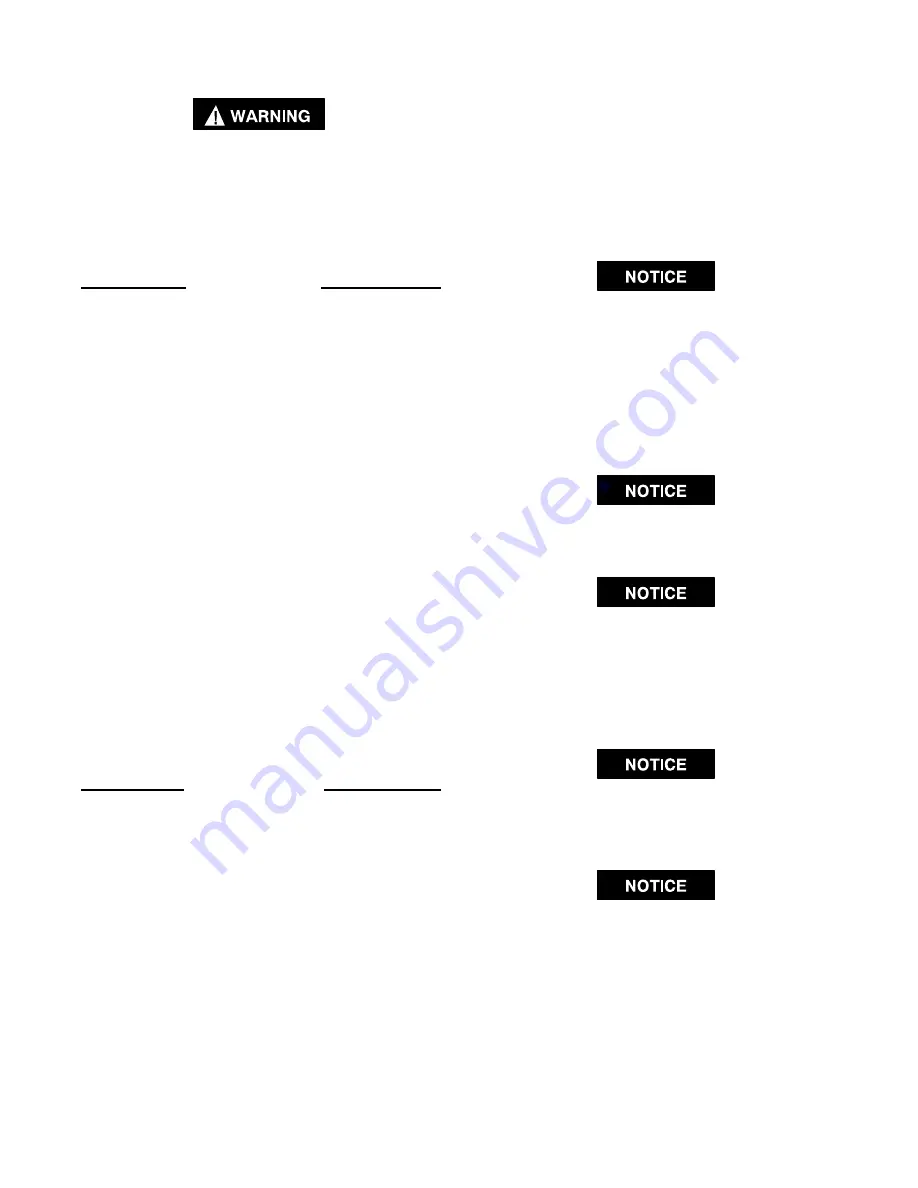
18
MAINTENANCE SECTION
Always wear eye protection when operating or
performing maintenance on this tool.
Always turn off air supply and disconnect air supply
hose before installing, removing or adjusting any
accessory on this tool, or before performing any
maintenance on this tool.
LUBRICATION
Each time the Series 6L Angle Drills are disassembled for
maintenance, repair or replacement of parts, lubricate the
tool as follows:
1. Moisten all O–rings with O–ring lubricant.
2. Work approximately 1.5 cc of grease into the Rear
Rotor Bearing (21), Front Rotor Bearing (28) and the
Spindle Bearing (48).
3. Work approximately 6 cc to 8 cc of grease into the H,
J, JJ, K or L ratio gear train and 10 cc to 12 cc of
grease into the M, P or R ratio gear train. Grease the
Planet Gear Bearings (32, 35, 39 and 42), the gear
teeth inside the Gear Case (44) and the planet gear
shafts on the Spindle (29) and Gear Head (38).
4. Work approximately 0.5 cc to 1.0 cc of grease into the
Lower Spindle Bearing (119).
5. Work approximately 0.5 cc to 1.0 cc of grease into the
Upper Spindle Bearing (104 or 105), Bevel Pinion
Bearing (109) and Bevel Pinion Thrust Bearing (112).
Apply 6 cc to 8 cc of grease to the Matched Bevel
Gear Set (107) used in 7L3A4 Angle Attachments,
2 cc to 4 cc of grease to the Matched Bevel Gear Set
used in 7L2A4 Angle Attachments and a maximum of
0.5 cc of grease to the bevel gears of the Spindle
Assembly (108) used in 7L1A1 Angle Attachments.
DISASSEMBLY
General Instructions
1.
Do not disassemble the tool any further than
necessary to replace or repair damaged parts.
2.
Whenever grasping a tool or part in a vise, always use
leather–covered or copper–covered vise jaws to
protect the surface of the part and help prevent
distortion. This is particularly true of threaded
members and housings.
3.
Do not remove any part which is a press fit in or on
a subassembly unless the removal of that part is
necessary for repairs or replacement.
4.
Do not disassemble the tool unless you have a
complete set of new gaskets and O–rings for
replacement.
Disassembly of Angle Attachment
1. Remove the Drill Chuck by inserting the short leg of a
1/4” hex key into the Chuck and tightening the
Chuck. Rap the long leg of the key sharply with a
hammer to remove the Chuck.
2. Carefully grasp the flats of the Coupling Nut (124) in
copper–covered vise jaws, Angle Head (101) facing
down.
Gear Case has left–hand threads.
3. Using a wrench on the flats of the Gear Case (44),
loosen but do not remove the Gear Case from the
Coupling Nut.
Remove the tool from the vise. Unscrew and remove
the Coupling Nut from the Gear Case.
4. Carefully grasp the Angle Head (101) in
leather–covered or copper–covered vise jaws, Spindle
(108 or 122) facing upward.
Spindle Bearing Cap (121) has left–hand threads.
5. For 7L1A1 Angle Head, using a wrench, remove the
Spindle Bearing Cap.
Do not remove the Spindle from the Angle Head
until the bevel pinion of the Spindle Assembly (108)
is pulled outward against the Bevel Pinion Bearing
(109). Failure to do so could damage the Spindle
Upper Bearing (105). If tightness or binding
occurs, check to make sure the bevel pinion has
been pulled outward.
Spindle Bearing Cap has left–hand threads.
For 7L2A4 Angle Head, use a wrench to remove the
Spindle Bearing Cap (121). Withdraw the Spindle
(122) from the Angle Head.
Spindle Bearing Cap has left–hand threads.
For 7L3A4 Angle Head, use No. 8SA32–26 Bearing
Cap Wrench to remove the Spindle Bearing Cap.
Withdraw the Spindle (122) from the Angle Head.
6. Inspect the Lower Spindle Bearing (119) for looseness
or roughness. If either of these conditions exists,
replace the bearing as follows:
a. For 7L1A1 Angle Head, slip the Lower Spindle
Bearing from the Spindle.
Summary of Contents for 6LH1A1
Page 13: ...MAINTENANCE SECTION 13 Dwg TPA1138 1 MOTOR AND GEARING ...
Page 16: ...16 MAINTENANCE SECTION Dwg TPB791 ANGLE ATTACHMENTS ...
Page 26: ...26 NOTES ...
Page 27: ...27 NOTES ...