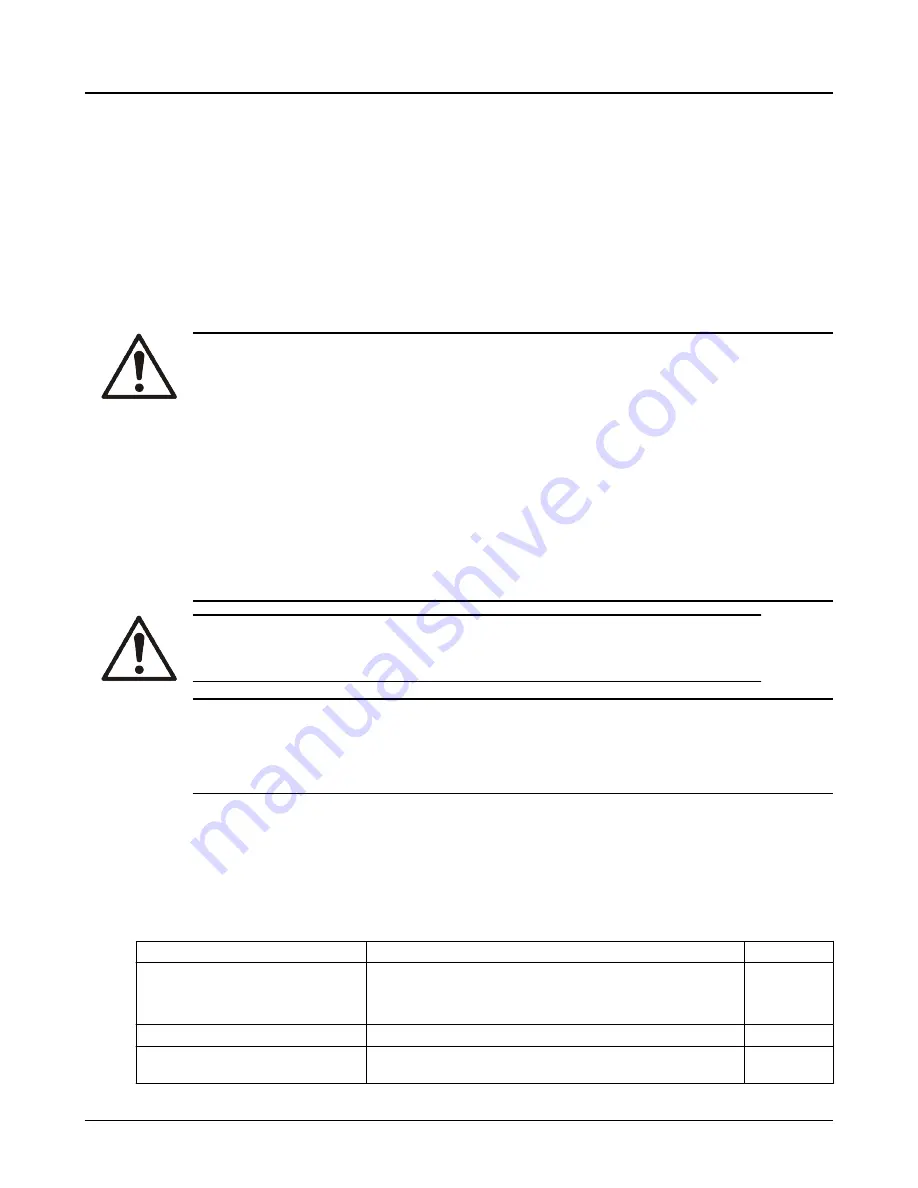
When a minimum-flow orifice is unavailable
Consider an automatic recirculation control valve or solenoid-operated valve if a constant bypass (mini-
mum-flow orifice) is not possible.
4.7 Piping checklists
4.7.1 General piping checklist
Precautions
WARNING:
•
Risk of premature failure. Casing deformation can result in misalignment and contact with
rotating parts, causing excess heat generation and sparks. Flange loads from the piping
system, including those from the thermal expansion of the piping, must not exceed the
limits of the pump.
•
Risk of serious personal injury or property damage. Fasteners such as bolts and nuts are
critical to the safe and reliable operation of the product. Ensure appropriate use of fasten-
ers during installation or reassembly of the unit.
•
Use fasteners of the proper size and material only.
•
Replace all corroded fasteners.
•
Ensure that all fasteners are properly tightened and that there are no missing fas-
teners.
CAUTION:
•
Do not move the pump to the pipe. This could make final alignment impossible.
NOTICE:
Vary the capacity with the regulating valve in the discharge line. Never throttle the flow from the
suction side. This action can result in decreased performance, unexpected heat generation,
and equipment damage.
Piping guidelines
Guidelines for piping are given in the Hydraulic Institute Standards available from the Hydraulic Institute
at 9 Sylvan Way, Parsippany, NJ 07054-3802. You must review this document before you install the
pump.
Checklist
Check
Explanation/comment
Checked
Check that all piping is supported in-
dependently of, and lined up naturally
with, the pump flange.
•
Strain on the pump
•
Misalignment between the pump and the drive unit
•
Wear on the pump bearings and the coupling
Keep the piping as short as possible. This helps to minimize friction losses.
Check that only necessary fittings are
used.
This helps to minimize friction losses.
4.7 Piping checklists
Models 3180, 3181, 3185, and 3186 Installation, Operation, and Maintenance Manual
41