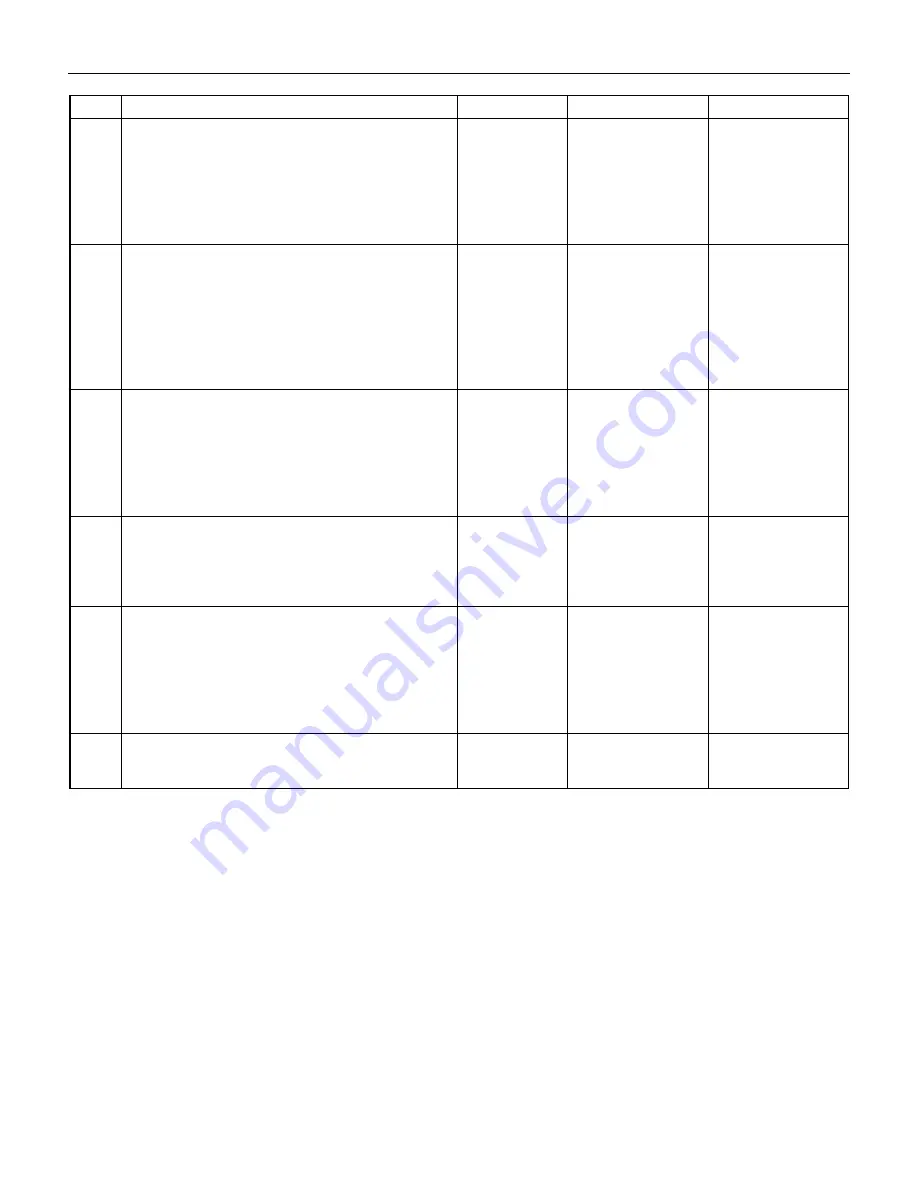
6E-216 Engine Control System (4JH1)
Step Action
Value(s)
Yes
No
14
1. Turn OFF the ignition.
2. Disconnect the PCU harness connector.
3. Inspect for an intermittent and for poor
connections at the harness connector of the PCU
(pins 1 and 2 of E-6 connector).
4. Repair the connection(s) as necessary.
Did you find and correct the condition?
Go to Step 18
Go to Step 16
15
1. Turn OFF the ignition.
2. Disconnect the ECM harness connector.
3. Inspect for an intermittent and for poor
connections on the CAN Low or High circuits at
the harness connector of the ECM (pins 23 and
24 of C-57 connector).
4. Repair the connection(s) as necessary.
Did you find and correct the condition?
Go to Step 18
Go to Step 17
16
Important:
The fuel injection pump must be timed to
the engine.
Replace the fuel injection pump. Refer to Fuel
Injection Pump Replacement in engine mechanical
section. (PCU is part of the fuel injection pump
assembly)
Did you complete the replacement?
Go to Step 18
17
Important:
Replacement ECM must be
programmed.
Replace the ECM. Refer to Engine Control Module
(ECM) Replacement in this section.
Did you complete the replacement?
Go to Step 18
18
1. Reconnect all previously disconnected harness
connector(s).
2. Clear the DTCs with the scan tool.
3. Turn OFF the ignition for 30 seconds.
4. Start the engine.
5. Monitor the DTC Information with the scan tool.
Does the DTC fail this ignition?
Go to Step 2
Go to Step 19
19
Observe the DTC Information with the scan tool.
Are there any DTCs that you have not diagnosed?
Go to Diagnostic
Trouble Code (DTC)
List System
OK
Summary of Contents for 4ja1
Page 2: ......
Page 34: ...6A 12 ENGINE MECHANICAL Cooling and Lubricating System N m kg m lb ft RTW46AXF000701...
Page 35: ...ENGINE MECHANICAL 6A 13 Intake Manifold 4JA1TC 4JH1TC N m kg m lb ft RTW36AXF000201...
Page 36: ...6A 14 ENGINE MECHANICAL EGR Valve EGR Pipe EGR Cooler RTW46AXF000801...
Page 37: ...ENGINE MECHANICAL 6A 15 Exhaust Manifold and Turbocharger 4JA1L RTW46AXF000901...
Page 39: ...ENGINE MECHANICAL 6A 17 Engine Electricals N m kg m lb ft RTW36AXF000501...
Page 40: ...6A 18 ENGINE MECHANICAL Fuel Injection System 4JA1L N m kg m lb ft RTW86AXF000201...
Page 41: ...ENGINE MECHANICAL 6A 19 Fuel Injection System 4JA1TC N m kg m lb ft RTW46AXF001201...
Page 42: ...6A 20 ENGINE MECHANICAL Fuel Injection System 4JH1TC N m kg m lb ft RTW46AXF001301...
Page 43: ...ENGINE MECHANICAL 6A 21 Engine Mounting Bracket N m kg m lb ft 022R300001...
Page 162: ...MEMO...
Page 187: ...FUEL SYSTEM 6C 5 For EURO III model RTW46AMF000201...
Page 220: ...MEMO...
Page 225: ...ENGINE ELECTRICAL 6D 5 TORQUE SPECIFICATIONS GENERATOR N m kg m Ib ft RTW86DLF000101...
Page 226: ...6D 6 ENGINE ELECTRICAL STARTER MOTOR N m kg m Ib ft RTW86DLF000201...
Page 254: ...MEMO...
Page 261: ...Engine Control System 4JH1 6E 7 Engine Controls Schematics Power Distribution 1 RTW86EXF004801...
Page 262: ...6E 8 Engine Control System 4JH1 Power Distribution 2 RTW86EXF004901...
Page 263: ...Engine Control System 4JH1 6E 9 Starting System RTW86EXF005001...
Page 264: ...6E 10 Engine Control System 4JH1 Charging System RTW86EXF005101...
Page 265: ...Engine Control System 4JH1 6E 11 ECM Power and PCU RTW86EXF003001...
Page 266: ...6E 12 Engine Control System 4JH1 ECM Ground and DLC RTW86EXF005201...
Page 267: ...Engine Control System 4JH1 6E 13 Gauges and Warning Lamps RTW86EXF003201...
Page 269: ...Engine Control System 4JH1 6E 15 MAF IAT Vacuum Pressure and ECT Sensors RTW86EXF003401...
Page 275: ...Engine Control System 4JH1 6E 21 1 Legend 1 Vehicle Speed Sensor VSS...
Page 536: ...MEMO...
Page 558: ...6H 2 ACCELERATOR CONTROL REMOVAL AND INSTALLATION 4JA1T L RHD RTW46HLF000301...
Page 559: ...ACCELERATOR CONTROL 6H 3 4JA1T L LHD RTW46HLF000601...
Page 560: ...6H 4 ACCELERATOR CONTROL 4JA1TC 4JH1TC RHD RTW46HLF000201...
Page 561: ...ACCELERATOR CONTROL 6H 5 4JA1TC 4JH1TC LHD PTW46BMF000101...
Page 564: ...No TF4JE WE 1101...