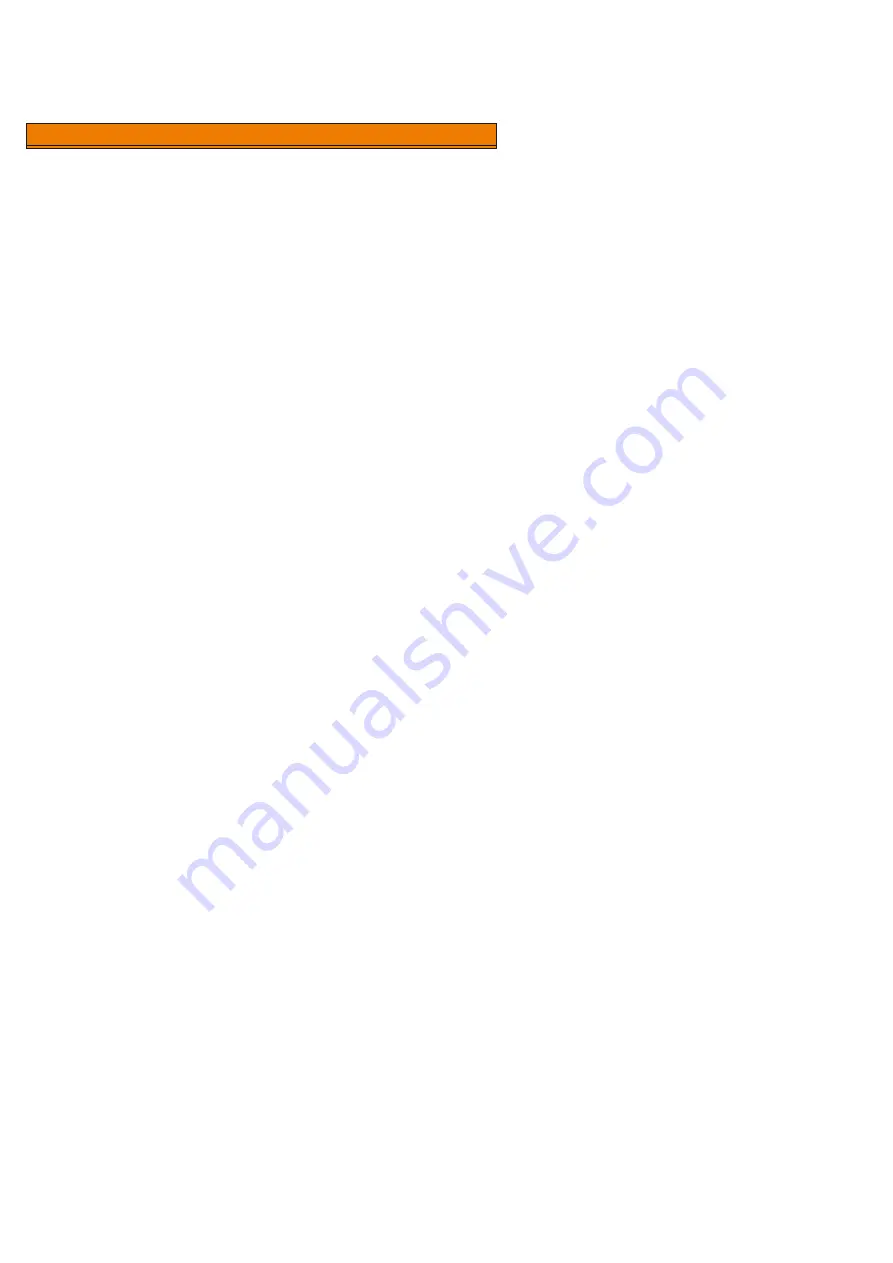
Date: November 2016
Issue No: 2
Crewsaver -
Servicing Manual : Inshore 380N Lifejacket
Page
of 31
25
8.1
Assembly
8
Section
8.1.1
Ensure the whistle is positioned and tied in correctly.
8.1.2
Expel the air from the chamber by inverting the dust cap on the oral tube.
Lifejackets may also be
deflated using the Venturi Vacuum System. For the part number, refer to Section 9.
8.1.3
Assemble the Operating Mechanism to the inflator.
8.1.3.1
For United Moulders Mk5 Automatic Operating Mechanisms. See Fig 8.1
8.1.3.1.1 A new retaining clip must be fitted. Refer to Section 9 for replacement parts.
8.1.3.1.2 Fit the new automatic firing capsule to the operating head, screw hand tight.
8.1.3.1.3 Locate Operating head onto the Manifold.
8.1.3.1.4 Tighten the retaining nut onto the body using the Calibrated torque driver provided in
the Crewsaver servicing tools. Note: Retaining nut must be tightened to between 2.5
and 2.7 Nm.
8.1.3.1.5 Firmly screw the cylinder adaptor by hand into the head
8.1.3.1.6 Connect the cylinder adaptor to the pressure test unit
8.1.3.1.6 Pressurise the head to between 25 and 30 psi and release the control to its vertical
position.
8.1.3.1.7 There may be a slight decrease in pressure over the first 2 seconds as the unit
stabilises. Leave for 10 seconds and check for any further decrease in pressure
shown on the gauge
8.1.3.1.8 Release the pressure by turning the control to deflate.
8.1.3.1.9 If there had been any decrease in pressure remove the cylinder adaptor, remove the
operating head and check the following.
a. Thick and thin washer either side of the head.
b. Damage to the D post seating.
c. Cross thread chrome nut
d. The cylinder seating washer.
e. The schrader or pang valve in the ‘D’ post.
f. The operating head
Warning: Care must be taken not to ‘cross thread’ the connection.
8.1.3.2.10 Fit the gas cylinder to the firing mechanism by hand then check using the torque
wrench and head adaptor from the tool kit (4Nm). The operating head is gripped in
one hand and the cylinder tightened using the torque wrench with the cylinder
tightening tool held in the other hand.
8.1.3.2.11
Place the Netlon sleeve over the cylinder
8.1.4
To re-pack the lifejacket see Fig 8.2.
8.1.5
Expel additional excess air, during the packing operation, from within the inflator by again inverting the
cap on the oral tube and inserting it into the oral valve. When all excess has been expelled replace the
cap.
8.1.6
Mark Service Label on Lifejacket (using an indelible pen) and Service Record Sheet with the date of the
service.
8.1.7
Ensure the serial number has been correctly recorded and that it is clearly marked on the Record
Sheet.
Warning: The lifejacket folding procedures must be followed accurately to ensure that the lifejacket inflation
mechanism operates and the lifejacket deploys correctly. The lifejacket shall not be folded and/or packed using
any other method or procedure than that specified.