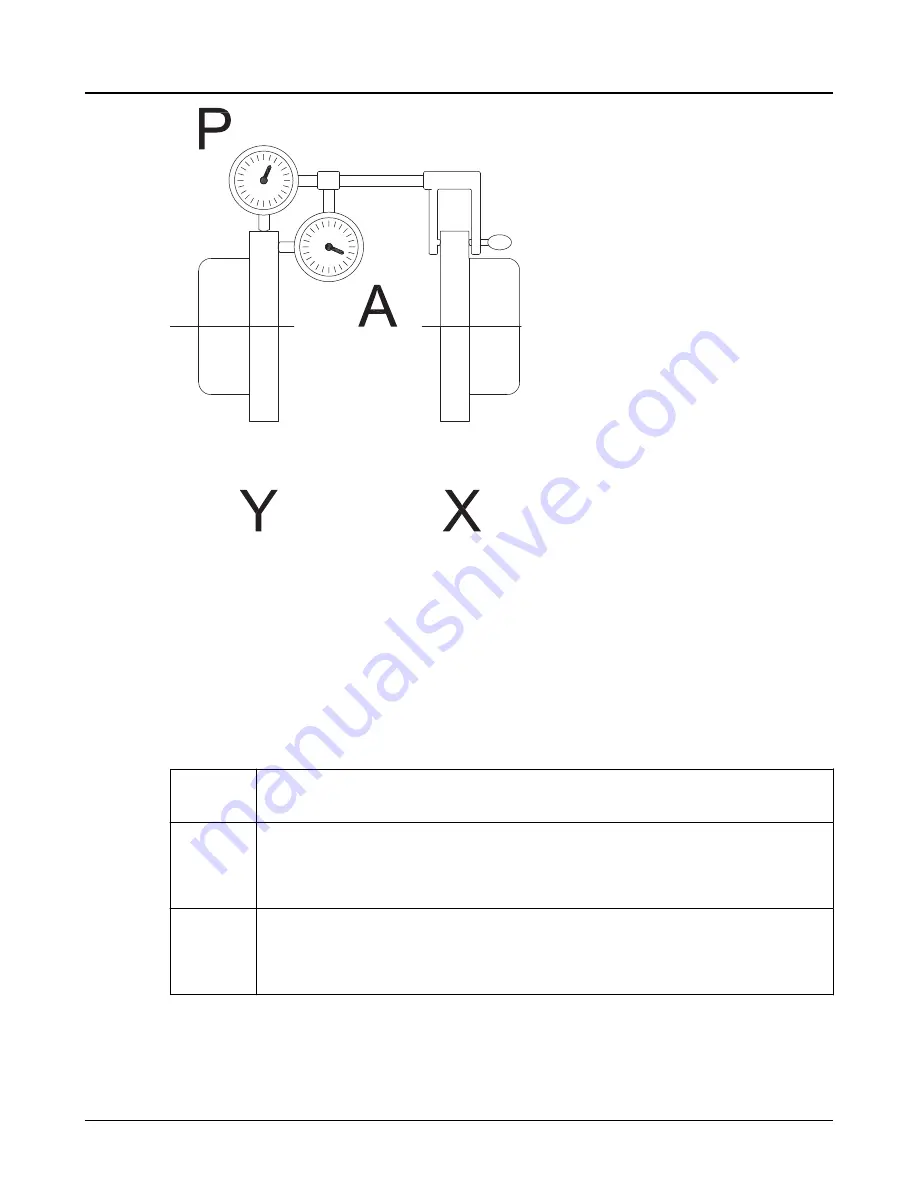
Figure 11: Dial indicator attachment
2.
Rotate the pump coupling half (X) in order to check that the indicators are in contact with the driver
coupling half (Y) but do not bottom out.
3.
Adjust the indicators if necessary.
4.4.5 Perform angular alignment for a vertical correction
1.
Set the angular alignment indicator to zero at the top-center position (12 o’clock) of the driver cou-
pling half (Y).
2.
Rotate the indicator to the bottom-center position (6 o’clock).
3.
Record the indicator reading.
When the
reading val-
ue is...
Then...
Negative
The coupling halves are farther apart at the bottom than at the top. Perform one of
these steps:
•
Add shims in order to raise the feet of the driver at the shaft end.
•
Remove shims in order to lower the feet of the driver at the other end.
Positive
The coupling halves are closer at the bottom than at the top. Perform one of these
steps:
•
Remove shims in order to lower the feet of the driver at the shaft end.
•
Add shims in order to raise the feet of the driver at the other end.
4.4 Pump-to-driver alignment
26
3610 i-FRAME API 610 11th Ed/ISO 13709 2nd Ed, API Type BB1 Single-Stage, Axially-Split, Between-Bearing IOM
Summary of Contents for 3610 i-FRAME
Page 2: ......