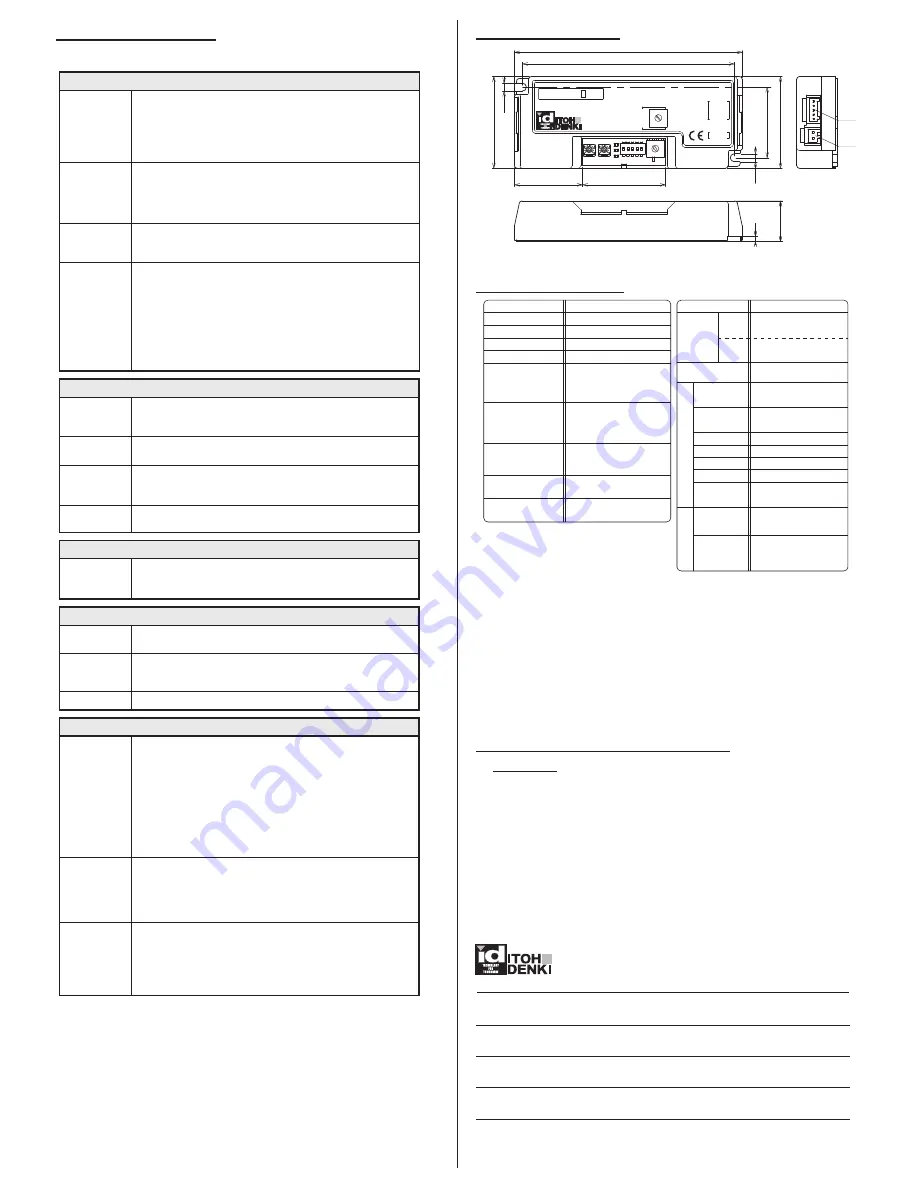
Type of brake
Dynamic brake
*1
3-00K-1710
11 Specifications
12 Applicable standards
(
-UL
)
10 Dimensions
6
5
4
0 1
9
8
7
2
3
CB-016
6
VR1-ACC
VR2-DEC
STATUS/ERR/PWR
5. L/H
SPEED
1. AUTO/MANU
3. DIRECTION
2. INT/EXT
4. E/N-OUT
CN2
CN1
24V
1.RUN
3.V-IN
2.DIR
4.ERR
5.PLS
0V
56
7
8
9 0 1 2
3
4
4.5
52
47
38.5
40
4.5
52
122
129
3
23
Symptom 5 Error Signal is often Discharged
Environment
•
Check if the LED 2 is blinking.
» If this is the case, see section 8 in page 7 and remove the
cause of error.
•
Check if the wire diameter of the power supply is appropriate
(0.5 to 1.5mm
2
).
Also, check if there is no failure in wiring or no looseness at
connectors.
» Check the wire diameter and wirings.
•
Check if CB-016 is too far from the power supply.
(Check if the voltage is dropped.)
•
Check if the product is used in the ambient temperature range
between 0 and 40
℃
.
•
Check if the driver card back plate is affixed to the metallic
plate face for better heat dissipation.
•
Check if the MDR is stalled in the conveyor line.
•
Check if the MDR end housing is contacting the conveyor
frame.
•
Check if the MDR's connector is properly inserted to the
driver card.
•
Check if the Poller cable is disconnected, or about to
disconnect.
LED 2 (red)
MDR
*1
CB-016 driver card having LT option is used in the ambient temperature range
between -30 and 10
℃
. (no condensation)
*1
MDR connector
Timing of brake
effected after
stop signal
Ambient
temperature
0 to +40
℃
Atmosphere
No corrosive gas
Vibration
≦
0.5G
Relative
humidity
≦
90%RH
(no condensation)
0.2A from start to
100msec and
0.125A thereafter
Power voltage
24VDC ±10%
(
±5%
)
24VDC
Protections
Integral 6.3A fuse (+ side)
Diode against miss-wiring
95
℃
on PCB or
105
℃
in motor
Error signal
discharge
Power (green)
Error (red)
Frequency (red/orange)
LED
Thermister
JST P/N S9B-XH-A
NPN (or PNP)
Open collector output
(should be set to 25mA to
less max output current)
*3
*5
*2
*7
Rated voltage
0.03A
Static current
20A , 1msec or less
Peak current
4.0A
Starting current
Motor starts running
from RUN signal
≦
15msec
200msec
Brake
current
Connector
(wiring side)
Power
Control
P/N 734-102 (10A max)
P/N 733-105 (4A max)
No holding effect. In case holding effect is required, use MDR with built-in brake option (BR)
together with CB-016[BN6][BP6].
In case of CB-016[BS6][BP6], connector P/N is S10B-XH-A
ElectroMagnetic brake, which is disengaged from the motor when powered, and is engaged
to the motor to stop inertia when power is off.
*1
*2
*3
*4
*5
*6
*7
Specifications are subject to change without prior notice.
Environment
Mechanical Brake
Contacts:
Headquarters: Itoh Denki Co.,Ltd.
Phone: +81 (0)790 47 1225 Fax: +81 (0)790 47 1325 www.itohdenki.co.jp
Europe, Middle East, Africa: Itoh Denki Europe SAS
Phone: +33 (0)4 50 03 09 99 Fax: +33 (0)4 50 03 07 60 www.itoh-denki.com
North & South America: Itoh Denki USA, Inc
Phone: +1 570 820 8811 Fax: +1 570 820 8838 www.itohdenki.com
Asia/Oceania: Itoh Denki Asia Limited
Phone: +852 2427 2576 Fax: +852 2427 2203
China: Itoh Denki Shanghai Company Limited
Phone: +86 21 6341 0181 Fax: +86 21 6341 0180 www.itohdenki.com.cn
*4
*6
*6
CB-016 driver card having LT option is used in the ambient temperature range between -30
and 10
℃
. (
no condensation
)
In case of using UL recognized product.
Symptom 4 Error Signal Not Discharged
Voltage
•
Check if the setting is made properly for discharge on normal
or discharge when error arises.
•
Check if the external voltage is 24VDC or less and its 0V is
common to the 0V input to CN1-2.
•
Check if the resistor larger than 1k
Ω
is mounted.
•
Check if the wiring is adequately done to CN2-4.
SW1-4
CN2-4
9 Troubleshooting
*
Follow the procedures below without removing plastic cover or modifying the driver
card, in case any problem happens.
Symptom 1: MDR does not run
Power
RUN signal
Error
MDR
•
Check if only LED 1 (green) illuminates
.
•
Check if 24VDC stable voltage is adequately supplied from
the power supply.
•
Check if the wiring to CN1 connector is made correctly
.
•
Check if 24VDC cable is adequately wired to the CN 1
connector
.
•
Check if 0V is injected to CN2-1
.
•
Check if the 0V injected to CN2-1 is common to 0V injected
to CN1-2
.
•
Check if the wiring is adequately made to CN2-1 connector
.
•
Check if the SW2 is set to NPN
.
•
Check if LED 2 is illuminating or blinking
.
» If this is the case, see section 8 and remove the cause of
error.
•
Check if the MDR is adequately installed and its shafts are
adequately fixed with the supplied mounting brackets or
accessories.
•
Check if the MDR end housing is NOT contacting conveyor
frame.
•
Check if the MDR's connector is properly inserted to the
driver card.
•
Check if the o-ring or belt tension is not too strong.
Check if the number of slaved idler rollers is adequate.
Symptom 2 : Speed variation is not achieved, or speed is slower than expected
Power
MDR
•
Check if the nominal speed of the MDR to see if the right
model is used to achieve the speed variation or to reach
expected speed.
•
Check if the SW1-2 is set properly: ON for external speed
variation and OFF for internal speed variation.
•
In case of external speed variation, check if the 0V is common
to the 0V input to CN1-2.
•
Check if the stable 24VDC is supplied.
•
Check if the wiring is adequately made to CN2-3 connector.
•
Check if the analog voltage input is made between 0 and 10V.
SW1-2 setting
CN2-3
Symptom 3 Reversing is not achieved
CW/CCW
•
Check if 0V is injected to CN2-2, and it is common to the 0V
input to CN1-2.
•
Check if the wiring is adequately made to CN2-1.
(
12
)
(
13
)
Installation
Pollution level
Overvoltage
category
Indoor
2
2
Conforming to IEC60640-1 and UL840
Please select and use an appropriate cable according to the voltage used, the current, and
the environment. There is a fear of a leak or a fire when an inappropriate cable is used.
(Wire diameter : AWG20
〜
14)
(Wire diameter : AWG28
〜
20)
UL and CSA
UL508C and CSA C22.2-No.274 (Recognized component)
- Category Code No. (CCN) : NMMS2, NMMS8
- File No. : E333970