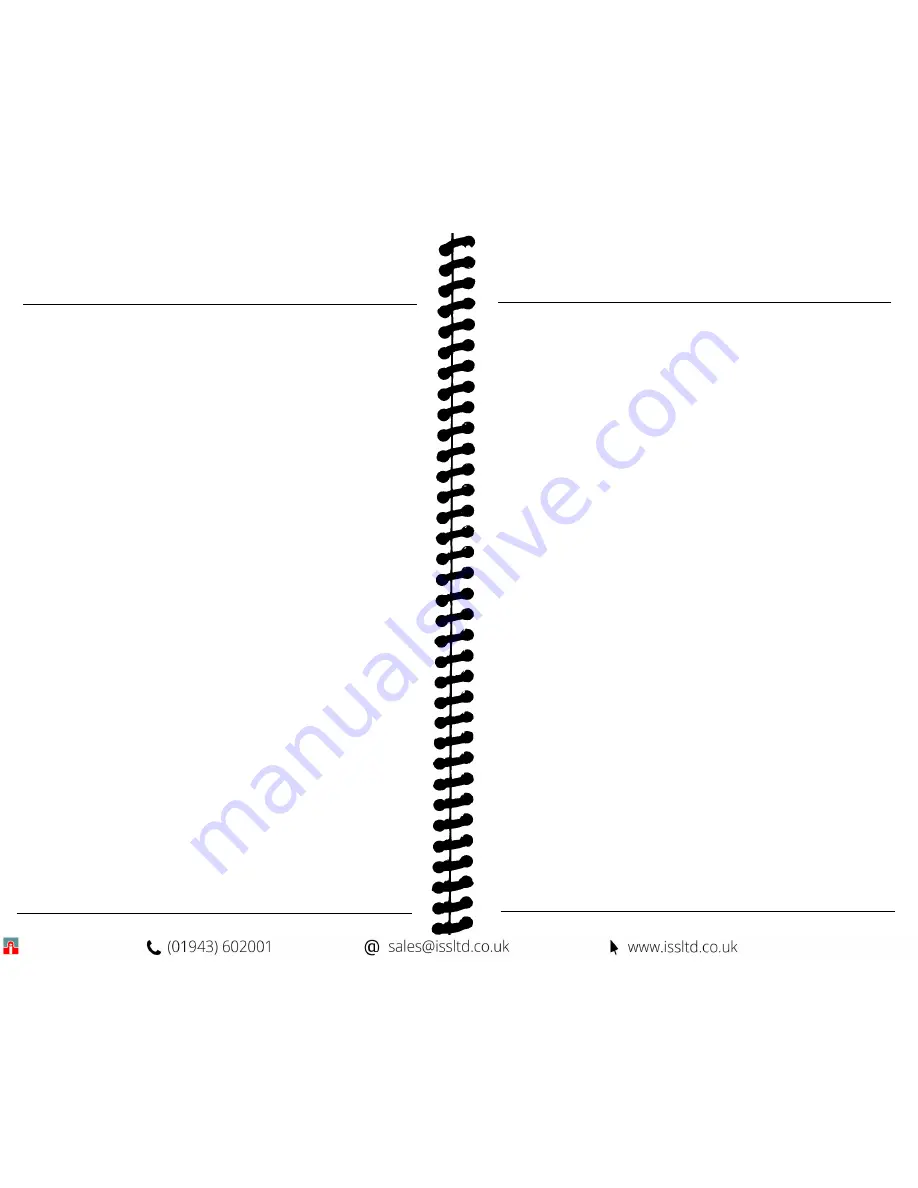
V.
PROGRAMMING
l
MASTER MODE
Program the following variables when using the MicroSpeed 196 in any mode. (These
are the only required variables if the MicroSpeed 196 will be used exclusively in
Master
mode.) After programming the variables, go to Section IX
“Tuning the
Microspeed 196
.“Then, after all programming and tuning is complete, go to
“Appendix A,” and record your entries.
Variable 01 - Maximum RPM
-
This number represents the revolutions per
minute of the shaft on which the feedback sensor is mounted, when the
MicroSpeed 196 is running the motor at maximum operating speed.
Note: The drive system must be able to run 10% faster than the
value programmed
into Variable
01
(maximum rpm.)
Variable 02 - User Units at Maximum RPM
-
This number will set up the
MicroSpeed 196 to translate rpms to units of production that are more appropriate
to the user, such as “Feet per Minute,” or “Gallons per Hour,” etc. The Speed Set
Points and the linear tach display will then be relative to the operation. To use this
variable, first determine the value of the user units at maximum rpm. If the rpm
of
the monitored shaft is desired, enter the same value as Variable 01. Otherwise, you
must calculate the user unit at the speed entered into Variable 01. Or you can enter
the same value as Variable 01, run at that speed, measure the actual units, and then
enter the measured value. Use Variable 10 to program the alphanumeric display to
show the appropriate user unit, i.e., PPM, GPM, GPH, etc. (see Section VIII,
“Programming Operational Variables"
in this manual for details and
the list of display options.
Variable 03 - Feedback Pulses Per Revolution
-
This is the number of digital
pulses produced by the feedback sensor on the monitored shaft for each shaft
revolution.
Note: Variable 03 will not accept decimals, the entry must be a whole number.
Example 1
-
The feedback sensor in this case is a Ring Kit at 60 ppr, mounted on the
motor shaft. The rated motor speed is 1750 rpm, but the operation only requires
1500 rpm. The desired display is rpm. Then Variable 01 would be 1500, Variable 02
would be 1500, and Variable 03 would be 60.
Example 2
-
In this case, the feedback sensor is a 600 ppr encoder, mounted on a
intermediate downstream shaft. The speed of this shaft is not known, but we do know
we want a maximum line speed of 200 feet per minute. Enter the PPR value (600 PPR)
into variable 03. Then go into diagnostic 9 (explained in section IX:
“Calibrating the
Isolated Command Output through the Drive"
and slowly ramp up the system speed
until 200 ft./min. is obtained. The display will read out the rpm value needed for
Variable 01. In this example, 623 rpm. Now leave Diagnostic 9, and enter 623 into
Variable 01, and 200 into Variable 02. Adjust the Output Span Potentiometer as
shown in Section IX for proper operation.
11
VI.
PROGRAMMING
l
FOLLOWER MODE
The Microspeed 196 in the Follower mode mirrors a lead frequency input, and can be
scaled by the Ratio Set Point. The lead frequency is typically generated from a digital
transducer on another shaft. The initial relationship between the lead and follower is set
up in Variables 01 through 05. This relationship will be referred to as the Unity Ratio.
First, program the Microspeed 196 Variables 01-03 per the Master mode instructions.
Then, program the Lead Input to set up the Unity Ratio. The MicroSpeed 196 maintains
both velocity and rotational control so that the cumulative following error is zero. A set
point ramp, cessation of the lead frequency, or a
STOP
command, will set the follower
error count to zero.The
ACCEL
and
DECEL
variables are active only when the Ratio
Set Point is changed by a value greater than 10% of the Unity Ratio, or by a
STOP
command.
Note: Follower control operates best when the lead and follower frequencies are relatively
equal. Example: When a lead frequency is 200 Hz, and the
follower frequency is 2000 Hz,
one lead pulse controls 10 follower pulses. This situation can result in unstable follower
operation.
Variable 04 - Maximum Lead RPM
-
This is the maximum rpm of the lead motor,
or of the shaft being monitored by the transducer that is producing the lead frequency
signal. The relationship of the Maximum Lead RPM (Var 04) at the User Unity Ratio
(Var 23) set point will result in the motor speed running at Maximum RPM (Var 01).
Variable 05 - Lead Pulses per Revolution
-
This is the number of pulses per
revolution generated by the transducer that is producing the lead frequency.
Note: When generating the lead
signal
from
a non-rotational source and only Hz. is known,
enter 60 into Variable 05
(lead PPR).
Then enter thefrequency into Variable 04
(Max. Lead RPM).
Variable 23 - User Unity Ratio
-
This variable allows the Ratio Set Point to be
programmed in User Units in the Follower mode (such as turns/foot). It is also used as
the Unity Ratio value in the ratio tach display mode. When this value is entered into the
Ratio Set Point, the follower motor will run at the relationship programmed into
Variables 01-05.
Note:
Variable 23 (User Unity Ratio) is applied when the operation is based on units
other than time (i.e. threads/inch vs. cuts/minute). If your operation has a time based
relationship, then leave Variable 23 at the default value.
Example:
Assume that the Unity Ratio between the Lead and Follower in a ball screw
thread-cutting operation results in 50.00 threads per inch being cut by the follower
machinery at its fastest rate. The lead motor turns at 1000 RPM with 60 PPR. The
follower motor must turn at 1500 rpm with 60 ppr. The variables would be programmed
as follows: Var 01 & 02 = 1500, Var 03 = 60, Var 04 = 1000, Var 05 = 60, and
Var 23 = 50.00.
Entering a Ratio Set Point of 50.00 will always produce 50 threads per inch. Changing
the Ratio Set Point to 25.00 will halve the follower motor speed in relation to the lead
motor and produce 25 threads per inch.
12
Summary of Contents for MicroSpeed 196
Page 1: ...MSMAN32C MicroSpeed 196...
Page 19: ......