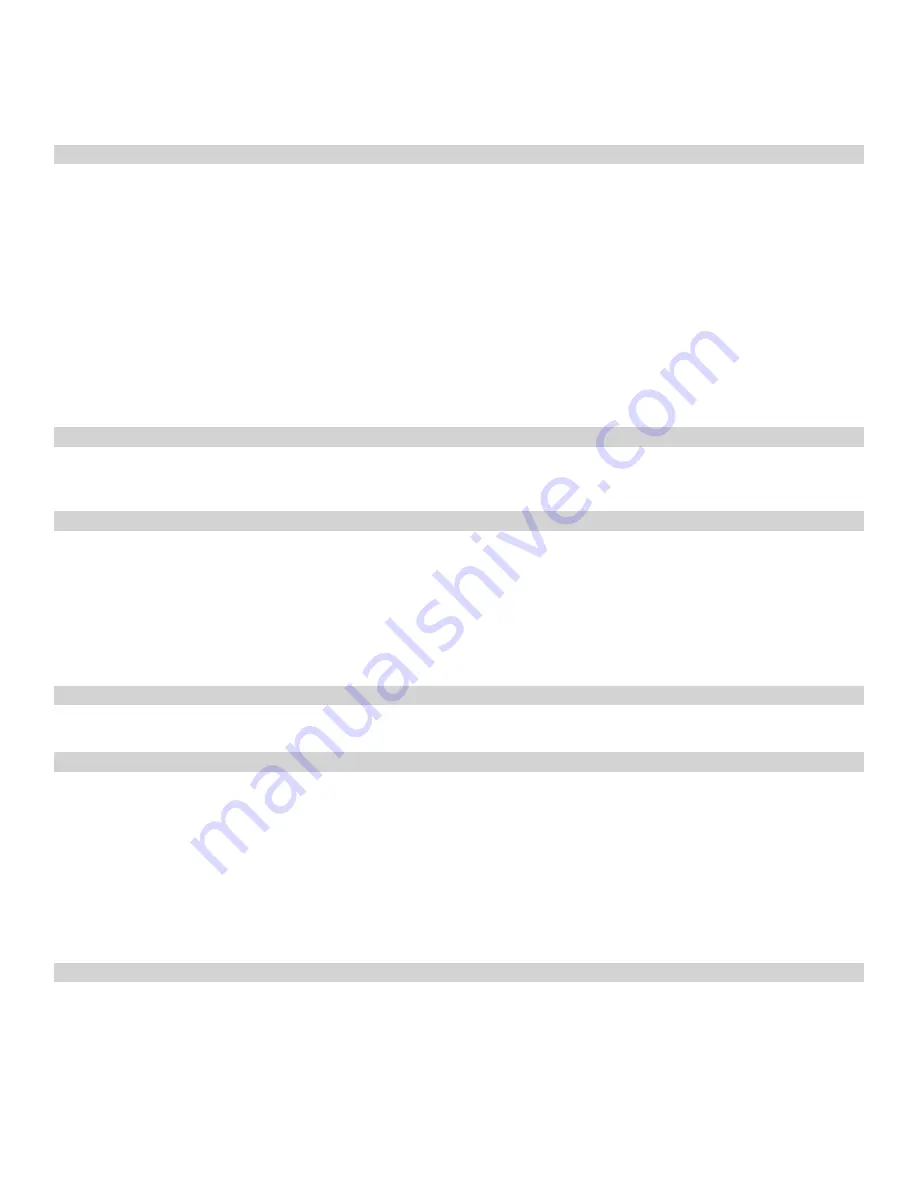
ALF-13120-E-02
All-Flo
10
TROUBLESHOOTING
PROBLEM EFFECT/SOLUTION
Pump Will Not Cycle
Discharge line closed or plugged
Discharge filter blocked
Check valve stuck
Air filter blocked
Air supply valve closed
Air supply hooked up to muffler side of pump
Compressor not producing air or turned off
Muffler iced or blinded
Diaphragm ruptured
Plant air supply line ruptured
Air valve wear/debris
Pilot sleeve wear/debris
Diaphragm rod broken
Diaphragm plate loose
Pumped Fluid Coming Out of Muffler
Diaphragm ruptured
Diaphragm plate loose
Inlet liquid pressure excessive (above 10 psig)
Pump Cycles but no Flow
Inlet strainer clogged
Suction valve closed
Suction line plugged
No liquid in the suction tank
Suction lift excessive
Debris stuck in valves
Excessive wear of check valves
Air leak on suction side with suction lift
Pump Cycles with Closed Discharge Valve
Debris stuck in check valve
Excessive wear of check valves
Pump Running Slowly/Not Steady
Air compressor undersized
Leak in air supply
Air-line, filter regulator or needle valve undersized
Muffler partially iced or blinded
Air valve gasket leak or misalignment
Air valve wear/debris
Pilot sleeve wear/debris
Liquid fluid filter blocked
Pump may be cavitating, reduce speed of operation
Suction strainer clogged
Pump Will Not Prime
Air leak in suction pipe
Air leak in pump manifold connections
Suction strainer and lines clogged
Excessive lift conditions
Check valve wear
Debris in check valve