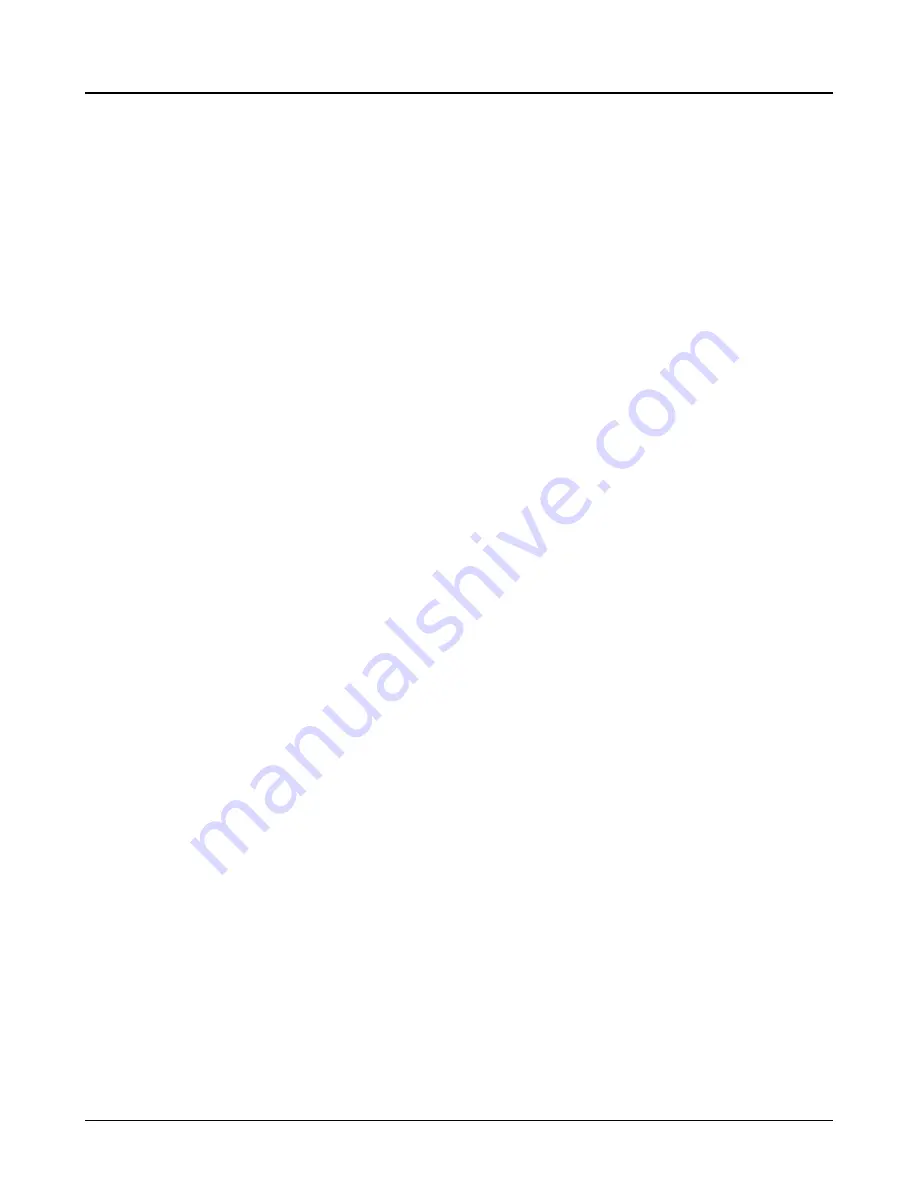
7.8 Assembly
A complete assembly operation is described in the following.
Sub-sections can be deduced from this.
7.8.1 Assemble bearing pedestal
1.
Press both radial ball bearings 321 onto the drive shaft 213.
2.
Insert key 940/1 into the drive shaft.
3.
Install the pre-assembled drive shaft into the bearing pedestal from the motor side.
4.
Insert wavy spring washer 953/1 into the bearing pedestal.
5.
Mount rear bearing cover 361 with the hex. socket screw 914/2.
6.
Mount support bracket 183 with hex. screws 901/2 and toothed lock washers 936/2.
The attachment slots of the support surface face towards the housing.
7.8.2 Assemble the drive magnet
1.
Clamp the pre-assembled bearing pedestal on the shaft end in the vice so that the carrier groove ,is
facing upwards.
2.
Mount drive magnet assembly 858 onto the drive shaft so that the driver cams engage.
3.
Screw in hex. socket screw 914/1 with tooth lock washer 936/1. Secure thread, with a drop e.g of
Loctite 234.
A hex. socket screw key with a minimum length of 120 mm is required for tightening.
7.8.3 Plain bearing pedestal with impeller, inner magnet assembly and
plain bearings
1.
Insert the plain bearing cartridge (310) into the centering of the plain bearing pedestal (339).
2.
Move the plain bearing cartridge into a position which permits all 3 hex. screws (901/1) to be insert-
ed.
3.
Tighten screws with an open-jaw wrench. For tightening torques, see
.
4.
If the parallel pin (562/1) in the clearance bore in the inner magnet assembly (859) has to be re-
placed, force it in carefully. It is to protrude by about 3 mm towards the impeller.
5.
Cut out a small corner on the inside diameter of the intermediate ring (509/1) so that a recess is
produced.
6.
Then mount the intermediate ring (509/1) onto the shaft of the inner magnet assembly (859).
7.
Apply Anti Seize assembly paste to the shaft and impeller holder.
8.
Place inner magnet assembly on the workbench and mount the pre-assembled unit plain bearing
pedestal / plain bearing cartridge from above onto the inner magnet assembly. Make sure that the
parallel pin (562/1) engages in the carrier groove of the plain bearing cartridge. To facilitate align-
ment, the plain bearing pedestal can be turned to and fro slightly.
9.
Mount 2
nd
intermediate ring (509/2) onto the drive shaft.
10. Mount distance washer (551/1).
11. Insert key (940/2).
12. Mount impeller (230).
13. Insert PTFE O-ring (912/1) into the groove of the impeller nut (231).
14. Tighten impeller nut. Secure it with a drop of e. g. Loctite (234). Counter check the inner magnet
assembly with a strap wrench. For tightening torques, see
2.3 Tightening torques on page 12
15. It must be possible to easily turn the plain bearing pedestal (339) by hand. When raising the plain
bearing pedestal, a slight axial play of the plain bearing of up to 1 mm must be felt.
16. The axial play of the plain bearing is automatically set during assembly.
7.8.4 Can and lantern
1.
Place the can gasket (406) in the centering on the plain bearing pedestal (339).
7.8 Assembly
Model ICM/ICMP Magnetic Drive Chemical Process Pump with Grease Bearing Lubrication Installation, Operation, and
Maintenance Manual
31
Summary of Contents for Goulds Pumps ICM
Page 2: ......