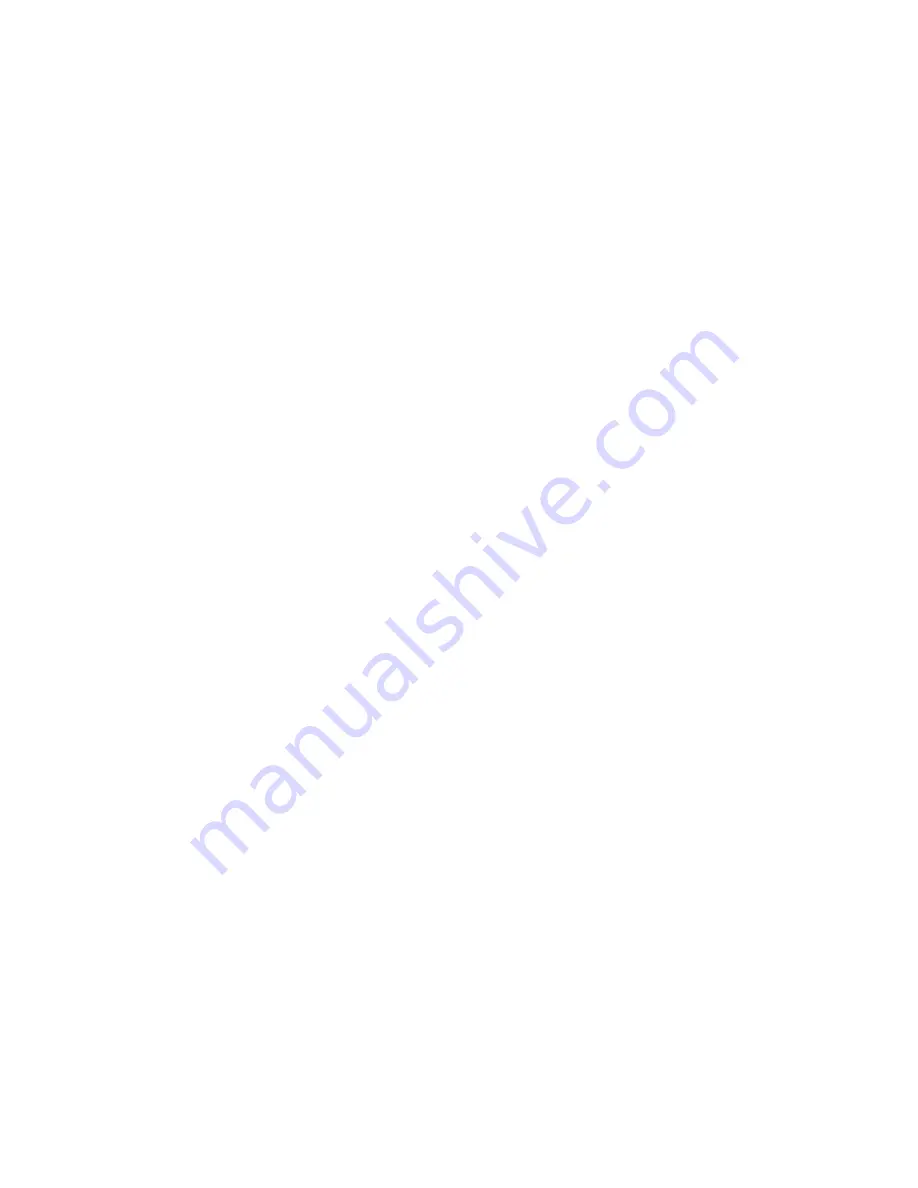
- 6 -
2
INSTALLATION
2.1
SENSOR
!! CAUTION:
All sensors have a directional arrow on the tag and/or
etched into a metal part. All flow controllers are assembled with the valve
on the downstream side. Before installing a sensor, please note proper
flow direction. This is critical to instrument performance.
The sensor style supplied with your meter is listed in the model code number in SECTION 6. Proper
installation of the sensor is necessary for achieving accuracy and repeatability. Installation
suggestions for each type of standard sensor are given here and instrument detail drawings may be
included in the appendix. For custom sensor installations, refer to CUSTOM INFORMATION —
SECTION 6.
Be sure wetted surfaces are clean before installing. If cleaning is needed, use non-residue solvent
and wipe dry. Some sensor terminations are enclosed in an aluminum housing and if it is not sealed
properly can easily be damaged by moisture and corrosion. Make sure the lid is tightly sealed and
the gasket, if supplied, is in place.
TU or TUL (nonintrusive) — capillary (C),
1
/
16
, and
1
/
8
TU or TUL sensors particularly require
special care in handling and installing to avoid damage to sensor tube and tube stubs.
!! WARNING:
TU and TUL sensors are made with thin-walled tubing — use care
when installing.
All TU and TUL sensors should have a straight line input sections, typically 20 pipe diameters. If
installed vertically, the direction of flow should be up through the sensor. Connection in the line is
via compression fittings, hose with clamp, threaded fittings or flanges, whichever is appropriate.
Care must be taken not to transmit a twisting force through the sensor’s midsection. The TU and
TUL sensors, whether flanged or not, must not be used to pull other piping together or to make up
angular mismatch of fittings. The sensor mounted enclosure should never be rotated for any reason.
TU and TUL sensors 1/16 or smaller may be sleeved with a tube for added support. Connection
should always be made to the flow tube, as there is no assured seal between the flow tube and the
sleeve.
Fluid temperatures other than ambient require special attention. Thermal gradients from one end of
the sensor to the other, as well as along the radius of the connection pipe, are undesirable.
Therefore, effective insulation should be installed around the inlet and outlet straight line runs.
Gradients which may exist in the line further up stream can be removed if an insulated elbow is
installed in the line prior to entering the straight line portion of the plumbing. Metallic support
braces for the sensor or adjoining plumbing can act as a heat sink and cause indication errors in high
temperature applications. The support braces should be thermally isolated from the line to avoid
heat loss effects. The adjustable valve is attached to the downstream side of the sensor. It generates
heat when used and should not be insulated.
Flow stream conditioning must also be considered to maximize meter performance. Avoid upstream
protrusions and short distance straight runs. Flow pulsations, such as those created by metering
pumps, may cause the instrument to differ from the factory calibration. Furthermore, if the flow is
varied by stroke and by pump speed adjustment, the indication will most likely be non-repeatable. If