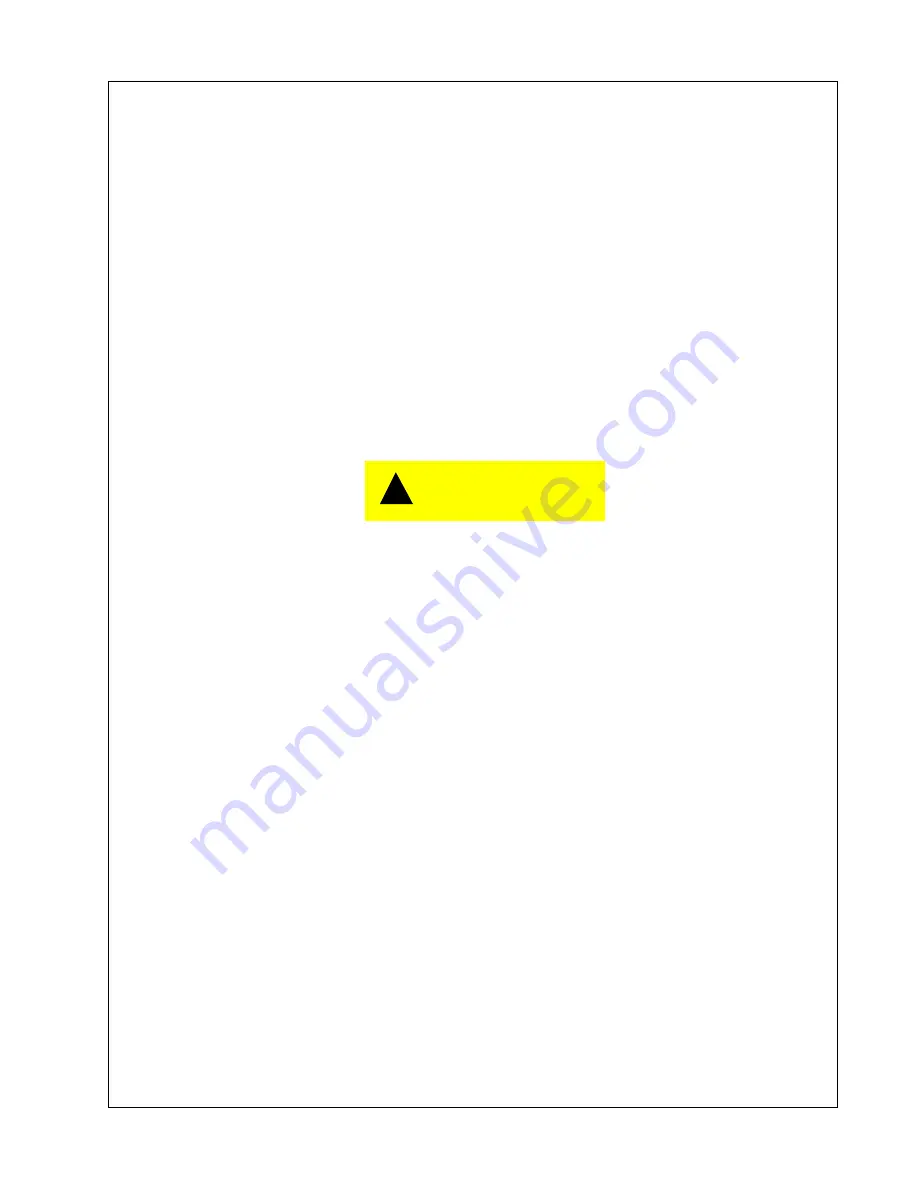
Installation
Operation & Maintenance Manual
23221138 (12-07) Rev A
23
An unloader valve triggers when the maximum set discharge pressure is reached, causing the
engine to throttle back and the reduced compressor output to be discharged overboard at very
low pressure. The nominal settings from the factory are unload at 175 psig and load at 145
psig. The unload pressure is adjustable at the unloader valve from 175 psig to 100 psig.
Mounting Unit
Satisfactory installation depends upon the ability of the installer. Refer to the appropriate
foundation plan for the dimensions of the compressor package.
Choose a clean, relatively cool location for the compressor package, and provide ample space
around the unit for general accessibility and to ensure effective heat dissipation. Extreme care
must be taken in locating an air-cooled unit of this type so there is an unrestricted supply of air
to the cooling fan, which pulls air into the package. The air exiting the package must flow away
from the unit so that it may be readily dissipated to atmosphere without recirculating hot air to
the fan intake. Any recirculation of the cooling air may result in an excessively high compressor
operating temperature.
CAUTION
!
Do NOT mount the unit with either the fan or cooler side of the machine
facing forward on a vehicle such that unrestricted airflow from motion of
the vehicle may enter the unit. Mounting the unit this way will cause wind
milling of the fan that can damage it. Mounting with this orientation must
be done behind a cab or other wind blocking structure.
The compressor package must be located so the instrument panel will be fully visible. If
desired the instrument cluster may be moved to the opposite side of the compressor. To move,
switch the gauges with the hole covers on the opposite side.
Exact level is not absolutely necessary, but it is recommended the unit be leveled with a
carpenter’s level set on the compressor housing. Leveling may be accomplished by shimming
the unit near the unit’s bolting holes. Use only steel shims. Mounting holes are provided on the
bottom of the base.
The mounting hole pattern of the compressor base and the optional fuel tank / receiver tank
module is identical, so that the tank module can be mounted later without drilling more holes
or separately using the same template.
Sufficient space must be provided at all service openings to provide ready access for service
and maintenance. For installations such as under the bed of a truck, it may be desirable to
provide a sliding mount tray for the compressor to facilitate servicing. For this type mounting,
care must be exercised to provide adequate piping and wiring slack to allow the unit to move
for service.
Summary of Contents for VHP40RMD
Page 5: ...23221138 12 07 Rev A 5 Safety...
Page 15: ...23221138 12 07 Rev A 15 Warranty...
Page 21: ...23221138 12 07 Rev A 21 Installation...
Page 29: ...23221138 12 07 Rev A 29 General Data...
Page 32: ...Operation Maintenance Manual General Data 32 23221138 12 07 Rev A...
Page 33: ...23221138 12 07 Rev A 31 Operating Instructions...
Page 41: ...23221138 12 07 Rev A 37 Maintenance Lubrication...
Page 50: ...Always use Ingersoll Rand Replacement parts 46 23221138 12 07 Rev A...