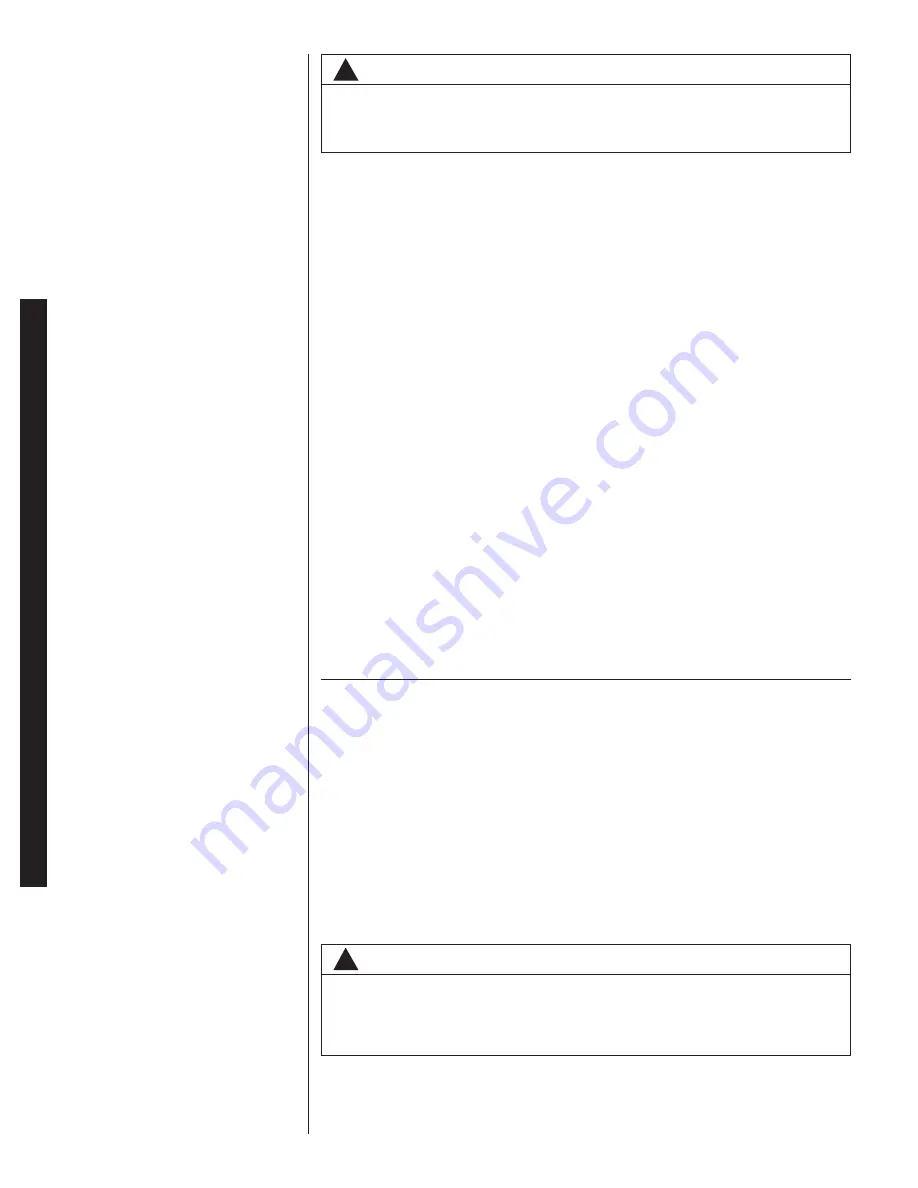
11.1 Evacuation Procedure
Evacuation is the most important part of the entire service procedure. The life and
efficiency of the equipment is dependent upon the thoroughness exercised by the
serviceman when evacuating air and moisture from the system.
Air or nitrogen in the system causes high condensing temperatures and pressure,
resulting in increased power input and non-verifiable performance.
Moisture chemically reacts with the refrigerant and oil to form corrosive hydrofluoric
acid. This attacks motor windings and parts, causing breakdown.
• After the system has been leak-checked and proven sealed, connect the vacuum
pump and evacuate system to 500 microns and hold 500 microns or less for at
least 15 minutes. the vacuum pump must be connected to both the high and low
sides of the system by connecting to the two pressure ports. Use the largest size
connections available since restrictive service connections may lead to false
readings because of pressure drop through the fittings.
• After adequate evacuation, open both service valves by removing both brass ser-
vice valve caps with an adjustable wrench. Insert a 3/16” [5 mm] hex wrench into
the stem and turn counterclockwise until the wrench stops.
• At this time gauges must be connected to the access fitting on the liquid line
(small) service valve and the common suction port connected to the common
suction line between the reversing valve and compressor to check and adjust
charge.
IMPORTANT: Compressors (especially scroll type) should never be used to evacu-
ate the air conditioning system because internal electrical arcing may result in a
damaged or failed compressor. Never run a scroll compressor while the system is in
a vacuum or compressor failure will occur.
FINAL LEAK TESTING
After the unit has been properly evacuated and service valves opened, a halogen
leak detector should be used to detect leaks in the system. All piping within the heat
pump, evaporator, and interconnecting tubing should be checked for leaks. If a leak
is detected, the refrigerant should be recovered before repairing the leak. The
Clean Air Act prohibits releasinig refrigerant into the atmosphere.
12.0 CONDENSING UNITS EQUIPPED WITH THE
11.0
COMFORT CONTROL
2
SYSTEM™
Comfort Control
2
is the next generation of the Integrated Compressor Control (ICC)
and is an integral part of the Comfort Control
2
System™ with the following features:
12.1 Control Description (see Figure 3)
Dual 7-Segment LED
• Displays status and diagnostic codes (See Status and Diagnostic Description)
• Displays diagnostic/fault recall (See Test Mode/Fault Recall)
RED LED (Y1)
• Y1 red LED (solid on) indicates Y1 call from thermostat is present
Line Voltage Connector
• Line voltage is connected to control board at lug terminals L1 & L2
• Maximum wire size accepted is 6 AWG copper wire
18
!
CAUTION
THE COMPRESSOR HAS AN INTERNAL OVERLOAD PROTECTOR. UNDER
SOME CONDITIONS, IT CAN TAKE UP TO 2 HOURS FOR THIS OVERLOAD
TO RESET. MAKE SURE OVERLOAD HAS HAD TIME TO RESET BEFORE
CONDEMNING THE COMPRESSOR.
!
CAUTION
UNIT MAY START SUDDENLY AND WITHOUT WARNING
Solid red light indicates a thermostat call for unit operation is present at
the ICC control. ICC control will attempt to start unit after short cycle timer
expires or when in Active Protection mode will attempt to restart unit prior
to Lockout mode.
Comfort Control
2
System™
CONTROL WIRING