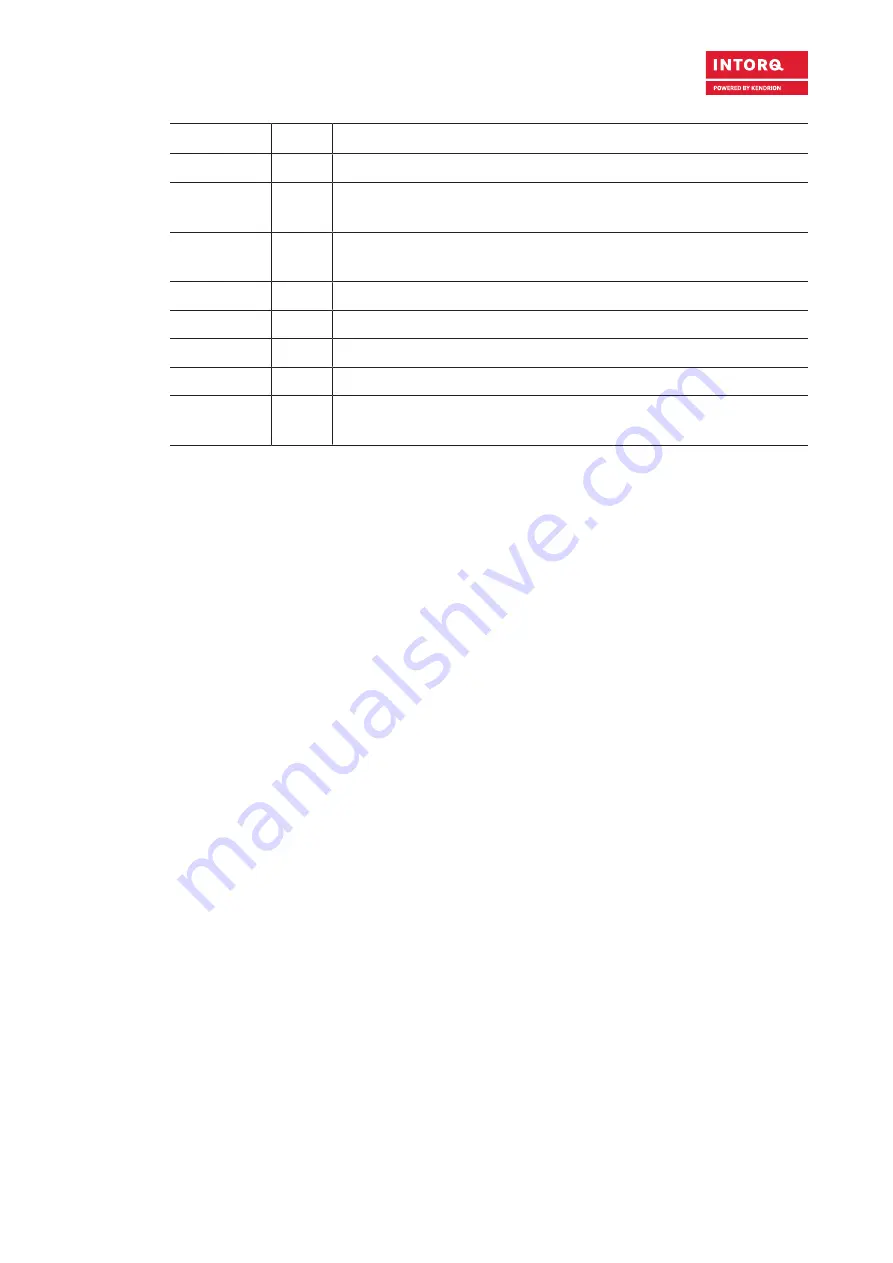
General information
Kendrion INTORQ | BA 14.0223 | 04/2022
10
Letter symbol Unit
Designation
t
3
ms
Slipping time, operation time of the brake (according to t
11
) until standstill
t
11
ms
Delay during engagement (time from switching off the supply voltage to the
beginning of the torque rise)
t
12
ms
Rise time of the braking torque, time from the start of torque rise until reach-
ing the braking torque
t
ue
s
Over-excitation period
U
V
Voltage
U
H
V DC
Holding voltage, after voltage change-over
U
L
V DC
Release voltage, before voltage change-over
U
N
V DC
Rated coil voltage; in the case of brakes requiring a voltage change-over,
U
N
equals U
L