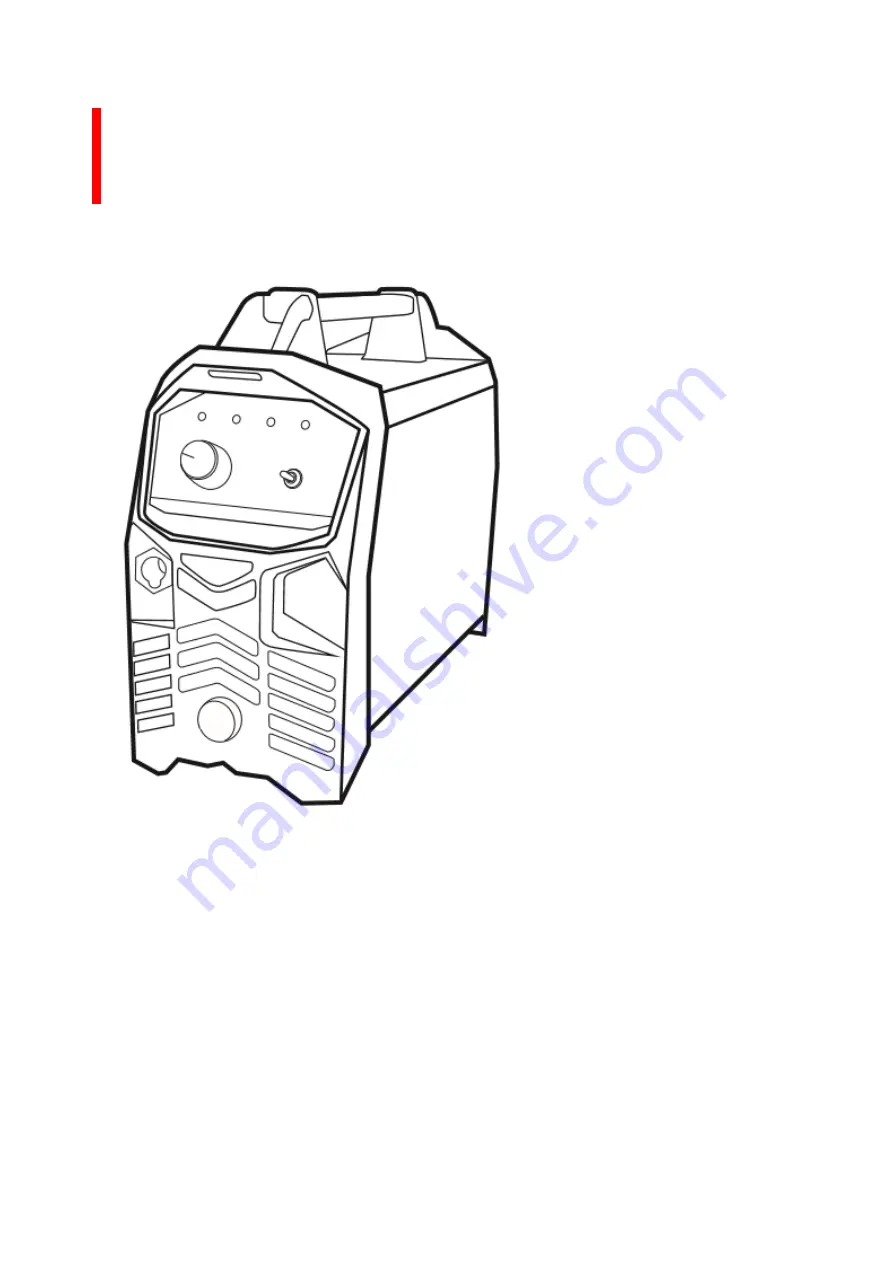
TitanCut 40
PFC
Operators Manual
Issue. A 0516
TitanCut 40
PFC
Operating Manual
Operating manual
EN
Brugsanvisning
DA
Gebrauchsanweisung
DE
Manual de instrucciones
ES
Käyttöohje
FI
Manuel d’utilisation
FR
Manuale d’uso
IT
Gebruiksaanwijzing
NL
Bruksanvisning
NO
Instrukcja obsługi
PL
Manual de utilização
PT
Инструкции по эксплуатации
RU
Bruksanvisning
SV
操作手册
CN
English
TitanCut 40
PFC
Plasma Cutter
Model No.
TCUT40P
Issue.
A 05/16
Summary of Contents for 40 PFC
Page 2: ...TitanCut 40 PFC Operators Manual Issue A 0516 ...
Page 25: ...TitanCut 40 PFC Operators Manual Issue A 0516 3 2 Plasma Torch Operation Start Up ...
Page 26: ...TitanCut 40 PFC Operators Manual Issue A 0516 3 2 Plasma Torch Operation Start Up ...
Page 27: ...TitanCut 40 PFC Operators Manual Issue A 0516 3 2 Plasma Torch Operation Start Up ...
Page 28: ...TitanCut 40 PFC Operators Manual Issue A 0516 3 2 Plasma Torch Operation Start Up ...
Page 32: ...TitanCut 40 PFC Operators Manual Issue A 0516 6 0 Torch Spare Parts Consumables ...
Page 33: ...TitanCut 40 PFC Operators Manual Issue A 0516 6 0 Torch Spare Parts Consumables ...
Page 34: ...TitanCut 40 PFC Operators Manual Issue A 0516 6 0 Torch Spare Parts Consumables ...
Page 35: ...TitanCut 40 PFC Operators Manual Issue A 0516 6 0 Torch Spare Parts Consumables ...
Page 36: ...TitanCut 40 PFC Operators Manual Issue A 0516 6 0 Torch Spare Parts Consumables ...
Page 37: ...TitanCut 40 PFC Operators Manual Issue A 0516 6 0 Torch Spare Parts Consumables ...
Page 38: ...TitanCut 40 PFC Operators Manual Issue A 0516 6 0 Torch Spare Parts Consumables ...
Page 39: ...TitanCut 40 PFC Operators Manual Issue A 0516 7 0 Electrical principle diagram ...