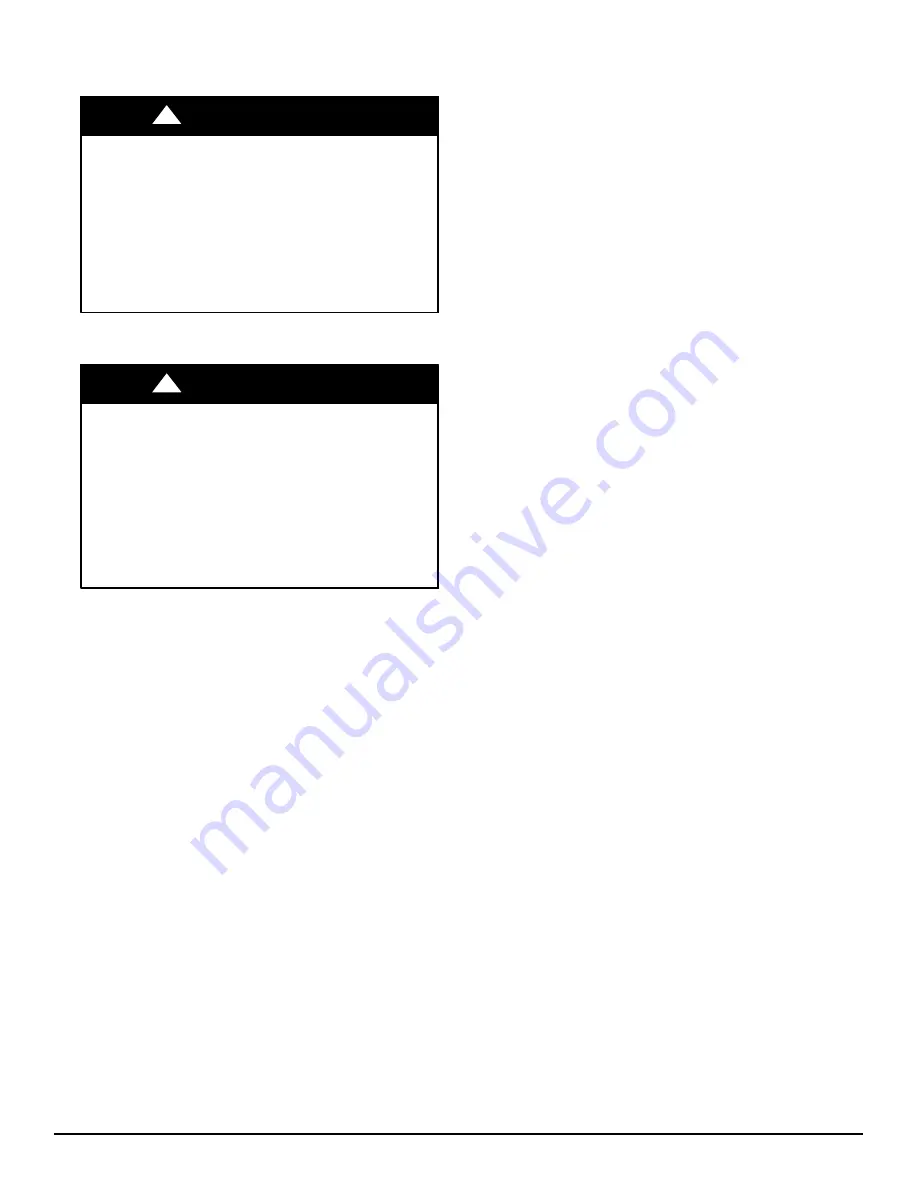
501 01 3600 01
21
Specifications are subject to change without notice.
SERVICE
Refrigeration System
EQUIPMENT DAMAGE HAZARD
Failure to follow this caution may result in damage to
equipment.
This system uses R--410A refrigerant which has higher
pressures than R-22 and other refrigerants. No other
refrigerant may be used in this system. Gage set,
hoses, and recovery system must be designed to
handle R--410A. If you are unsure consult the
equipment manufacturer.
CAUTION
!
Compressor Oil —
EQUIPMENT DAMAGE HAZARD
Failure to follow this caution may result in damage to
equipment.
The compressor in a R--410A system uses a polyolester
(POE) oil. This oil is extremely hygroscopic, meaning it
absorbs water readily. POE oils can absorb 15 times as
much water as other oils designed for HCFC and CFC
refrigerants. Take all necessary precautions to avoid
exposure of the oil to the atmosphere.
CAUTION
!
Servicing Systems on Roofs With Synthetic Materials —
POE (polyolester) compressor lubricants are known to cause
long term damage to some synthetic roofing materials.
Exposure, even if immediately cleaned up, may cause
embrittlement (leading to cracking) to occur in one year or
more. When performing any service which may risk
exposure of compressor oil to the roof, take appropriate
precautions to protect roofing. Procedures which risk oil
leakage include but are not limited to compressor
replacement,
repairing
refrigerants
leaks,
replacing
refrigerant components such as filter drier, pressure switch,
metering device, coil, accumulator, or reversing valve.
Synthetic Roof Precautionary Procedure:
1. Cover extended roof working area with an imper-
meable polyethylene (plastic) drop cloth or tarp.
Cover an approximate 10 x 10 ft (3.3 x 3.3 m) area.
2. Cover area in front of the unit service panel with a
terry cloth shop towel to absorb lubricant spills and
prevent run-offs, and protect drop cloth from tears
caused by tools or components.
3. Place terry cloth shop towel inside unit immediately un-
der component(s) to be serviced and prevent lubricant
run-offs through the louvered openings in the base pan.
4. Perform required service.
5. Remove and dispose of any oil contaminated material
per local codes.
Liquid Line Filter Drier —
The factory-provided filter drier is specifically designed to
operate with R--410A Replace the filter drier with
factory-authorized components only with a filter drier
with desiccant made from 100% molecular sieve grade
XH-11. Filter drier must be replaced whenever the
refrigerant system is opened.
When removing a filter drier, use a tubing cutter to cut the
drier from the system.
Do not unsweat a filter drier
from
the system. Heat from unsweating will release moisture
and contaminants from drier into system.
Field Refrigerant Access Ports —
Field service access to refrigerant pressures is through the
access ports located at the service valves (see Fig. 23).
These ports are
-in SAE Flare couplings with Schrader
check valves and service caps. Use these ports to admit
nitrogen to the field tubing during brazing, to evacuate the
tubing and evaporator coil, to admit initial refrigerant
charge into the low-side of the system and when checking
and adjusting the system refrigerant charge. When service
activities are completed, ensure the service caps are in
place and secure; check for leaks. If the Schrader check
valve must be removed and re-installed, tighten to 2-3
in-lbs (23-34 N-cm).
Factory High-Flow Access Ports —
There are two additional access ports in the system - on
the suction tube between the compressor and the suction
service valve and on the liquid tube near the liquid service
valve (see Fig. 24). These are brass fittings with black
plastic caps. The hose connection fittings are standard
-in SAE Male Flare couplings.
The brass fittings are two-piece High Flow valves, with a
receptacle base brazed to the tubing and an integral
spring-closed check valve core screwed into the base. (See
Fig. 20) This check valve is permanently assembled into
this core body and cannot be serviced separately; replace
the entire core body if necessary. Service tools are
available from RCD that allow the replacement of the
check valve core without having to recover the entire
system refrigerant charge. Apply compressor refrigerant
oil to the check valve core’s bottom o-ring. Install the
fitting body with 96
-10 in-lbs (1085
23 N-cm) of
torque; do not overtighten.