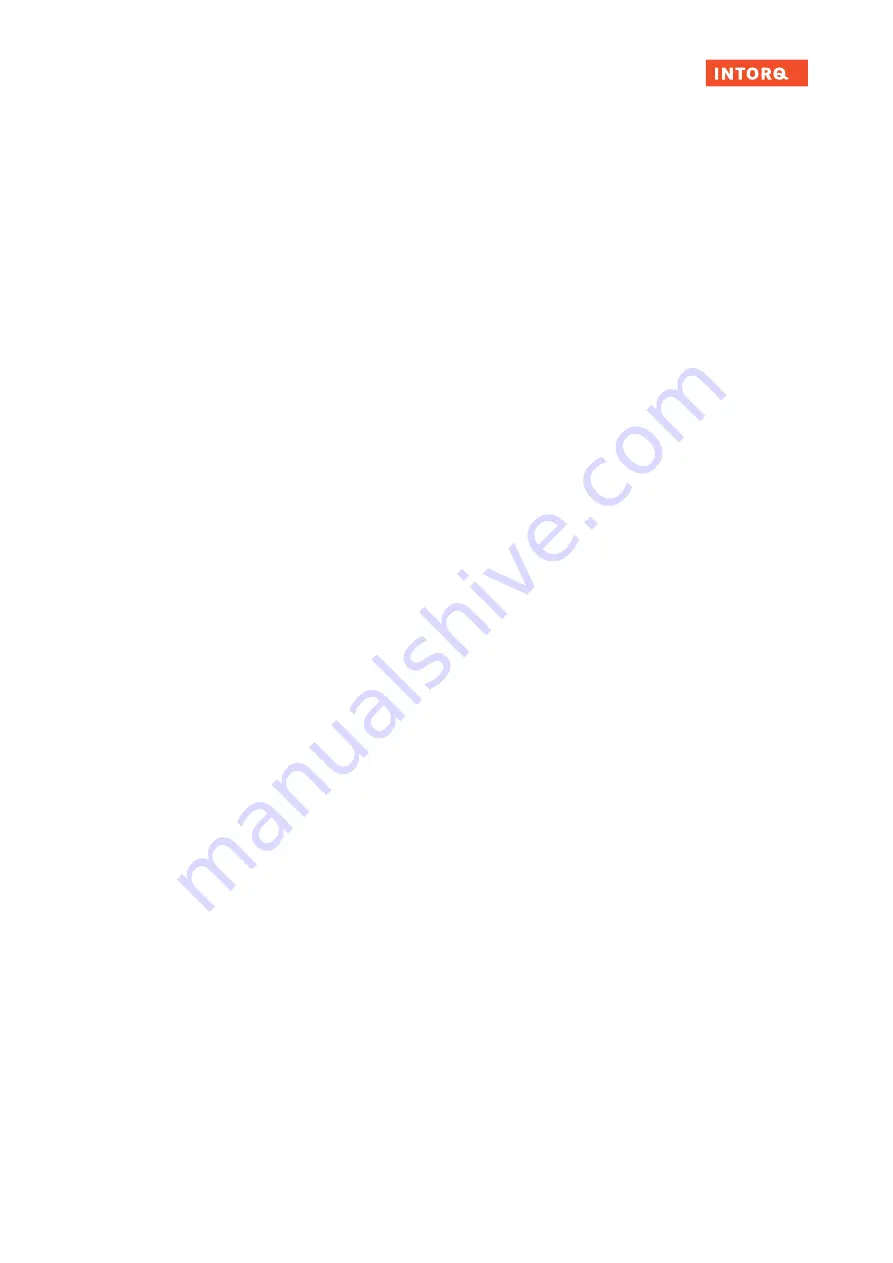
Product description
INTORQ | BA 14.0215 | 07/2019
13
3.4
Braking and release
During the braking procedure, the inner and outer springs use the armature plate to press the rotor (which
can be shifted axially on the hub) against the friction surface. The asbestos-free friction linings ensure high
braking torque and low wear. The braking torque is transmitted between the hub and the rotor via gear
teeth.
When the brakes are applied, an air gap (s
L
) is present between the stator and the armature plate. To re-
lease the brake, the coil of the stator is energised with the DC voltage provided. The resulting magnetic
flux works against the spring force to draw the armature plate to the stator. This releases the rotor from the
spring force and allows it to rotate freely.
3.5
Release monitoring
The spring-applied brake has a micro-switch for each braking circuit to monitor the switching state. When
the brake is released, the micro-switches toggle. This means that it is possible to prevent the drive from
being operated when the brake is closed. The micro-switches can be connected as both normally open
and also normally closed.
To check that the micro-switches function correctly, we recommend testing the switching status (refer to
table 6) in both the released and applied braking states.
3.6
Project planning notes
¾
When designing a brake for specific applications, torque tolerances, the limiting speeds of the rotors,
the thermal resistance of the brake, and the effect of environmental influences must all be taken into
account.
¾
The brakes are dimensioned in such a way that the specified rated torques are reached safely after a
short run-in process.
¾
However, as the organic friction linings used do not all have identical properties and because environ-
mental conditions can vary, deviations from the specified braking torques are possible. These must be
taken into account in the form of appropriate dimensioning tolerances. Increased breakaway torque is
common in particular after long downtimes in humid environments where temperatures vary.
¾
If the brake is used as a pure holding brake without dynamic load, the friction lining must be reactiv-
ated regularly.
3.7
Optional configuration
3.7.1
Hand-release (optional)
To temporarily release the brake when there is no electricity available, a hand-release function is available
as an option. The hand-release function can be retrofitted.
3.7.2
Optional encapsulated design
This design not only prevents the penetration of spray water and dust, but also the spreading of abrasion
particles outside the brake. This is achieved by the following enclosures:
¾
A cover ring over the armature plate and rotor.