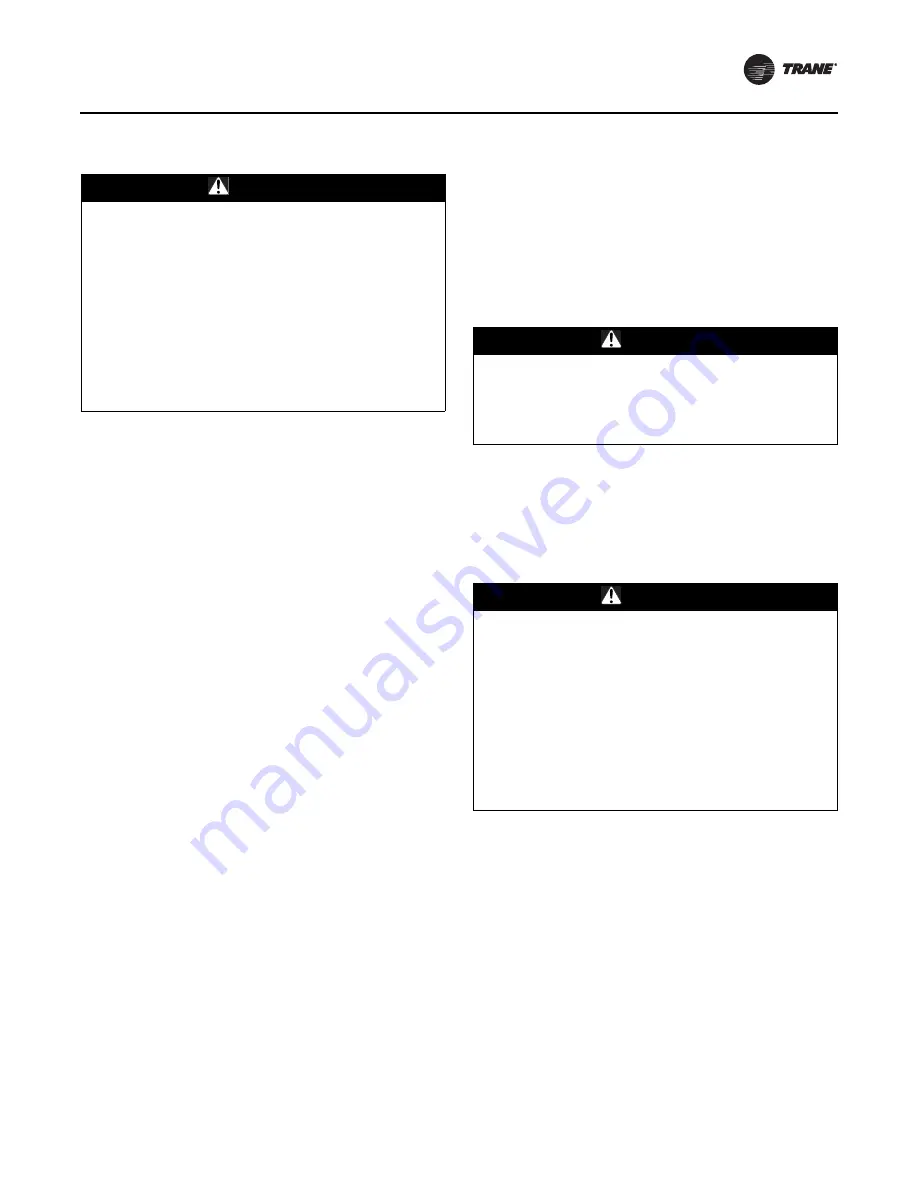
Wiring
AFDJ-SVU01D-EN
39
Torquing Electrical Power Connections
Use a torque wrench to tighten power connections. A
torque wrench eliminates the human element and
provides proper hardware tightening.
Proper torque for connections depends on both the bolting
materials and the metals being connected. Strand
migration will occur when the copper is under prolonged
pressure.
Electrical power terminations should be rechecked for
tightness when the apparatus is first installed and
periodically afterwards. The conductor could flow under
prolonged pressure. Thermal cycling will be greater
during the first few months in operation.
Most hardware used for making a bolted electrical joint
will be low carbon steel. The hardware does not carry
electrical current but holds the two conducting surfaces
together under pressure. When properly torqued, the
slight elongation of the bolt or screw acts to maintain
pressure on the electrical joint. The thermal expansion of
steel is less than that of the conducting metals, which is
usually copper.
The pressure at the electrical joint will vary slightly during
thermal cycling and reduces somewhat when there is cold
flow in the conducting metals. Re-torquing will re-
establish the surface pressure, which is essential to
keeping a low resistance drop between the two
conducting surfaces and avoiding eventual failure.
Cabinet Wire Routing
All wiring should be installed in conformance with the
applicable local, national, and international codes (for
example, NEC/CEC). Control wiring enters the cabinet
through the left side and terminates at the control panel’s
terminal block. Tighten the control wire connections to
7.1 to 8.9 in·lb (0.8 to 1.0 N·m).
Wire Routing
Wire Sizing
Care should be taken to see that all interconnection wiring
and ground wiring is sized and installed in conformance
with the National Electrical Code (NEC), the National Fire
Protection Association (NFPA), or the Canadian Electrical
Code (CEC) as applicable, and other appropriate local
codes. Refer to controller and motor nameplates for
electrical data.
Important:
•
Before servicing, disconnect all power sources and
allow at least 40 minutes for capacitors to discharge.
•
All electrical enclosures-unit or remote-are IP2X.
Grounding the Cabinet
Refer to submittals for power lug sizes and location along
with control wiring specifics for the controller.
Use the following steps to ground the cabinet:
1.
Open the left-hand enclosure door of the drive. The
grounding stud is located just above and to the left of
the breaker.
2. Run a suitable earth ground completed by field) to the
cabinet’s ground connection point. The grounding lug
is capable of accepting up to 4/0 AWG wire. For AWG/
MCM equivalents in mm
2
, refer to
.
Tighten the ground connections to 375 in·lb
(42.4 N·m).
WARNING
Hazardous Voltage w/Capacitors!
Disconnect all electric power, including remote
disconnects and discharge all motor start/run
capacitors before servicing. Follow proper lockout/
tagout procedures to ensure the power cannot be
inadvertently energized. For variable frequency drives
or other energy storing components provided by Trane
or others, refer to the appropriate manufacturer’s
literature for allowable waiting periods for discharge of
capacitors. Verify with an appropriate voltmeter that all
capacitors have discharged. Failure to disconnect
power and discharge capacitors before servicing could
result in death or serious injury.
WARNING
Hazardous Voltage/Improper Grounding!
Hazardous voltage due to improperly grounded
electrical components could result in death or serious
injury. The motor controller has a chassis ground that
must be connected to an earth ground.
WARNING
Proper Field Wiring and Grounding
Required!
Failure to follow code could result in death or serious
injury. A ground wire must be connected to the
enclosure. The motor frame must also be grounded to
the drive controller. All field wiring MUST be performed
by qualified personnel. Improperly installed and
grounded field wiring poses FIRE and ELECTROCUTION
hazards. To avoid these hazards, you MUST follow
requirements for field wiring installation and grounding
as described in NEC and your local/state electrical
codes.