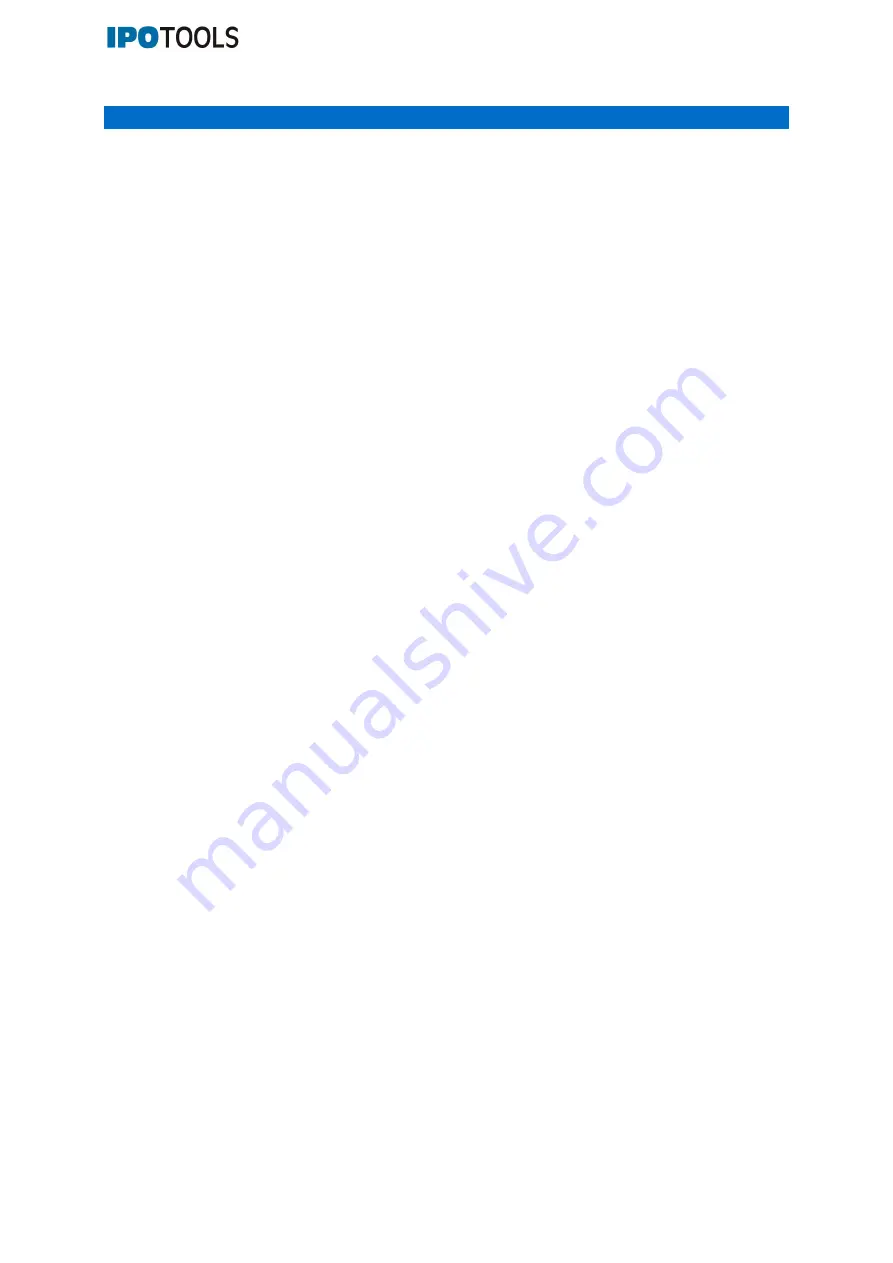
MIG-160ER
3
SAFETY MEASURES
Caution: Improper use of any welding machine can result in injury or death.
CONNECT THE WELDING APPLIANCE ONLY TO THE APPROPRIATE ENERGY SOURCE. This
information is given on the rating plate on the welding machine. When welding outdoors, use only an
extension cord designed for such use.
WORK WITH THE APPLIANCE ONLY ON A DRY AREA AND ON A SOLID GROUND. Make sure the
work area is clean and tidy.
MAKE SURE THERE ARE NO FLAMMABLE SUBSTANCES IN THE WORKING AREA.
KEEP CLEAN CLOTHES WITHOUT TRACE OF GREASE OR OIL AT WORK.
MAKE SURE THE CABLES DO NOT COME INTO CONTACT WITH GREASE OR OIL and never
wrap them around your shoulders.
SAFE WORK WITH CLAMPS or in other means, do not overdo it.
NEVER ESTABLISH AN ARCH ON A PRESSURE GAS TANK.
THE UNINSULATED PART OF THE ELECTRODE HOLDER SHOULD NEVER TOUCH THE
GROUND WHILE THE CURRENT IS FLOWING!
IT IS NECESSARY TO TURN OFF AND DISCONNECT THE CABLES WHEN REPAIRING OR
ADJUSTING THE APPLIANCE. Check the device before each use. Use only original spare parts.
FOLLOW ALL MANUFACTURER'S RULES regarding modification, and adjustment of the device.
APPROPRIATE PROTECTIVE NON-FLAMMABLE CLOTHING AND FOOTWEAR AGAINST HEAT
AND FLAMMES MUST BE CARRIED AT WORK. The welder should be dressed in a work suit made
of non-combustible fibbers during welding. The dress should be dry, clean, not too loose and without
cut-outs or pockets. Shoes should be closed, high. The use of non-flammable gloves, a hat, a
protective mask, and a leather apron is mandatory. Low shoes, self-made fibber dresses and short
gloves are not suitable for welding.
ALWAYS WARE A WELDING MASK WITH APPROPRIATE EYE PROTECTION WHEN WELDING.
Sparks can cause blindness during welding, so always wear protection under the welding mask.
BE CAREFUL OF HOT METAL PARTS, ESPECIALLY WHEN WELDING OVER YOUR HEAD.
Always wear head, arm, leg, and body protection.
MAKE SURE YOU HAVE A FIRE EXTINGUISHER ALWAYS AT YOUR HAND.
DO NOT SKIP THE MACHINE OPERATING CYCLE. The estimated cycle of the welding machine is a
percentage of ten minutes, with this in mind the machine can operate safely in terms of output power.
PREVENT CHILDREN, ANIMALS AND THIRD PARTIES FROM ACCESSING THE WORK AREA.
When storing equipment, make sure it is out of the reach of children.
PROTECT YOURSELF AGAINST ELECTRIC SHOCK. Do not work when you are tired or under the
influence of drugs, alcohol, or other illicit substances. Do not allow the body to come into contact with
grounded surfaces.
SPECIAL WARNINGS:
Welding is not allowed in rooms with flammable and explosive materials,
it is not allowed to weld in / on containers where there were gases, oils, paints…,
more demanding welds should be welded only by certified welders,
persons with a pacemaker should consult a doctor before welding.