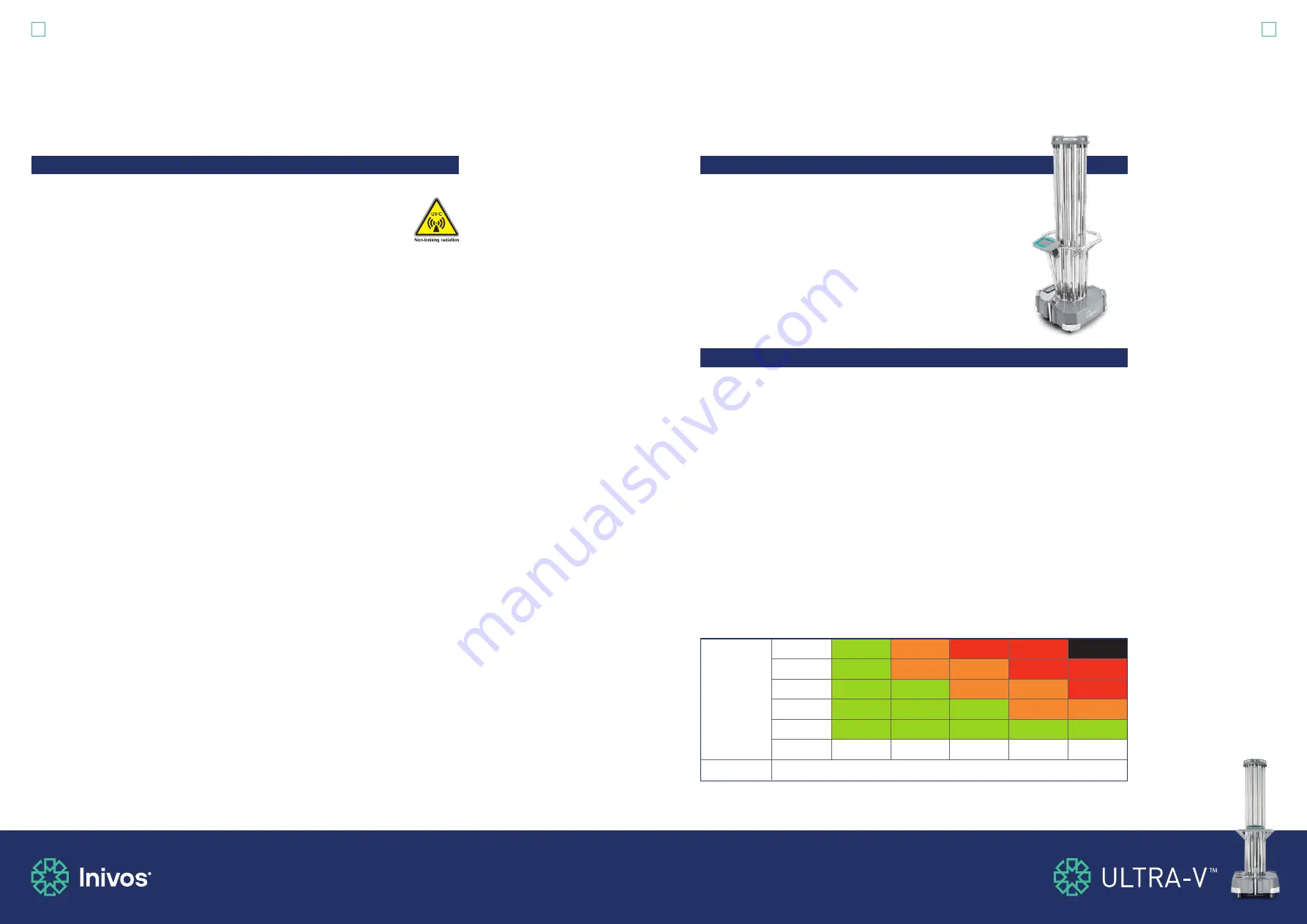
8
inivos.com
9002_ULTRA-V_INSTRUCTION MANUAL_V1/0820
9002_ULTRA-V_INSTRUCTION MANUAL_V1/0820
9
2.3
Ultra-V
™
Process Safety
In order to avoid these potential risks of the UV-C light the Ultra-V™ system comes with a
number of safety and security features that are designed to minimize the potential risk of
accidental UV-C exposure:
1.
The operator must secure all the entrance/exit points to the treatment area and
display visual warning signs at all the entrance points to the space. Use Inivos tape
to block any potential UV-C Light leakage.
2.
In case of emergency, a “Stop Process” soft button is available during the process on the
screen of the Ultra-V™ Process Monitor (BB), pressing it will switch off the lamps immediately
and carry out safety checks. Do not enter room while the Process Monitor is performing safety
checks.
3.
The Ultra-V™ Process Monitor communicates with the Ultra-V™ main unit by Wi-Fi, this
communication is checked every 10 seconds, in the case that the communication is lost,
Ultra-V™ automatically switches off the lamps.
4.
As a last resort, Ultra-V™ units are equipped with a movement sensor system (C) that
automatically switch off the lamps when any movement is detected. Therefore, if someone
inadvertently enters the treatment area, Ultra-V™ will automatically switch off the lamps to
minimise exposure to UV-C light. This safety feature is last resort, putting any person very
close to the hazard, and therefore must not be used to switch off the Ultra-V system light.
5.
UV-C Light emitting lamps (B) feature a polymer coating sleeve which is designed to safely
contain any glass in case of breakage.
6.
The lamps of the Ultra-V™ system are provided with special lamp glass that filters out the
wave-lengths which produce ozone, therefore the amount of ozone produced during the
decontamination is negligible. If possible, allow the room to be ventilated before entering after
the decontamination process.
7.
Site specific risk assessment must be carried out taking into account hazards identified in this
manual and the hazard analysis and reduction report.
3.1
Pre-operation checks
Remove soft cover and stow away safely. Position the system in the
room to be decontaminated.
Each Ultra-V
™
system is individually tested for full functionality and
calibrated before despatch. There is a small amount of machine set
up required before use.
Check the Ultra-V
™
system for damage after unpacking. Do not
connect the electrical supply if any damage is identified. Check each
bulb for damage.
Check the spectormes LED’s light up, if not replace the batteries.
Section 3:
Before using the Ultra-V
™
system
Likelihood
5
5
10
15
20
25
4
4
8
12
16
20
3
3
6
9
12
15
2
2
4
6
8
10
1
1
2
3
4
5
1
2
3
4
5
Consequence
3.2
Hazard Analysis and Risk Reduction Report
This document follows a standard risk evaluation and preventative action process to
understand hazards and minimise risk to operators and to ensure process efficiency.
Through a process of implementation and audit of standard operating procedures, risk
associated with Ultra-V
™
Decontamination Process can be minimised independent of
operator ability, ensuring safe operation of the Ultra-V
™
System within the healthcare setting.
Quantitative Risk Assessment scoring
Likelihood scoring:
1.
Rare - Will probably never happen or recur
(unlikely to occur /may happen sometime in 5 to 25 years)
2.
Possible (under unfortunate circumstances) - Unlikely - Not expected to happen or
recur, but possible (Possible to occur in time; may happen sometime in 2 to 5 years)
3.
Possible - Might Happen or recur occasionally (Possible to occur in time; may happen
sometime in 2 to 5 years)
4.
Probable - Likely - Will probably happen or recur, but is not a persisting issue or
circumstance (Probably will occur in time; may happen sometime in 1 to 2 years)
5.
Almost Certain - Very Likely - Very likely to happen or recur: possibly frequently (likely to
occur immediately or within a short period of time; may happen several times in one year)