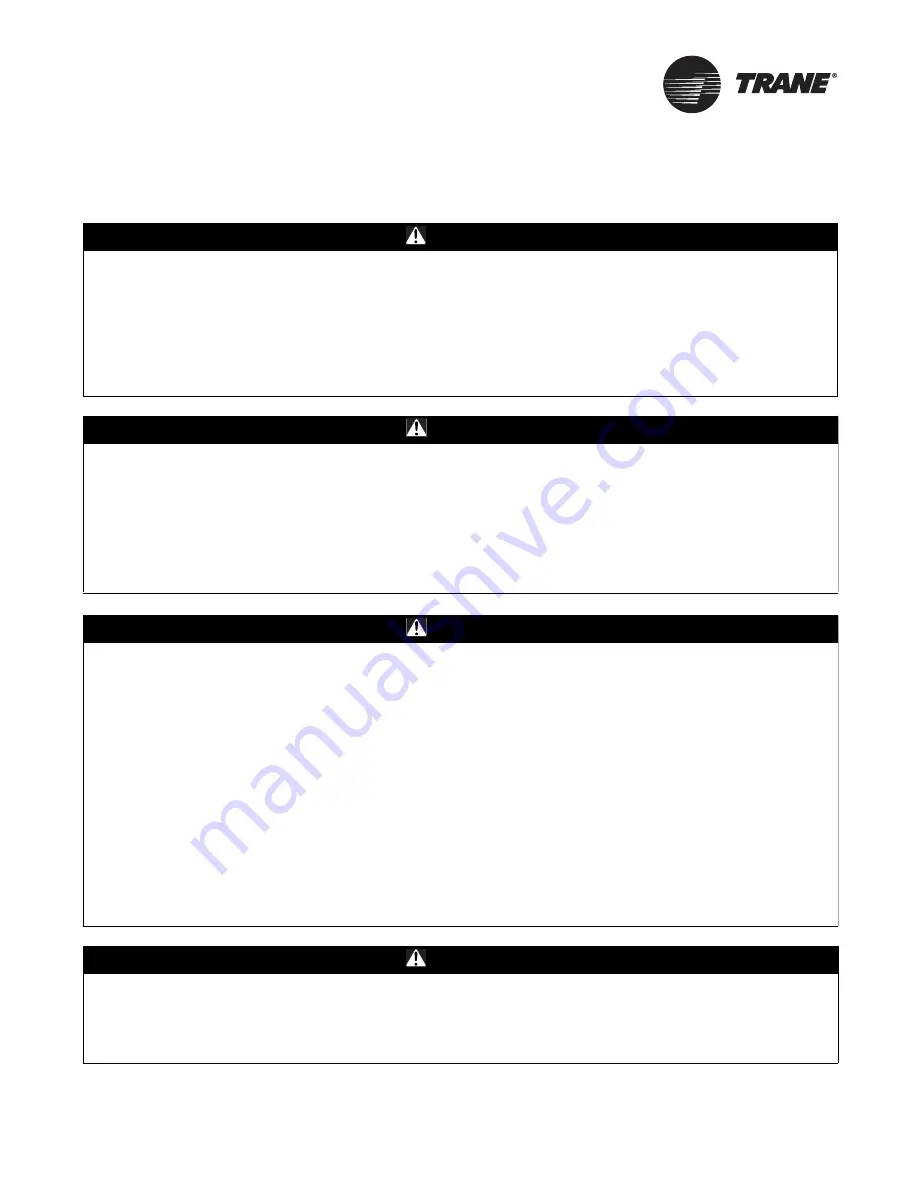
AFDJ-ADF001A-EN (10 Oct 2014)
1
PowerFlex 7000 “A” or “B” Frame Pre-Commissioning Check List
Remote-Mounted Medium Voltage Air-Cooled Adaptive Frequency™ Drive (Model: AFDJ)
WARNING
Safety Alert!
Failure to follow the instructions below could result in death or serious injury. In addition to the following tasks, you
MUST:
•
Follow all instructions in the Adaptive Frequency drive and the CenTraVac™ chiller Installation, Operation, and
Maintenance manuals, including warnings, cautions, and notices.
•
Perform all required tasks in any applicable Service Alerts and Service Bulletins.
•
Review and understand all information provided in Submittals and Design Specifications.
WARNING
Hazardous Procedures!
Failure to follow all instructions provided could result in death or serious injury. The following procedures could result
in exposure to electrical, mechanical or other potential safety hazards. Always refer to the safety warnings provided
throughout the Adaptive Frequency drive and CenTraVac chiller Installation, Operation, and Maintenance manuals
concerning these procedures. Unless specified otherwise, disconnect all electrical power including remote
disconnect and discharge all energy storing devices such as capacitors before servicing. Follow proper lockout/
tagout procedures to ensure the power can not be inadvertently energized. When necessary to work with live
electrical components, have a qualified licensed electrician or other individual who has been trained in handling live
electrical components perform these tasks.
WARNING
Personal Protective Equipment (PPE) Required!
Installing/servicing this unit could result in exposure to electrical, mechanical and chemical hazards.
•
Before installing/servicing this unit, technicians MUST put on all PPE required for the work being undertaken
(Examples; cut resistant gloves/sleeves, butyl gloves, safety glasses, hard hat/bump cap, fall protection, electrical
PPE and arc flash clothing). ALWAYS refer to appropriate Material Safety Data Sheets (MSDS)/Safety Data Sheets
(SDS) and OSHA guidelines for proper PPE.
•
When working with or around hazardous chemicals, ALWAYS refer to the appropriate MSDS/SDS and OSHA/GHS
(Global Harmonized System of Classification and Labelling of Chemicals) guidelines for information on allowable
personal exposure levels, proper respiratory protection and handling instructions.
•
If there is a risk of energized electrical contact, arc, or flash, technicians MUST put on all PPE in accordance with
OSHA, NFPA 70E, or other country-specific requirements for arc flash protection, PRIOR to servicing the unit. NEVER
PERFORM ANY SWITCHING, DISCONNECTING, OR VOLTAGE TESTING WITHOUT PROPER ELECTRICAL PPE AND
ARC FLASH CLOTHING. ENSURE ELECTRICAL METERS AND EQUIPMENT ARE PROPERLY RATED FOR INTENDED
VOLTAGE.
Failure to follow instructions could result in death or serious injury.
WARNING
Proper Field Wiring and Grounding Required!
Failure to follow code could result in death or serious injury. All field wiring MUST be performed by qualified
personnel. Improperly installed and grounded field wiring poses FIRE and ELECTROCUTION hazards. To avoid these
hazards, you MUST follow requirements for field wiring installation and grounding as described in NEC and your
local/state electrical codes.