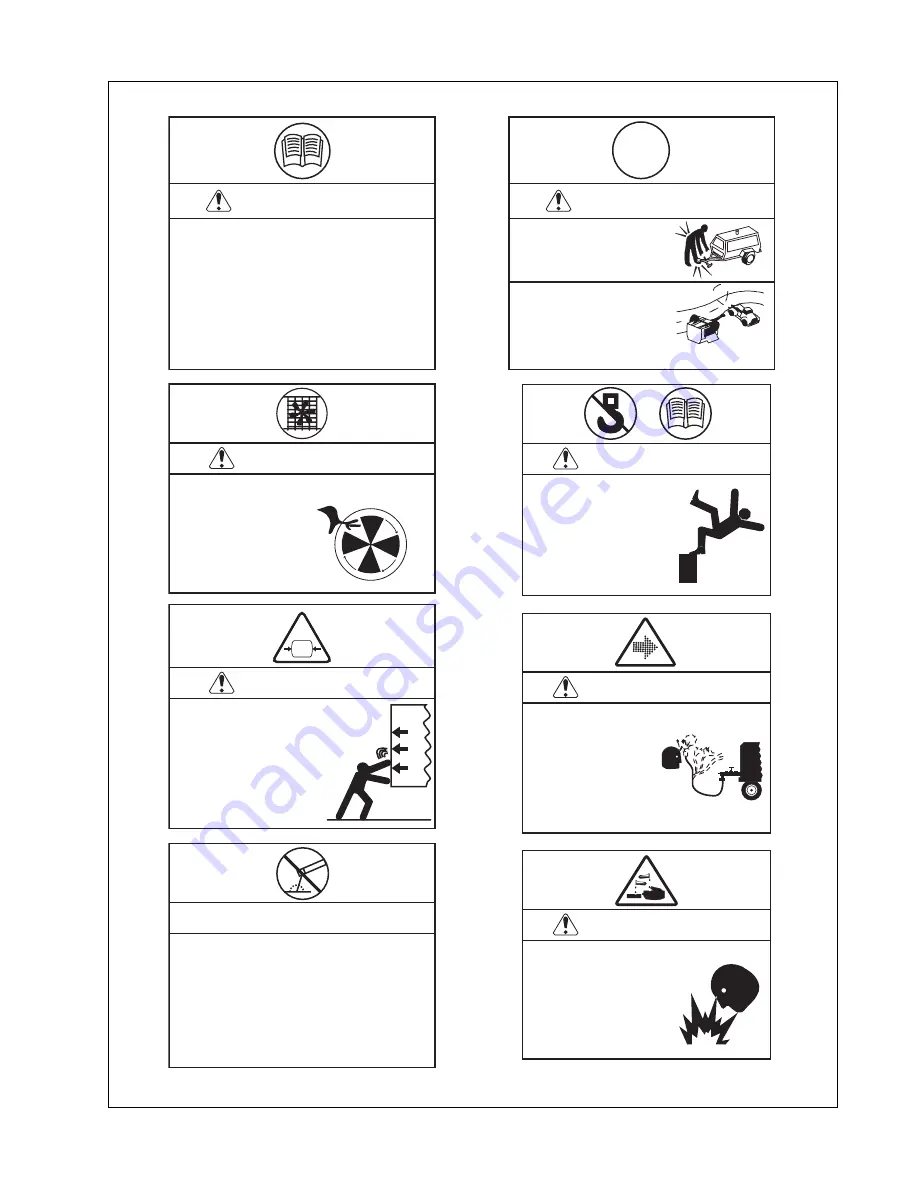
Safety
Operation & Maintenance Manual
23221138 (12-07) Rev A
13
WARNING
Modification or alternation of this machine.
Can cause serious injury or death.
Do not alter modify this machine
without the express written consent of
the manufacturer.
Improper operation of this equipment.
Can cause serious injury or death.
Read Operator's Manual supplied with
this machine before operation or
servicing.
WARNING
Rotating fan blade.
Can cause serious injury.
Do not operate without
guard on place.
Disconnected air hoses whip.
Can cause serious
injury or death.
When using air tools
attach safety device
(OSHA valve) at source of
air supply for each tool.
WARNING
WARNING
Combustible gas.
Can cause serious burns,
blindness or death.
Keep sparks and open
flames away from batteries.
Falling of machine.
Can cause serious injury
or death.
Access lifting bail from
inside machine.
WARNING
WARNING
Door under pressure.
Can cause serious injury.
Use both hands to open door
when machine is running.
CAUTION
DO NOT WELD.
ELECTRONIC DAMAGE
WILL OCCUR.
This engine is equipped with an
electronic engine controller and
other electronic components.
WARNING
Excessive towing speed.
Can cause serious injury
or death.
Do NOT exceed 65 mph (105 km/hr.)
Collapsing jackstand.
Can cause serious injury.
Insert locking pin completely.
105
km/h
Summary of Contents for VHP40RMD
Page 5: ...23221138 12 07 Rev A 5 Safety...
Page 15: ...23221138 12 07 Rev A 15 Warranty...
Page 21: ...23221138 12 07 Rev A 21 Installation...
Page 29: ...23221138 12 07 Rev A 29 General Data...
Page 32: ...Operation Maintenance Manual General Data 32 23221138 12 07 Rev A...
Page 33: ...23221138 12 07 Rev A 31 Operating Instructions...
Page 41: ...23221138 12 07 Rev A 37 Maintenance Lubrication...
Page 50: ...Always use Ingersoll Rand Replacement parts 46 23221138 12 07 Rev A...