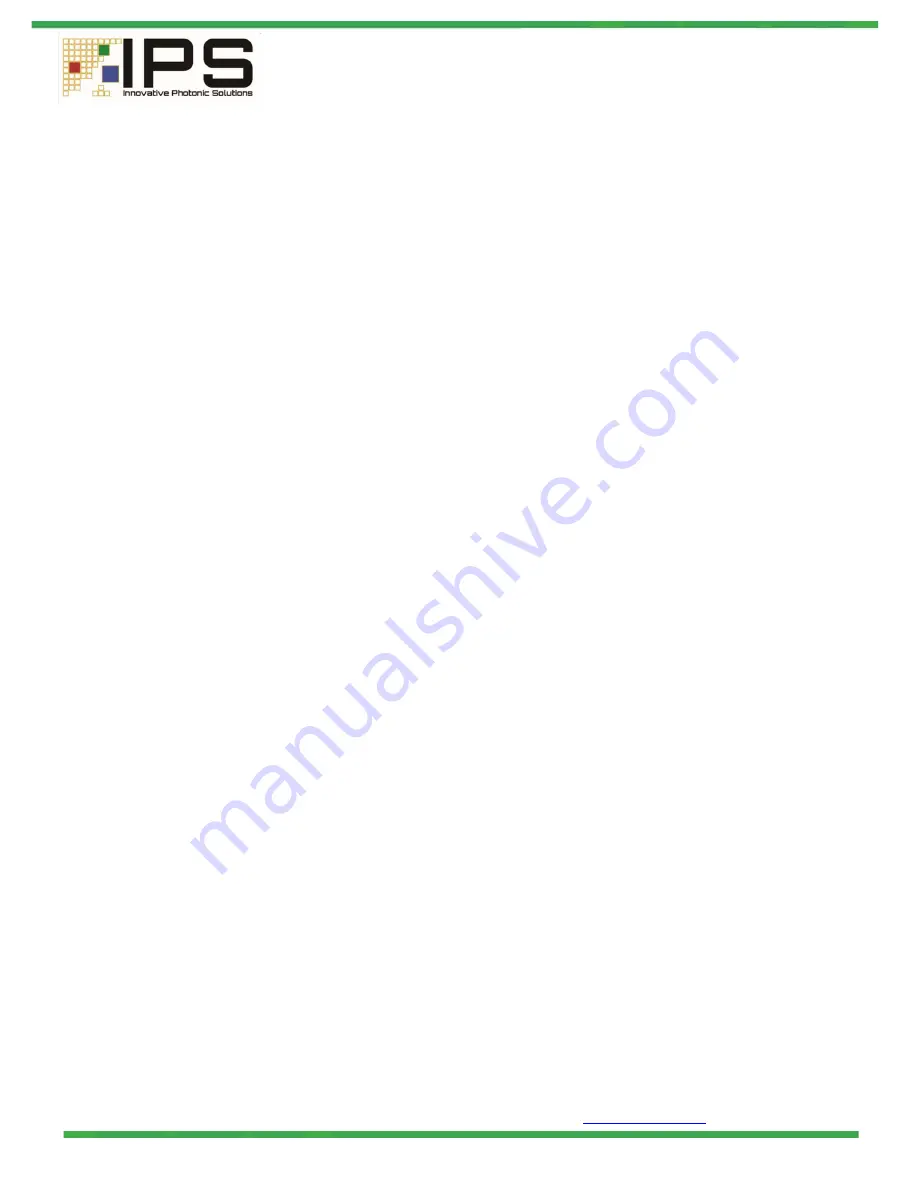
4. Operation
4.1.
Ensure the power supply meets the required specifications especially for voltage,
current and ripple ratings.
4.2.
Ensure the control inputs meet the requirements of the voltage, surge, spike and
ripple requirements.
4.3.
Before the laser is powered on make sure that the control input connected through
pin 7 is pulled high for the laser output to be in the dibbled status, while the input to
Pin 8 is set to low (connecting to negative power supply terminal).
4.4.
The warm up time for the laser and the driver is 5 minutes minimum.
4.5.
After the laser is powered and warmed up, a TTL low at pin 7 (inputting a zero voltage
at pin 7) will enable laser output. Slowly increase the voltages supplied to pin 8 for
desired laser output power.
4.6.
The minimum possible laser output power over its lazing threshold can be determined
through the gradual adjustment of the control input voltage with the observed lazing
threshold point, while the control voltage corresponding to the maximum output power
can also be experimentally determined. For OEM applications the above two control
values need to be saved and applied by the control input source (i,g, system micro-
controller) to match the specific laser/driver set.
4.7.
There is a nearly linear relationship between the supplied control voltage and the
laser output power within the Min and Max range.
4.8.
To ensure the performance of the laser and safety of the personnel, always set pin 7
to High and pin 8 to Low before turning laser-beam on. Always allow sufficient time
(eg. 5 minutes) for the laser to reach its thermal equilibrium.
4.9.
Power off sequence: Set the voltage of pin 8 to zero before powering off the laser’s
power supply.
5. Notes
5.1.
Every laser/driver pair has its unique laser power control voltage values specific to
the matched laser/driver set. Ensure the pair-specific control voltage values
determined are saved and applied correctly to the matched set only.
5.2.
Ensure the 5 minute warm up routine from the system level whenever possible.
5.3.
The laser has a built in isolator mechanism against the reflected laser beam for
maximum possible operation stability in most applications. It is good practice in the
system design to avoid or minimize the reflected beam back into the laser. In special
applications contact the factory, should higher isolation performance be required.
5.4.
The driver unit has been adjusted to work with the specific laser head to the highest
possible performance. Hence neither mismatch of the laser heads to drivers, or
customer alteration to the laser head/driver setting is allowed.
313 Enterprise Drive Plainsboro, NJ 08536
Tel: +1 (732)
230-1601
Web:
www.ipslasers.com
290020438-B
(2021/01/14)
Page
5
of
5
Copyright 2021 IPS Lasers