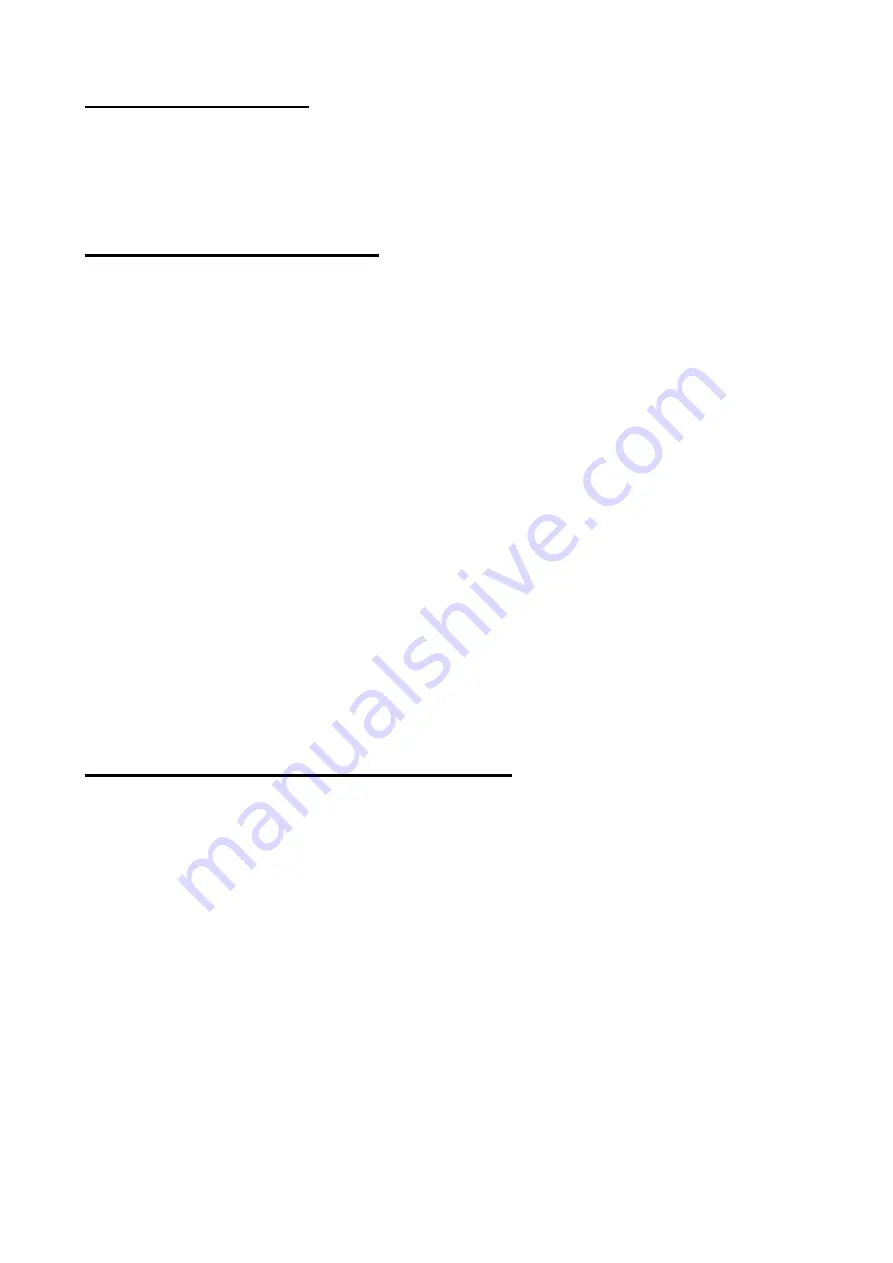
Pressure specification
The maximum working pressure of this equipment for fluids and air is
180 psi (12.5bar
).
Ensure all equipment and accessories used with this pump are rated to withstand the
maximum working pressure of this pump. Never exceed the maximum working pressure of
the pump, hose lines or any other components attached to the pump itself.
Procedure for pressure relief
In order to avoid the risk of serious injury to operators from splashing/spraying chemicals,
the following safety procedures should be used. This procedure should be used when
shutting down the pump, performing general maintenance, repairing a pump or other
components of the system, replacing components or when pumping operation is ceased.
1. Close the air valve to the pump.
2. Use the air bleed down valve (see INSTALLATION, page 8) to relieve the air pressure
in the system.
3. Relieve the fluid pressure by holding a grounded metal pail in contact with the metal
part of the fluid dispense valve and slowly opening the valve.
4. With a container ready to catch the fluid, open the drain valve (see INSTALLATION,
page 8).
5. It is a good practice to leave the drain valve open until it is time to dispense fluid again.
If you are unsure that the fluid pressure has been relieved due to a blockage in a
component or a hose, carefully relieve the pressure by carefully loosening the hose end
coupling to allow the fluid pressure to escape slowly. After the pressure has been relieved,
the fitting can then be removed and any blockages removed.
Flush the pump before initiating operation
1. The pump is tested with lightweight DOP oil, which is left in to protect the pump parts.
If the fluid you are pumping may become contaminated by oil, flush oil from pump with
a compatible solvent before use. Follow the flushing instructions below.
2. When pumping fluids that set up or solidify, flush the system with a compatible solvent
as often as necessary to remove build-up of solidified chemicals in the pump or hoses.
3. If the pump is being used to supply a circulating system, allow the solvent to circulate
through the entire system for at least 30 minutes every 48 hours or more often if
necessary to prevent settling and solidification of chemicals.
4. Always fill the wet-cup 1/2 full of throat seal liquid (TSL) or compatible solvent to keep
the fluid from drying on the displacement rod and damaging pump throat packing.
5. Lubricate the throat packing frequently, when you are pumping a non-lubricating fluid
or are shutting down for more than one day.