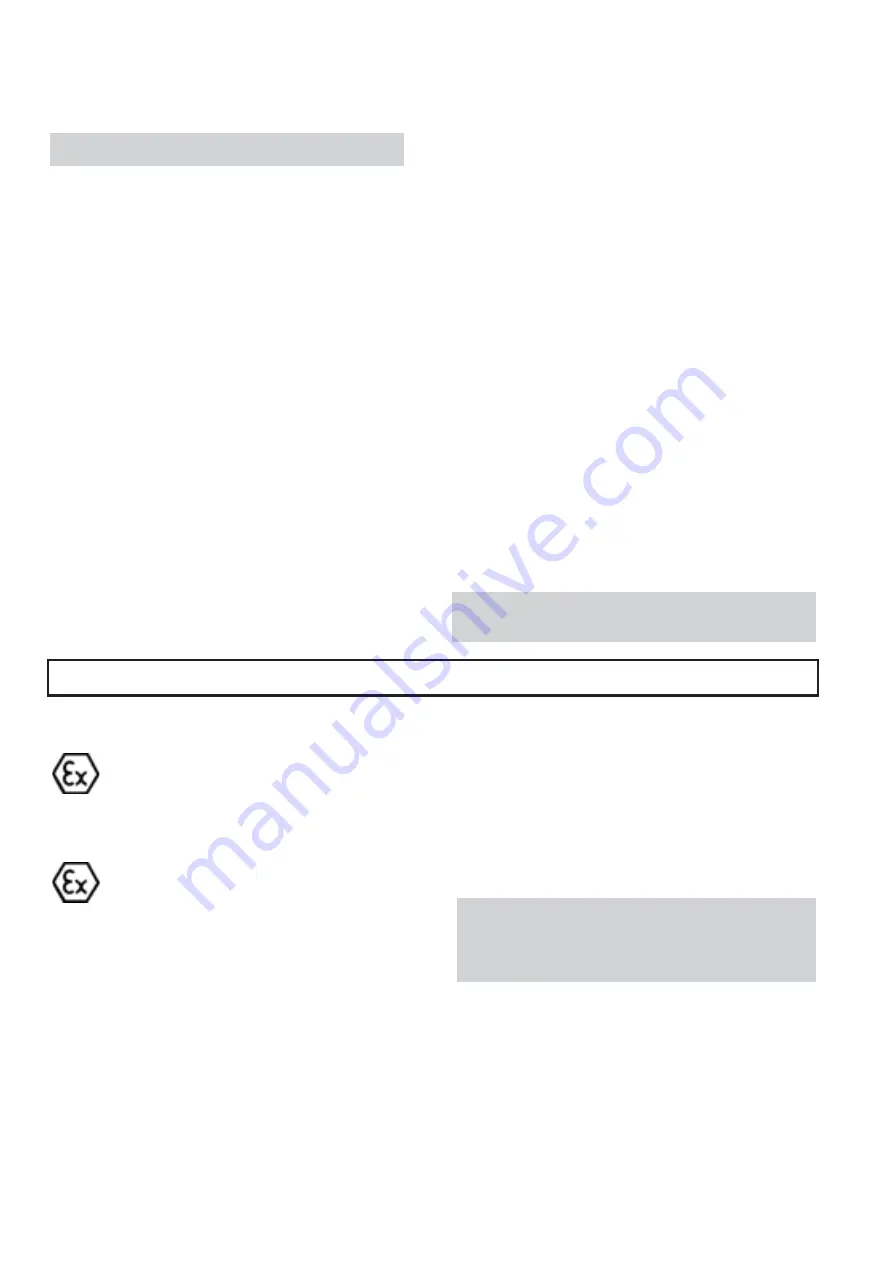
26
AF (6-36) IOM
NOTE: Care must be taken to have the straight
edge parallel to the axis of the shafts
COMPLETE ALIGNMENT
A unit is in complete alignment when both indicators
“A” (angular) and “P” (parallel) do not vary by more
than .003” (.076 mm) as measured at four points 90
°
apart.
Vertical Correction (Top-to-Bottom)
1. Zero indicators “A” and “P” at top dead center (12
o'clock) of coupling half (Y).
2. Rotate indicator to bottom dead center (6 o'clock).
Observe the needles and record the readings.
3. Make corrections as outlined previously.
Horizontal Correction (Side-to-Side)
1. Zero indicators “A” and “P” on the left side of
coupling half (Y), 90
°
from top dead center (9
o'clock).
2. Rotate indicators through, top dead center to the
right side, 180
°
from the start (3 o'clock), Observe
the needle, measure and record the reading.
3. Make corrections as outlined previously.
4. Recheck both vertical and horizontal readings to
ensure adjustment of one did not disturb the other.
Correct as necessary.
FACTORS THAT MAY DISTURB
ALIGNMENT
The unit should be checked periodically for alignment.
If the unit does not stay in line after being properly
installed, the following are possible causes:
1. Settling or spring of the foundation.
2. Wear of bearings.
3. Pipe strains distorting or shifting the machine.
4. Shifting of the sub-base due to heat created from
an adjacent heat source.
5. Shifting of the building structure due to variable
loading or other causes.
6. Loose nuts or bolts on the pump or driver
assembly.
NOTE: With experience, the installer will
understand the interaction between angular and
parallel and will make corrections appropriately.
IMPELLER ALIGNMENT
GENERAL
Improper impeller adjustment could cause
contact between the rotating and stationary
parts, resulting in a spark and heat
generation.
The impeller clearance setting procedure
must be followed. Improperly setting the
clearance or not following any of the proper
procedures can result in sparks, unexpected
heat generation and equipment damage.
The AF impeller has been aligned at the factory but
should be checked prior to pump operation. The
impeller requires several thousandths of and inch of
clearance to prevent rubbing due to the action of
hydraulic forces when the pump is operating. Many
corrosion-resistant alloys will gall and build up if
rubbing occurs, therefore, pumps using these alloys
need to be free from any rubbing.
Turn the shaft by hand, if the impeller rubs the inside
of the elbow or casing it must be realigned. The
following steps are used to align the impeller.
There are (2) types of impeller adjustment for the AF
pump.
Type 1
has adjusting lugs on the stuffing box
cover,
Type 2
has adjusting lugs on the elbow. Type 1
moves the back-pullout relative to the elbow. Type 2
moves the casing relative to the impeller to set the
clearance (see Figs. 22 and 23).
Note: Impeller rubbing is often caused by pipe
strain or belt tension. Pipe strain must be
eliminated prior to impeller alignment. The
impeller should aligned after proper belt
tensioning.
Clearance measurement -
The alignment worksheet
on page 28 is used to align the impeller of the AF
pump. The measurement procedure is as follows:
Summary of Contents for Goulds Pumps AF
Page 1: ...Installation Operation and Maintenance Instructions Model AF 6 36 MXR Bearings ...
Page 3: ...AF 6 36 IOM 6 THIS PAGE INTENTIONALLY LEFT BLANK ...
Page 5: ...AF 6 36 IOM 8 THIS PAGE INTENTIONALLY LEFT BLANK ...
Page 14: ...10 AF 6 36 IOM THIS PAGE INTENTIONALLY LEFT BLANK ...
Page 32: ...28 AF 6 36 IOM ...
Page 34: ...30 AF 6 36 IOM THIS PAGE INTENTIONALLY LEFT BLANK ...
Page 48: ...44 AF 6 36 IOM THIS PAGE INTENTIONALLY LEFT BLANK ...
Page 66: ...62 AF 6 36 IOM AF SECTIONAL shown with optional restrictor bushing adapter Fig 77 ...
Page 68: ...64 AF 6 36 IOM AF OPTIONS Fig 78 351 370F 126 ...
Page 69: ...AF 6 36 IOM 65 MXR BEARING CONFIGURATIONS 1MXR 3MXR 4MXR 6MXR Fig 79 540C 6 ...
Page 72: ...68 AF 6 36 IOM THIS PAGE INTENTIONALLY LEFT BLANK ...