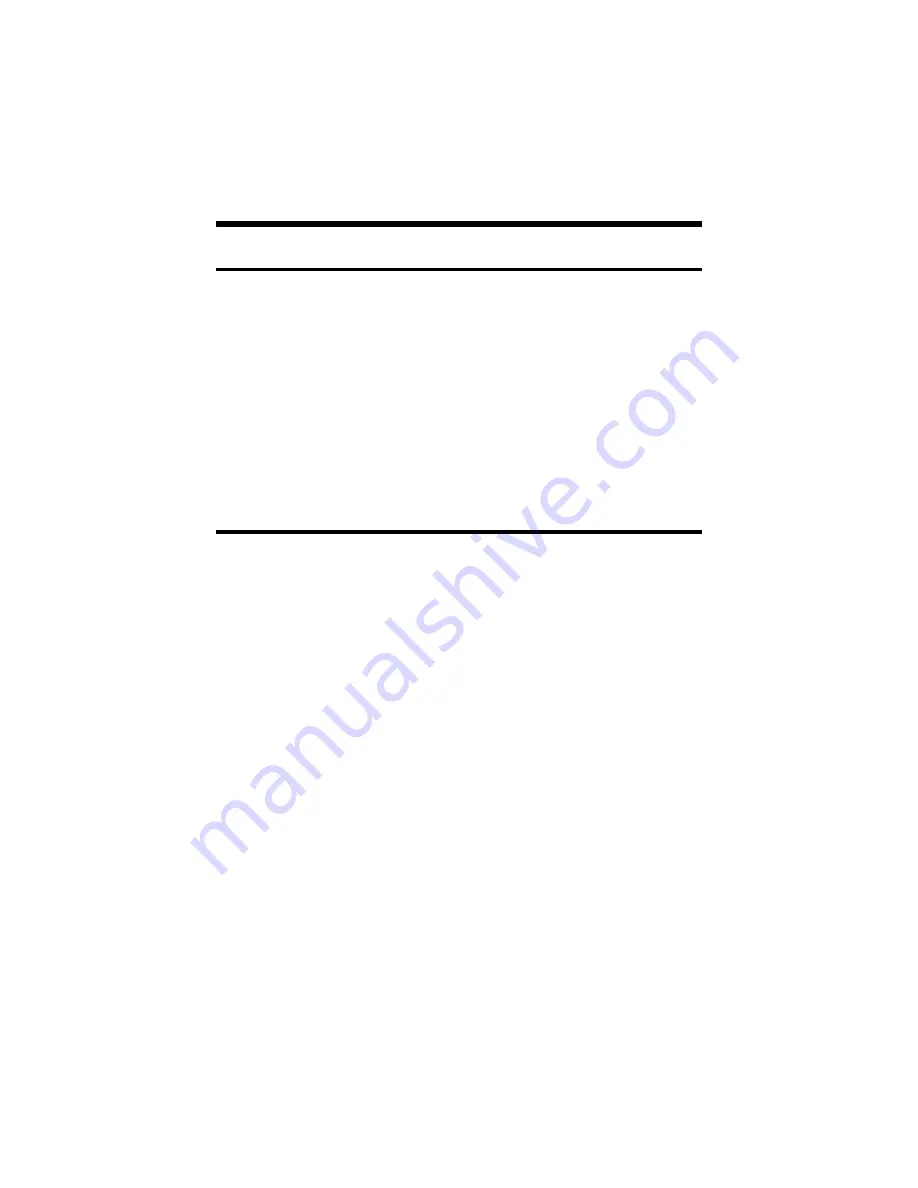
25
S e c t i o n 1 . 5
I n t e r f a c i n g t o t h e I B S e r i e s D r i v e
S e c t i o n O v e r v i e w
The IB series drive may be incorporated directly in the user’s printed circuit
board. It may also be chassis mounted and interfaced to using either
soldered wire connection or the optional plug on terminal strips (IMS PN
TS-6). In order to operate, the IB drive must have the following connec-
tions
!
Motor Power (+V).
!
Motor.
!
Logic Interface (Step Clock, Direction).
The section also contains pin assignment and description, and sample logic
and current adjust interface circuit examples.
L a y o u t a n d I n t e r f a c e G u i d e l i n e s
Logic level signals should not run parallel to motor phase signals. The
motor phase signals will couple noise onto the logic level signals. This will
cause rough motor motion and unreliable system operation. Motor phase
signals should be run as pairs and should be separated from other signals
by ground traces where possible
When leaving the board, motor cables should not run parallel with other
wires. Phases should be wired using twisted pairs. If motor cabling in
excess of one foot is required, motor cabling should be shielded twisted
pairs to reduce the transmission of EMI. The shield must be tied to AC
ground at driver end only. The motor end must be left floating.
If more than one driver is connected to the power supply, separate power
and ground connections from each driver to the power supply should be
used.
The power supply cables need to be a twisted pair if power is connected
from a source external to the board. If multiple drivers are used with an
external power source, and it is not possible to run separate power and
ground connections to each driver, a low impedance electrolytic capacitor
equivalent to two times the total capacitance of all driver capacitors and of
equal voltage must be placed at the power input of the board.