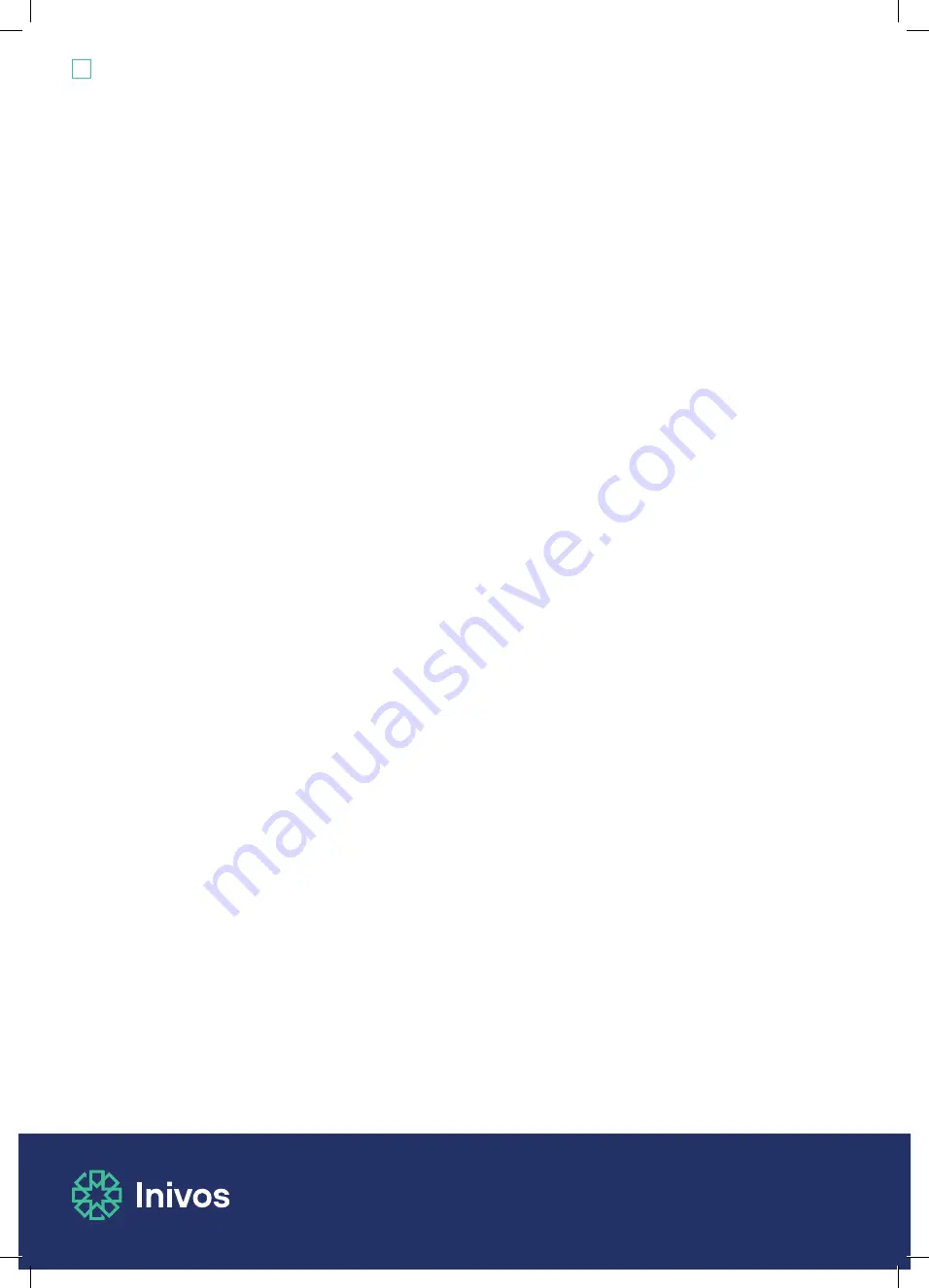
52
www.
inivos
.com
INSTRUCTION MANUAL
REVISION 4.0 • APRIL
2020
External dimensions (mm)
1275mm H x 725mm W x 650mm D with and without process monitor
attached
Weight (drained of fluid)
Approx 113 Kg
Storage temperature range
0–60 °C
Operational temperature range
10– 35 °C
Operational humidity range
15–85% RH
Fluid storage capacity
6.8 Litres (full), 7.5 Litres (max)
Ultrasonic frequency
Approx 1.7 MHz
Atomised droplet size
2-5 m
Power consumption
1500 W
Supply voltage range
220-240 V AC
Supply frequency
50/60 Hz
Plug fuse
13 A
Operational SPL
<70 dB(A)
Section 7:
Specifications
Summary of Contents for ProXcide
Page 8: ...8 www inivos com INSTRUCTION MANUAL REVISION 4 0 APRIL 2020 1 2 ...
Page 41: ...APRIL 2020 REVISION 4 0 INSTRUCTION MANUAL 41 Issue 4 Pop up box for issue 4 ...
Page 42: ...42 www inivos com INSTRUCTION MANUAL REVISION 4 0 APRIL 2020 Issue 5 Pop up box for issue 5 ...
Page 43: ...APRIL 2020 REVISION 4 0 INSTRUCTION MANUAL 43 Issues 12 Pop up box for issue 12 ...
Page 44: ...44 www inivos com INSTRUCTION MANUAL REVISION 4 0 APRIL 2020 Issue 13 Pop up box for issue 13 ...
Page 45: ...APRIL 2020 REVISION 4 0 INSTRUCTION MANUAL 45 Issues 16 to 20 Pop up box for issues 16 20 ...