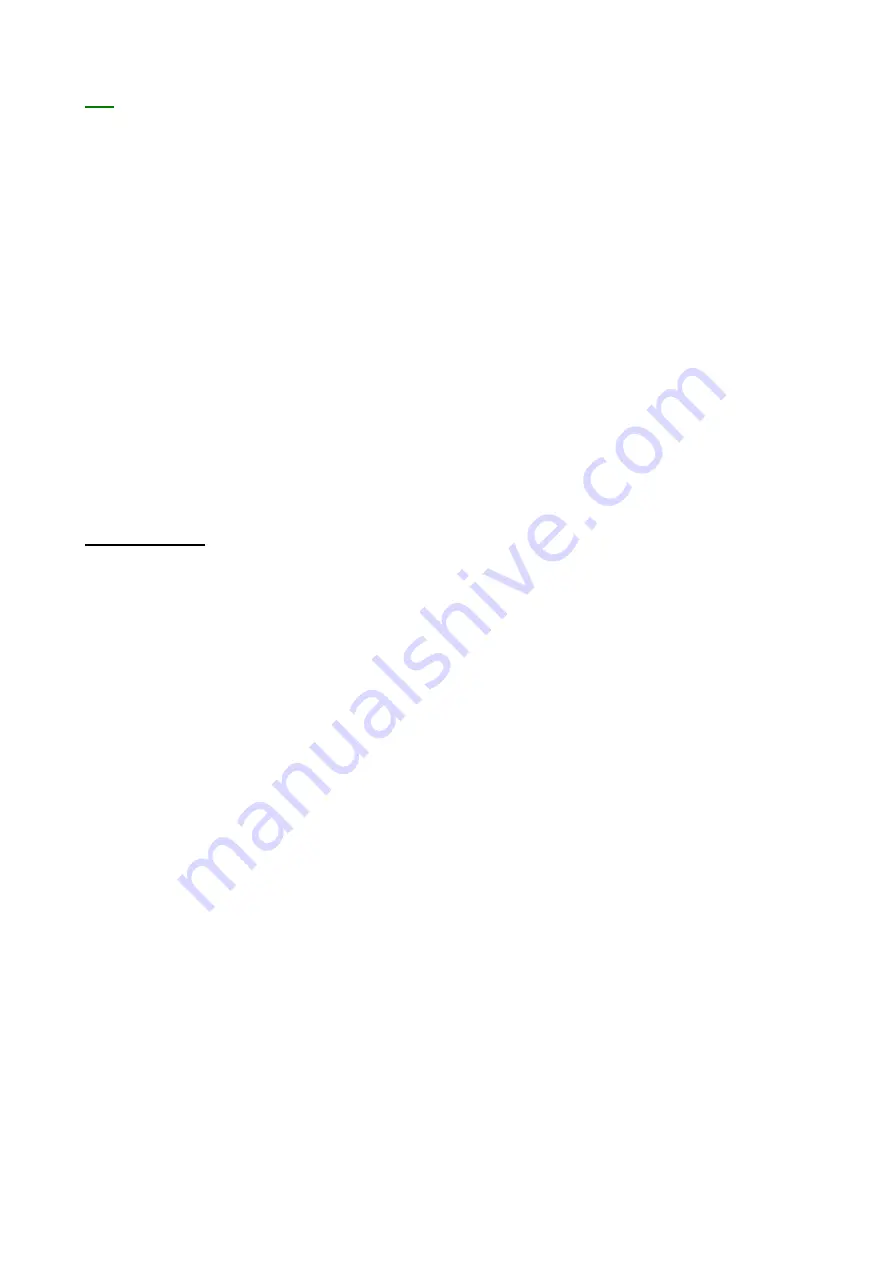
2.1 Installation procedures
Install the necessary accessories in sequence using
Figure B
(page 8) as a guide. An air
control valve (IPM part #601805) for controlling air flow is required. To minimize the risk of
serious injury such as splashing/spraying chemicals on the skin, in the eyes or injury from
moving parts, install the following accessories in your system.
1. Bleed-off master air valve
This valve will relieve the air trapped in the system after pump operation is ceased. Air
that is trapped between this valve and the pump can cause the pump to reciprocate un-
intentionally or un-expectantly and may cause injury to the operator.
2. Fluid Drain Valve
The fluid drain valve is installed to relieve fluid pressure in the pump, hose or at the
dispensing valve when pump operation is ceased. The relief of pressure by the
dispensing valve, which at times is inadequate if there is a clog or other restriction in
the hose or dispensing valve can be achieved by using this fluid drain valve. Always
use a metal valve for grounding purposes.
Lubrication
Connect an air lubricator to help achieve maximum pump longevity. The in-line lubricator
provides proper lubrication to the air motor during operation. (see daily maintenance check,
page 14). Next, install a bleed-off master air valve on the system. This valve is required on
your system to relieve trapped air as explained above.
Air filters help to remove dirt and foreign particles from the supply air. Water moisture will
also be trapped within this filter. Be sure to release the trapped water daily as a good
maintenance practice (see daily maintenance check, page 14). Connect a grounded air
supply hose for main air supply.
For the fluid section, connect one fluid drain valve directly after the outlet of the pump. Be
sure to connect it pointing downwards for safety. Connect a grounded fluid hose to the fluid
outlet 3/4” NPT (female).
Ensure that installation is fully completed before proceeding with start up
operations.
Ensure grounding of the pump and accessories is completed before beginning
pump operation. Observe all OSHA and other safety regulations.