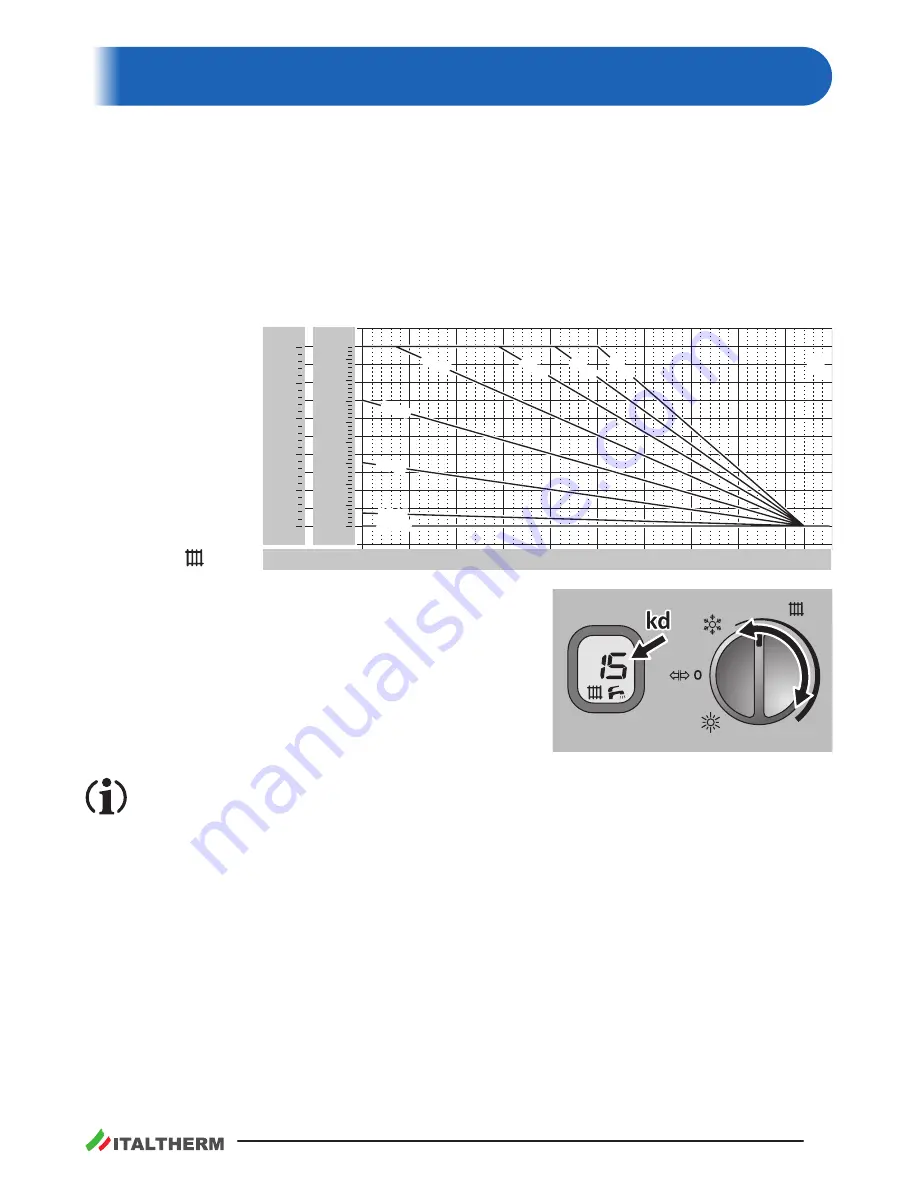
Green Heating Technology
51
Addendum
Outdoor Sensor Kit
Installation and setting
The Outdoor Sensor manages automatically the CH flow temperature** as a function of the outdoor
temperature, thus avoiding the user to adjust it manually. This function is also named
"shifting tempera
-
ture"
.
**
that's
the temperature of the heating elements. Don't mistake it with the room temperature (managed by the room thermo
-
stat or by the Remote Control, but not by the boiler) that doesn't depend on the first one.
The installation must
be made by a profes-
sionally skilled tech-
nician
following the
instructions supplied
with the kit. Refer to
"Electrical diagram" on
page 49 for the links to
the Main Board.
After the installation of
the Sensor,
the Sum-
mer/Winter
knob
won't adjust directly
the CH flow temperature, but the dispersion factor
"kd"
that's
the response of the outdoor temperature, detected by the sen
-
sor, on the CH flow temperature (see graph).
Practically,
kd
value should be adjusted depending on the esti
-
mated efficiency of the building's thermal insulation. Its range
is from 01 to 30:
use
higher values
when there is a
high ther-
mal dispersion
and therefore a less efficient insulation (and
vice versa).
Because of the wide buildings typologies, it's impossible to give precise indications on kd value
to set. The correct setting must be determined case by case and will have, as a result, an opti
-
mal comfort in all the climatic conditions
requiring heating, i.e. a prompt reaching of the room
temperature with cold weather and no room overheating during mild periods.
Outdoor Sensor kit and Remote Control
If also the Remote Control Kit is installed, its parameter
P04
(modulation mode) should be set on val-
ue
2
(modulating on outdoor sensor and on-off on room sensor) or
3
(modulating on both outdoor and
room sensors) as described in the
paragraph 5
of the instruction booklet included in the Remote Con-
trol Kit. Afterwards, also the
kd
should be set on this latter (refer to
paragraph 8.6
of the same booklet).
On the Remote Control, just because of different display, the
kd
adjustment range is
0.1…3.0
instead
of 01…30.
00178 00
35
40
45
50
55
60
65
70
75
78
MAX
MIN
High temperature range 35÷78 °C
–20
t
ext
(°C)
–15
–10
–5
0
5
10
15
20
25 27
20
25
30
35
40
45
MAX
MIN
Low temperature range 20÷45 °C
(if available)
(kd=00)
kd=05
kd=01
kd=10
kd=15
kd=20
kd=25
kd=30
00177
ENG 00