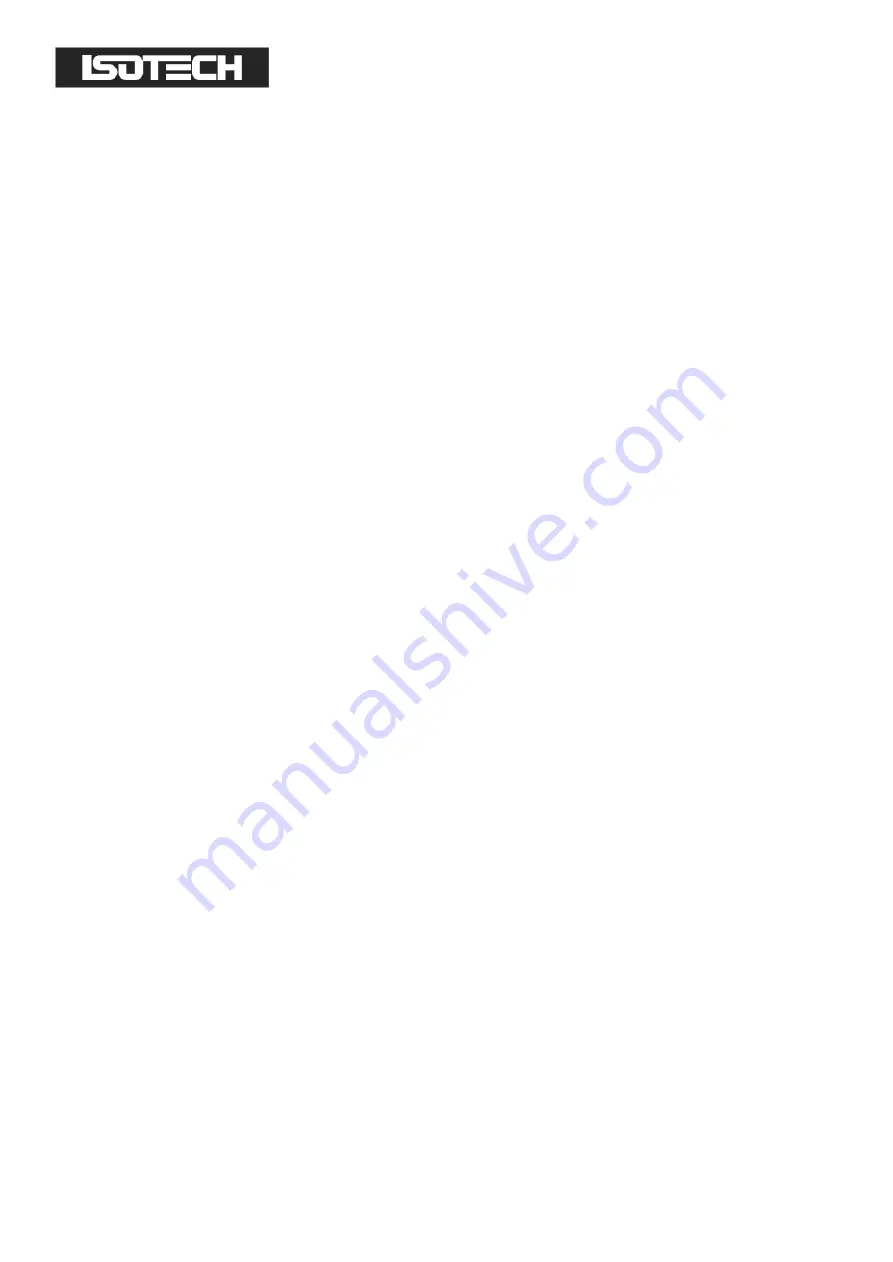
Page 9 of 43
Low Temp Furnace Model ITL-M-17701 13-07/20
THE LOW-TEMPERATURE FURNACE
The low-temperature furnace for realisation of metal freezing points is based on the design of Chattle (p.65,
"Supplementary Information for the International Temperature Scale of 1990," B.I.P.M., 1990). It is
furnished with two independent control systems, one for temperature control using a PRT and the other for
over-temperature protection using a type N Thermocouple.
INTRODUCTION
The Isotech Low Temperature Fixed Point Furnace is designed specifically to realize and maintain the
freeze plateaux of Isotech Indium, Tin and Zinc Fixed Point Cells, for calibration of thermometers on the
International Temperature Scale of 1990.
The Low Temperature Furnace is a single-zone furnace. The recommended procedure for establishing a
freeze plateau requires operator attention until the plateau is realized. Following that, the Model 17701
Furnace will maintain the plateau, essentially automatically, for a period of 10 to 12 hours.
The furnace core, into which the freeze-point cell is inserted, is of Aluminium alloy, which provides a very
low thermal gradient along the core length. The main furnace heater is of the parallel-tube design as used
at NIST. A pre-warming tube is provided.
Two entirely independent over-temperature safety devices are included. A dedicated (on-off) over
temperature control circuit provides active safety. A fusible link in the main power circuit provides passive
safety.
The Low Temperature Furnace is completely self-contained, castor mounted and requires no external
supplies (except power).
NEW FEATURES
The furnace has been upgraded to benefit from the latest technology. Fitted with a crystal clear colour
display the furnace is now fully programmable. Programs can be created for the furnace to switch between
set temperatures, for example to bring the furnace to the melt or freeze temperature at a desired time, or to
lower the furnace temperature after a predetermined time.
The PID control parameters are now dynamically optimised at different temperatures optimizing furnace
stability. An Ethernet interface allows the furnace temperature to be monitored across a network whilst a
USB Interface allows programs to be copied or for the furnace heat up and cool down history to be
exported.