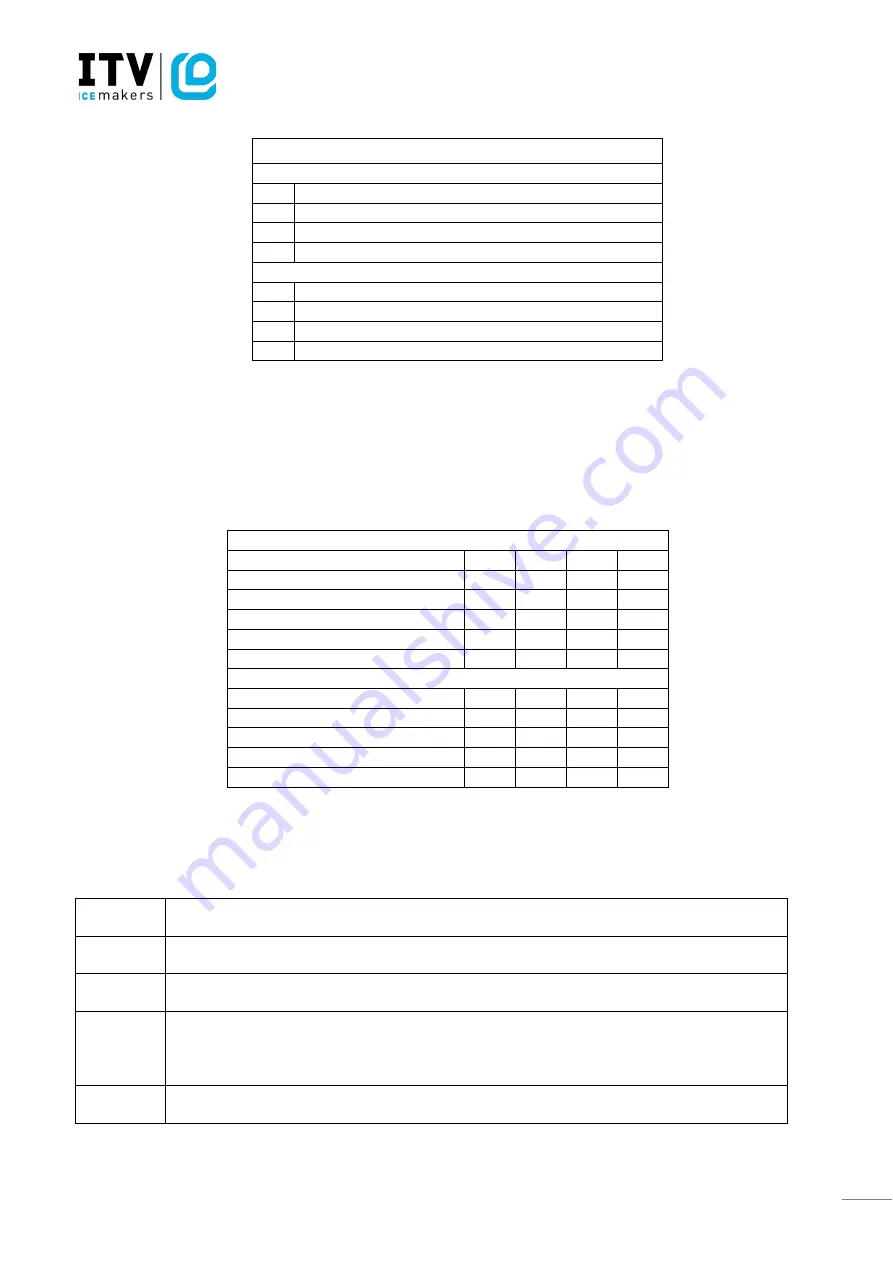
SERVICE MANUAL
SPIKA SERIES
15
PCB connections
Outputs
C
compressor
B
Water pump
EA
Water inlet valve
GC Hot gas valve.
Inputs
SC Evaporator temperature NTC probe
P
Safety pressure switch
MC Curtain switch
N
PCB push button
LED signalling
Next to each out relay there is an orange led. Signals relay on
Next to each input terminal there is an orange led marking input active.
There are four additional red leds that signals machine status (continuous) or alarm (flashing)
Status signaling . Continuous led
LE1
LE2
LE3
LE4
Start up delay
X
Ice cycle T>Tc
X
X
Ice cycle T<Tc
X
Harvest
X
Full bin
X
Alarm signaling . Flashing led
LE1
LE2
LE3
LE4
Safety pressure switch
X
Ice cycle timeout
X
Harvest cycle timeout
X
Faulty temperature probe
X
Dip switches setting
dip
Descripción (* factory setting)
1-4
tf - ice production timer. See table
5-7
tw - Water input timer. See table.
8
Tc - Evaporator temperature for timer start.
ON=-2ºC / OFF=-4ºC
9
Not used