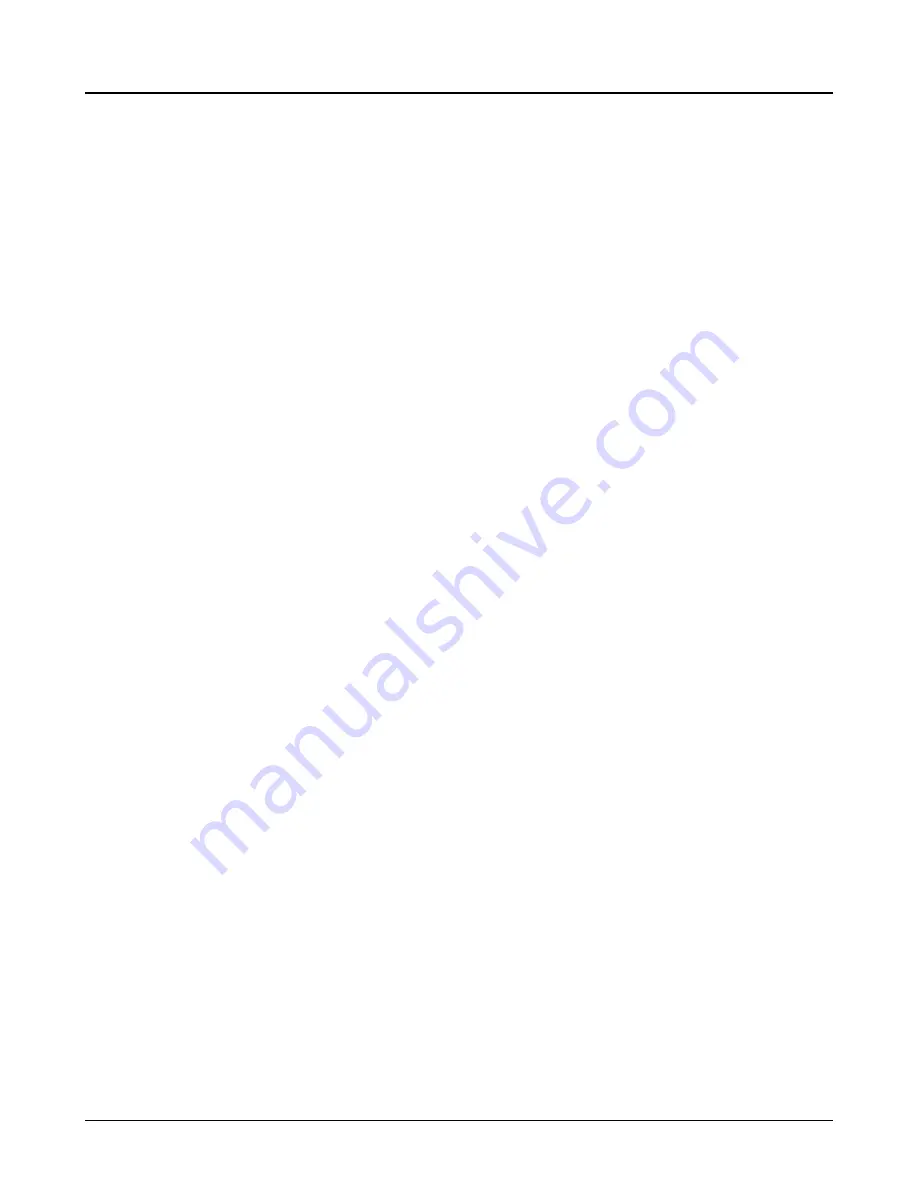
7.6.3 Removing lantern, can and plain bearing pedestal
1.
Undo housing screwing (901/3), (554/3).
2.
Do not undo the two screws (901/5) (if installed). They hold the lantern (344), can (159) and plain
bearing pedestal (339) together.
3.
Pull the entire slide-in unit out of the housing (100).
4.
If the housing does not move (e.g. owing to corrosion at the centering), remove the two plastic plugs
from the lantern (344).
5.
Screw in jacking screws M8 and use them to press off the lantern.
7.6.4 Dismantling lantern, can and plain bearing pedestal
1.
Place the unit lantern (344) / plain bearing pedestal (339) / impeller (230) on the workbench with the
impeller facing upwards.
2.
Remove the two hex. screws (901/5) or the 3 setscrews (904/2) (depending on size).
3.
Remove lantern (344) and can (159).
4.
Place remaining unit on the inner magnet assembly.
5.
Place strap wrench around the impeller and undo the impeller nut (231) counterclockwise.
6.
Pull off impeller (230).
7.
Remove key (940/2), distance washer (551/1) and intermediate ring (509/2).
8.
Pull the plain bearing cartridge (310) with plain bearing pedestal (339) out of the inner magnet as-
sembly 859.
9.
Remove 2
nd
intermediate ring (509/1) from the inner magnet assembly (859).
10. If the inner magnet assembly or inner magnet assembly shaft has to be replaced (split inner magnet
assembly): Push the inner magnet assembly shaft (220) and key (940/2) out of the inner magnet
assembly (859) with a hydraulic press. Make sure that the thread for the impeller nut is not dam-
aged.
11. Undo screws (901/1) and remove plain bearing cartridge (310) from the plain bearing pedestal
(339).
7.6.5 Dismantling the plain bearing
The plain bearing cartridge (310) is one unit which - if necessary - is replaced completely.
7.7 Notes on assembly
7.5 Notes on dismantling on page 28
are to be observed, in particular the notes on safe-
ty.
Good mechanical engineering practice is to be observed for assembly work.
Use original spare parts. See also Conversion work and production of spare parts by the customer. Do
not use defective parts.
Treat close-tolerance areas (not stainless steel components) with a corrosion inhibitor. Grease screw
threads prior to assembly.
Apply Anti Seize paste to close-tolerance surfaces (not on stainless steel parts) and screw thread prior to
assembly.
Check whether all parts fit and only then perform assembly.
Important dimensions are to be checked before assembly, e.g. by fitting parts together as a test.
These important dimensions are centerings, bearing seats or bearing clearances.
During assembly, gaskets (400), (401) and (406) are to be replaced, intermediate rings (509) must be
replaced.
Prior to assembly, remove any metallic particles adhering to parts fitted with magnets.
7.7 Notes on assembly
30
Model ICM/ICMP Magnetic Drive Chemical Process Pump with Grease Bearing Lubrication Installation, Operation, and
Maintenance Manual
Summary of Contents for Goulds Pumps ICM
Page 2: ......