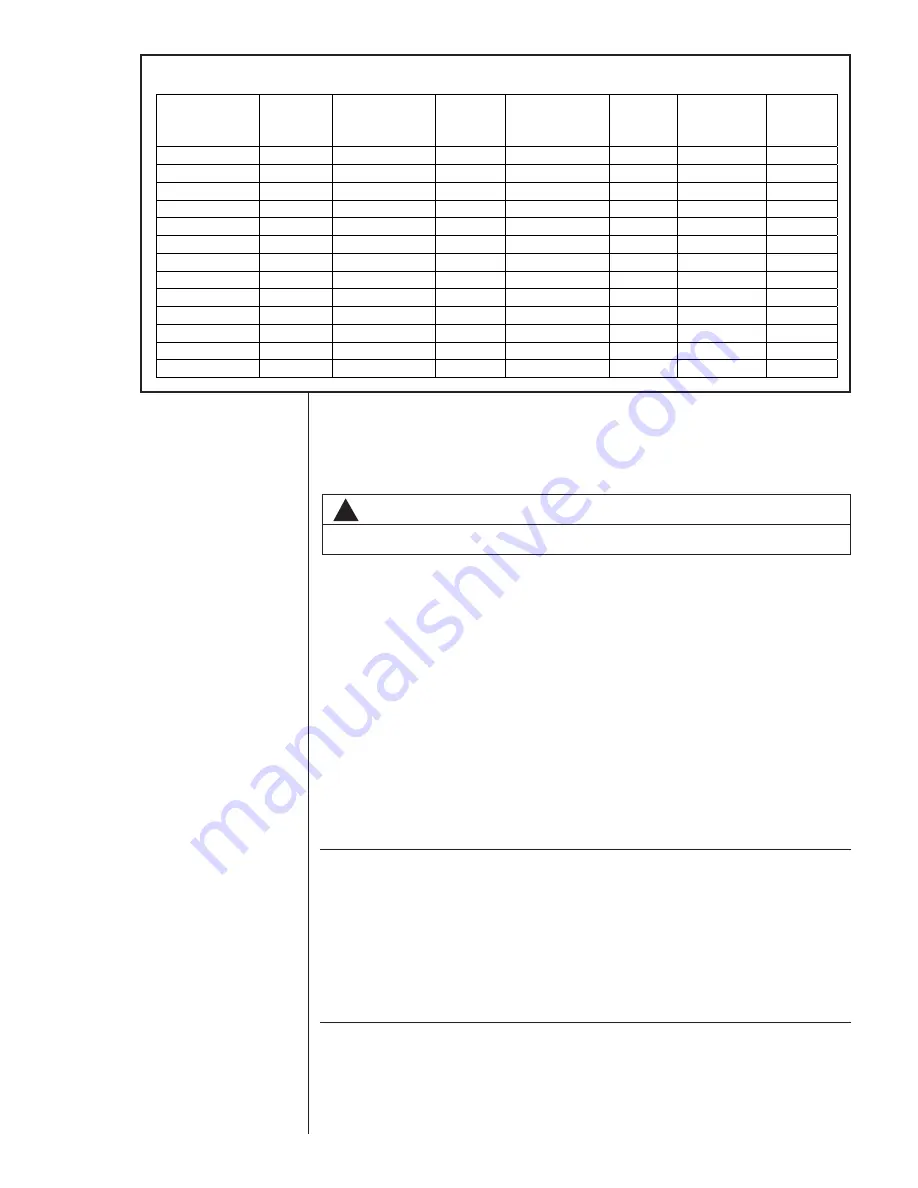
42
Step 5. Adjust Charge to obtain the specified sub-cooling value. If the measured
sub-cool is below the listed requirement for the given outdoor and indoor
conditions, add charge. If the measured sub-cool is above the listed
requirement for the given outdoor and indoor conditions remove charge.
IMPORTANT: Excessive use of elbows in the refrigerant line set can produce
excessive pressure drop. Follow industry best practices for installation. Installation
and commissioning of this equipment is to be preformed by trained and qualified
HVAC professionals. For technical assistance contact your Distributor Service
Coordinator.
16.6 FINISHING UP INSTALLATION
• Disconnect pressure gauges from pressure ports; then replace the pressure port
caps and tighten adequately to seal caps. Do not over tighten.
• Replace the service valve caps finger-tight and then tighten with an open-end
wrench adequately to seal caps. Do not over tighten.
• Replace control box cover and service panel and install screws to secure service
panel.
• Restore power to unit at disconnect if required.
• Configure indoor thermostat per the thermostat installation instructions and set
thermostat to desired mode and temperature.
17.0 ACCESSORIES
17.1 Remote Outdoor Temperature Kit (Part No. 47-102709-03)
This is a kit that has a longer remote sensor that can be installed away from the out-
door unit for better thermostat temperature display.
17.2 RXME-A02 Communicating 2 Wire Kit
This kit will allow the outdoor unit to communicate to the system with only 2 wires.
18.0 TROUBLESHOOTING
IMPORTANT: The JEC series units with the ICC (Integrated Compressor Control)
provide status and diagnostic information that greatly enhances the ability to quickly
diagnose system faults. Use the following troubleshooting guides as another tool in
system diagnostics.
!
NOTICE
Systems should not be fine tune charged below 40°F outdoor dry bulb.
SATURATION
TEMP
(Deg. F)
R-410A
PSIG
SATURATION
TEMP
(Deg. F)
R-410A
PSIG
SATURATION
TEMP
(Deg. F)
R-410A
PSIG
SATURATION
TEMP
(Deg. F)
R-410A
PSIG
-150
-
-30
17.9 35
107.5
100
317.4
-140
-
-25
22
40
118.5
105
340.6
-130
-
-20
26.4 45
130.2
110
365.1
-120
-
-15
31.3 50
142.7
115
390.9
-110
-
-10
36.5 55
156.0
120
418.0
-100
-
-5
42.2 60
170.1
125
446.5
-90
-
0
48.4
65
185.1
130
476.5
-80
-
5
55.1
70
201.0
135
508.0
-70
-
10
62.4
75
217.8
140
541.2
-60
0.4
15
70.2
80
235.6
145
576.0
-50
5.1
20
78.5
85
254.5
150
612.8
-40
10.9
25
87.5
90
274.3
-35
14.2
30
97.2
95
295.3
TABLE 7