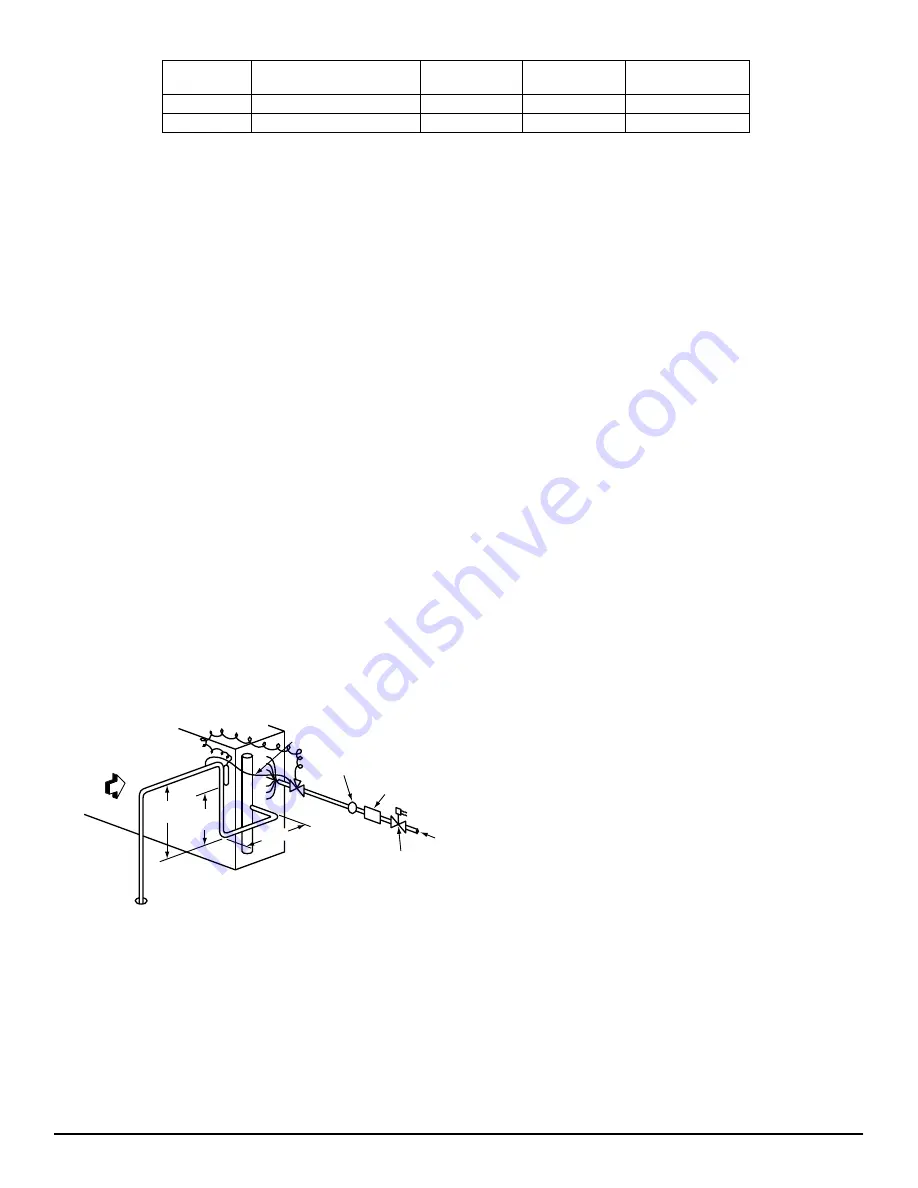
501 01 3600 01
9
Specifications are subject to change without notice.
Table 6 – Refrigerant Specialties Part Numbers
LIQUID LINE
SIZE (in.)
LIQUID LINE
SOLENOID VALVE (LLSV)
LLSV
COIL
SIGHT
GLASS
FILTER
DRIER
1
/
2
EF680035
EF680037
KM680004
KH43LS085
5
/
8
EF680036
EF680037
KM680005
KH43LS087
Check CAS090*G/H Model with Evaporator Coil
Connections —
Confirm before installation of unit that the evaporator coil
connections are consistent with the CAS090*G/H.
Insulate Suction Lines —
Apply closed-cell tubular insulation to all suction lines
between evaporator coil connection and CAS090*G/H
unit’s suction service valve.
Refer to Table 6 for recommendations on refrigeration
specialties.
Select the filter drier for maximum unit capacity and
minimum pressure drop. Complete the refrigerant piping
from the indoor unit to the outdoor unit before opening
the liquid and suction lines at the outdoor unit.
Install Liquid Line Solenoid Valve —
It is recommended that a solenoid valve be placed in the
main liquid line (see Fig. 6) between the condensing unit
and the evaporator coil. Locate the solenoid valve at the
outlet end of the liquid line, near the evaporator coil
connections, with flow direction arrow pointed at the
evaporator coil. Refer to Table 6. (A liquid line solenoid
valve is required when the liquid line length exceeds 75 ft
[23 m].) This valve prevents refrigerant migration (which
causes oil dilution) to the compressor during the off cycle, at
low outdoor ambient temperatures. Wire the solenoid in
parallel with the compressor contactor coil (see Fig. 6). This
means of electrical control is referred to as solenoid
drop
control.
Single Circuit Coil Piping Configuration
For single compressor condensing units
15 DIAMS
MIN
10
DIAMS
8 DIAMS
MIN
INDOOR
COIL CKT
AIRFLOW
TXV
SENSING
BULB
EQUALIZER LINE
SIGHT GLASS
A LOCATION
TXV
FILTER DRIER
A LOCATION
LIQUID LINE
SOLENOID
VALVE
FLOW
C14291
Fig. 6 -- Location of Sight Glass and Filter Drier
Solenoid drop control wiring:
Control the power to the
liquid line solenoid through a Solenoid Valve Relay (SVR)
in all units. Use part number HN61PC005 (field--supplied,
installed). CAS090*G/H unit requires one SVR.
Evaporator Capacity Control Liquid Line Solenoid
Valve:
Many older unit designs included automatic
capacity controls that sensed changes in suction pressure
and could increase or decrease compressor capacity
automatically as the evaporator load changed. Control
systems were used on these units that had the thermostat’s
second stage contacts control a capacity control liquid line
solenoid valve to open or shutoff a portion of the
evaporator surface without any direct connection to the
compressor circuit.
This form of system capacity staging control is not possible
with CAS090 models. If this installation is a retrofit for a
unit that included automatic pressure--operated unloading,
check the existing thermostat and liquid solenoid valve.
When found, convert the evaporator second stage solenoid
control into a drop--solenoid control.
Selecting an Accumulator –
Because all CAS090 models use scroll compressors, an
accumulator is not required. If an accumulator is to be
added, check the accumulator manufacturer’s literature
carefully for indication of its suitability for use with
R--410A; look for minimum working pressure of 200 psig
(1380 kPa). Select the accumulator first on the basis of its
cataloged minimum capacity (tons) to ensure oil return from
the accumulator, then on tube size or holding capacity.
Make Piping Connections —
Piping connections at the CAS090*G/H unit are ball
valves with stub tube extensions. Do not open the unit
service valves until all interconnecting tube brazing has
been completed.
The stub tube connections include
1
/
4
-in SAE service fittings
with Schrader valve cores (see Fig. 7). Before making any
brazed connections to the unit service valves, remove both
Schrader valve caps and cores and save for re-installation.
Connect a source for nitrogen to one of these service fittings
during tube brazing to prevent the formation of copper
oxides inside the tubes at brazed joints.
When connecting the field tubing to the CAS090*G/H
service valves, wrap the valves in wet rags to prevent
overheating.
Pressure-test all joints from outdoor unit connections over
to the evaporator coil, using nitrogen as pressure and with
soap-and-bubbles.
When pressure-testing is completed, remove the nitrogen
source at the outdoor unit service valves and re-install the
two Schrader valve cores. Torque the cores to 2-3 in-lbs
(23-34 N-cm).