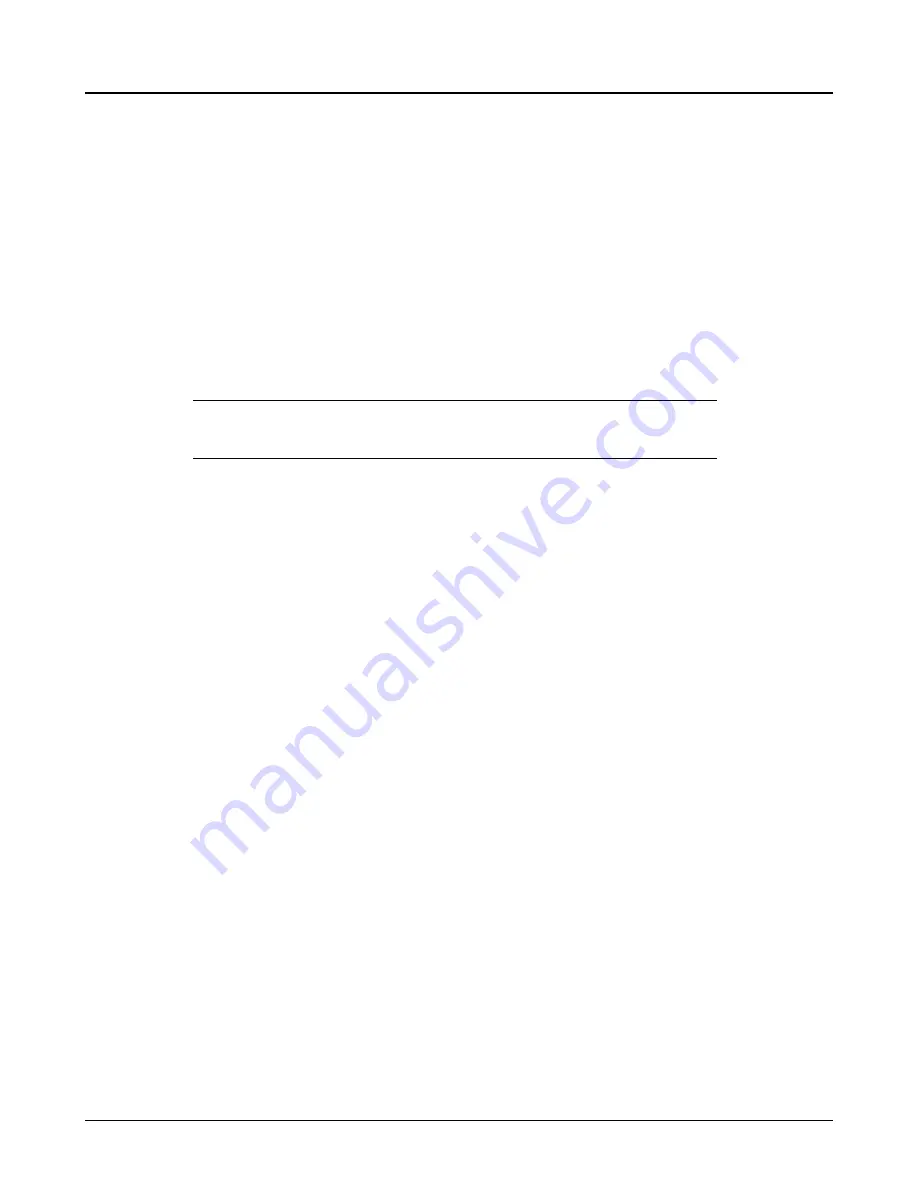
Positive Reading - The coupling half Y is shifted toward position 3. If the value is greater
than .003" (.076mm), shift the motor accordingly.
4.
Repeat steps 1-3 until indicator P reads .003in. (.076mm) or less.
5.
Once the ideal alignment is reached, repeat steps 1- 4 substituting position 2 for position 1 and
position 4 for position 3.
Method 2 - Straight-Edge Method
For the following steps refer to Fig. 4.
1.
Place a straight edge across the two coupling flanges at position 1 and mark the spot on both
flanges.
2.
Adjust the motor so that the straight-edge rests evenly on both flanges (within .003in. - .076mm).
3.
Rotate both flanges 90° to positions 2 and repeat steps one and two.
4.
The unit will be in parallel alignment when the straight edge rests evenly (within .003in. - . 76mm)
on the coupling periphery at both positions along the periphery.
NOTICE:
Care must be taken to have the straight edge parallel to the axis of the shafts.
TIP:
Since the coupling halves are disconnected, this would be a good time to check the motor
rotation to see if it is in the proper direction.
5.1.6 V-belt drive -alignment
Well designed and properly installed v-belt drives are capable of running for years without maintenance.
There are a few points that should be checked periodically.
1.
Sheave Alignment - Alignment must be maintained for full power transmission, minimum vibration,
and long drive life. A dial indicator can be used to check runout on the periphery and face of each
sheave. A straight edge can be used to check the alignment of the pump and drive sheaves in the
vertical direction, See Fig. 6 page 6.
2.
Belt Installation - When installing new belts, shorten center distance between sheaves so that belts
can be placed on the sheave without the use of force. Never "roll" or "pry" the belts into place, as
this could damage the belt cords.
3.
Check Belt Fit - Regardless of the belt section used, the belt should never be allowed to bottom in
the groove. This will cause the belts to lose their wedging action and slippage can occur. Sheaves
or belts that permit such a condition to occur should be changed.
4.
Maintain Proper Belt Tension - Proper tension is essential for long belt life. Improper tension could
cause belt fatigue and/or hot bearings.
The general method for tensioning belts is given below, and should satisfy most drive requirements.
Step 1: Reduce the center distance so that the belts may be placed over the sheaves and in the
grooves without forcing them over the sides of the grooves. Arrange the belts so that both belt
spans have approximately the same sag between the sheaves. Apply tension to the belts by in-
creasing the center distance until the belts are snug, see Fig.5.
5.1 Installation Instructions-Vertical Pumps
Model VJC Installation, Operation, and Maintenance Manual
19
Summary of Contents for VJC
Page 1: ...Installation Operation and Maintenance Manual Model VJC ...
Page 2: ......