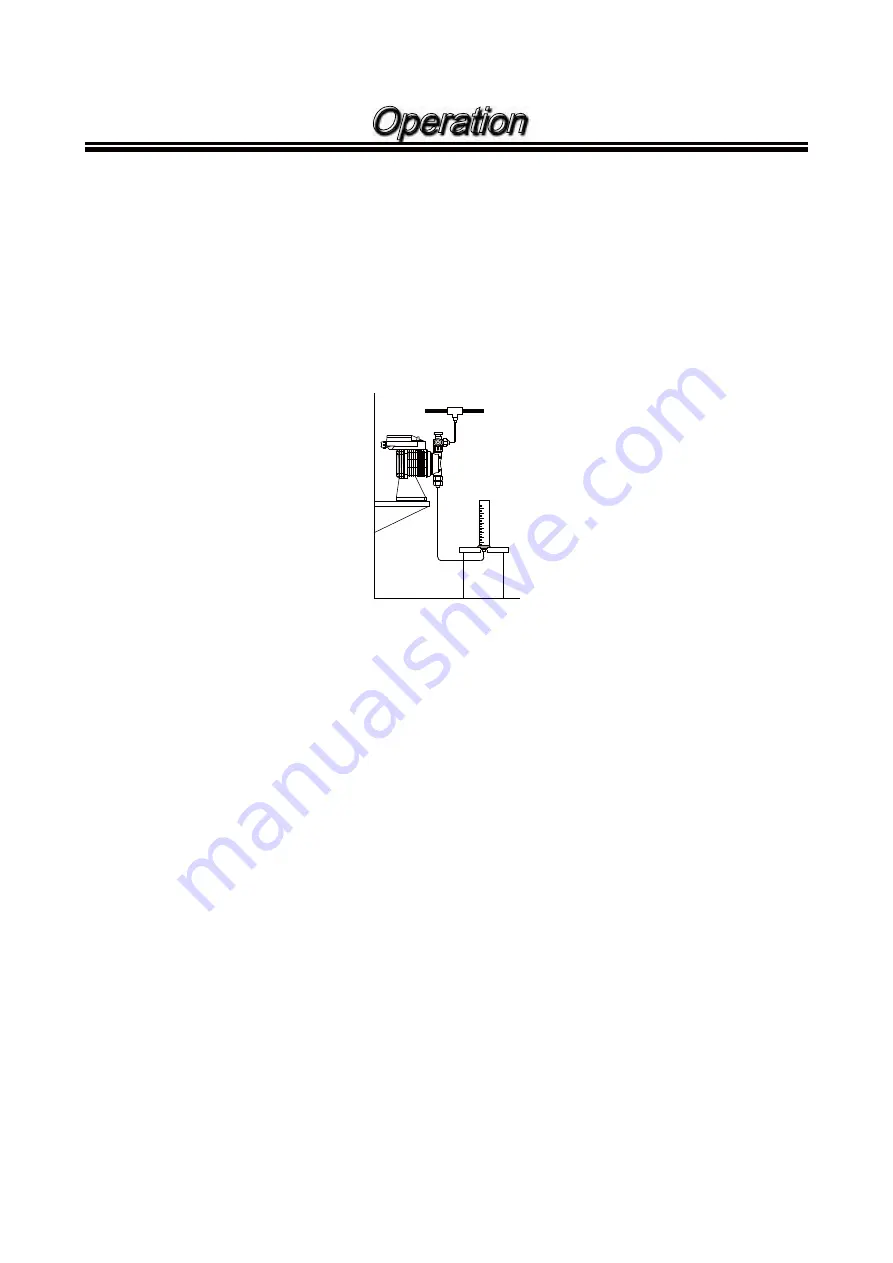
- 12 -
Operation
3. Calibration
If exact output calibration is required, first prime and adjust the pump as above. Then connect a calibra-
tion column to the suction side of the pump. Turn the pump on for one minute and read the amount of liquid
pumped from the column. Adjust the frequency up or down as necessary and check the output again. When
the desired output is reached, disconnect the calibration column and reconnect the suction tubing (See
Figure 4).
Figure 4
Calibration