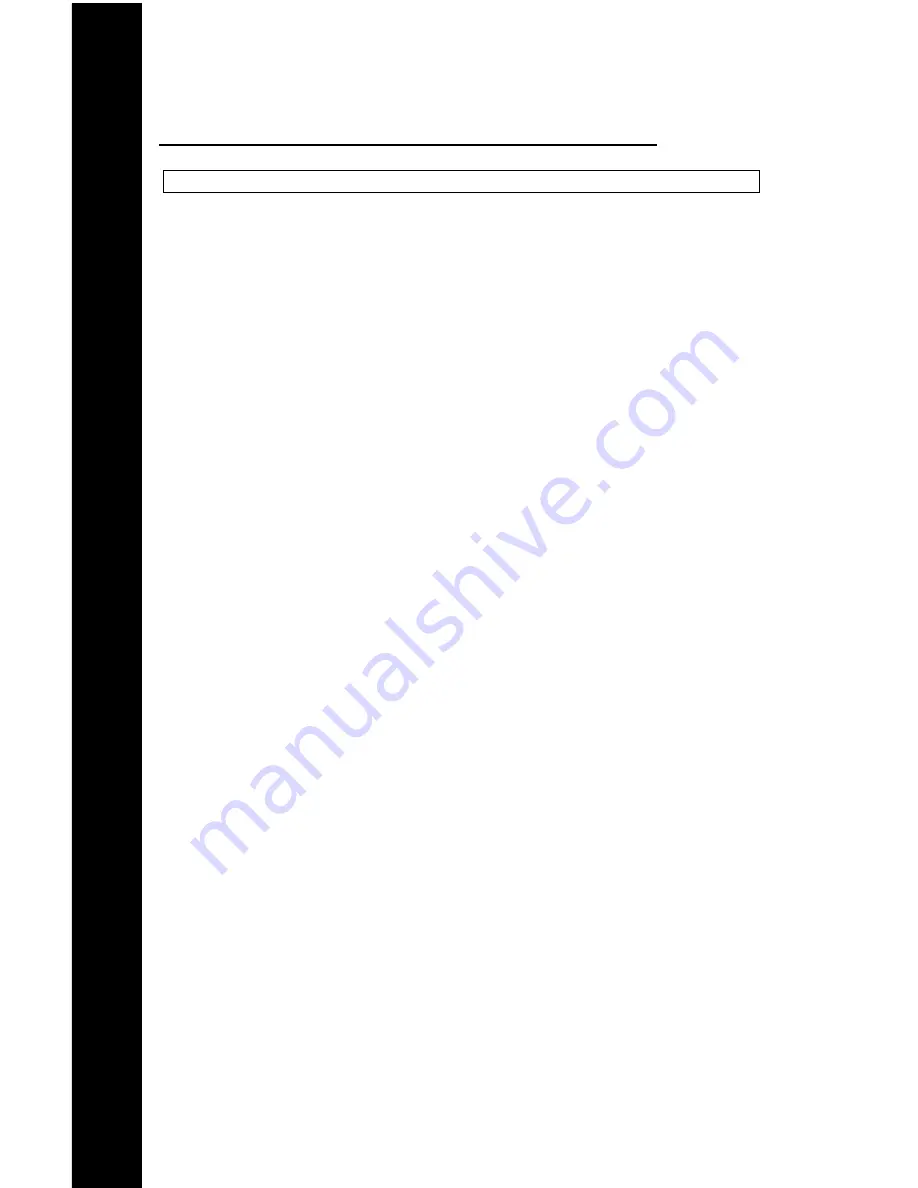
Machine makes a
Gearbox drive not
Loosen gearbox
ratcheting noise when
engaged with airlock
and gearbox
turned on.
rotor connection.
stabilizers. Align
gearbox and airlock
perpendicular to
each other.
Low oil level in gearbox.
Have the gearbox
inspected and
repaired by a
qualified technician
if necessary.
Decreased material
Worn airlock seals.
Inspect seals for
throw.
tears or cuts. See
maintenance section
to replace or adjust
as necessary.
Kink in hose.
Run hose as straight
as possible to help
maintain production.
Excess air leaking into
Inspect seals for tears
hopper.
or cuts. See mainten-
ance section to
replace or adjust as
necessary.
Machine does not run
No power.
Check source of
electrical power.
Possible tripped
circuit breaker.
Main panel circuit
Push to reset.
breaker tripped.
TROUBLESHOOTING
30
TROUBLESHOOTING
THE FORCE/1
Troubleshooting, Cont.
Problem
Likely Cause
Remedy
Summary of Contents for Force 1
Page 3: ...MACHINE INFORMATION 2...
Page 9: ...8 THE FORCE 1 Overview OVERVIEW...
Page 42: ...ELECTRICAL DRAWINGS 41 Electrical Wiring Diagram Electrical With Relay Mfg from 10 02 Present...
Page 45: ......
Page 48: ......