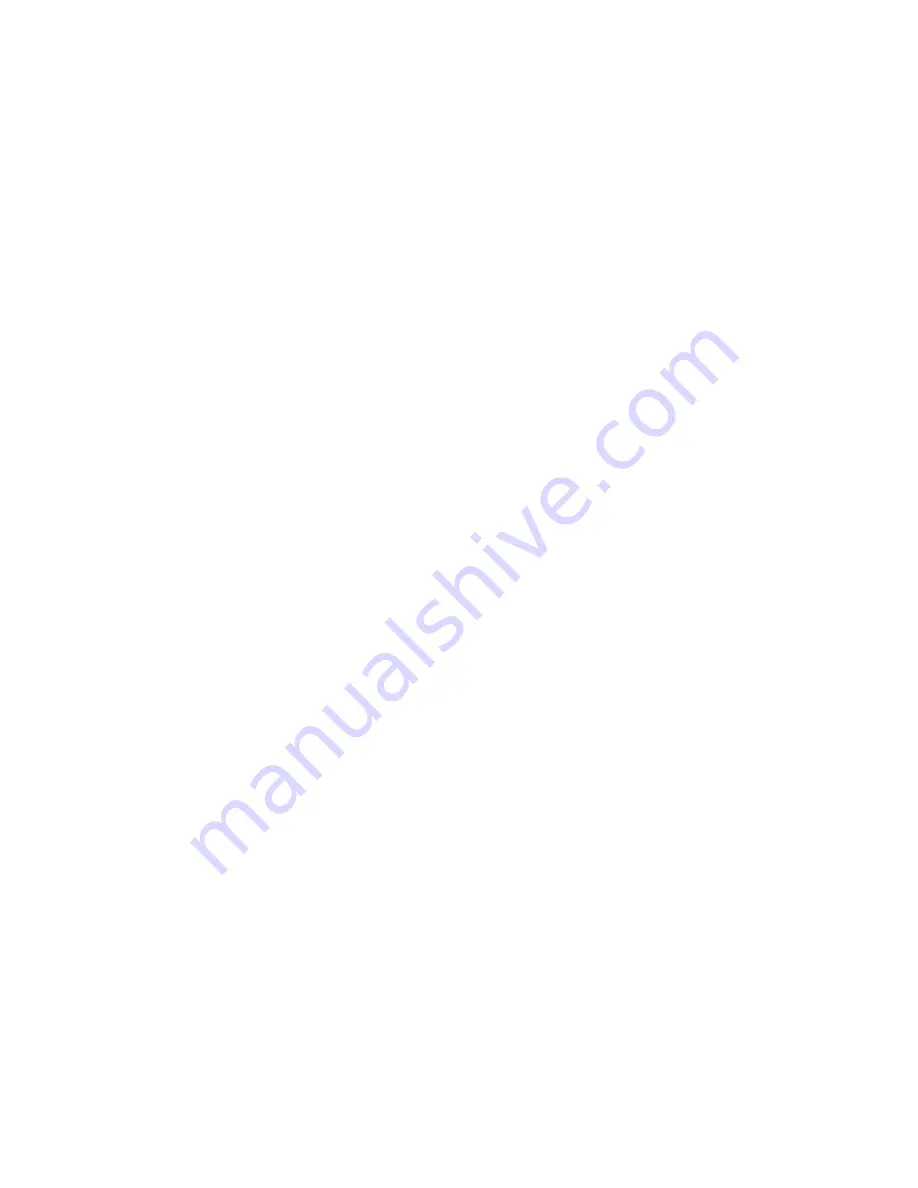
Version 3.0 (04/2013) en
Translation of the original instructions
Manufacturer's address
Interroll Engineering GmbH
Hoeferhof 16
D-42929 Wermelskirchen
Tel. +49 2193 23 0
Fax. +49 2190 2022
www.interroll.com
Copyright
The copyright of this manual remains with Interroll Engineering GmbH. The
operating instructions contain technical regulations and drawings which may not
be reproduced partially or in full, transmitted by any means, utilized without
permission for competitive purposes or disclosed to third parties.