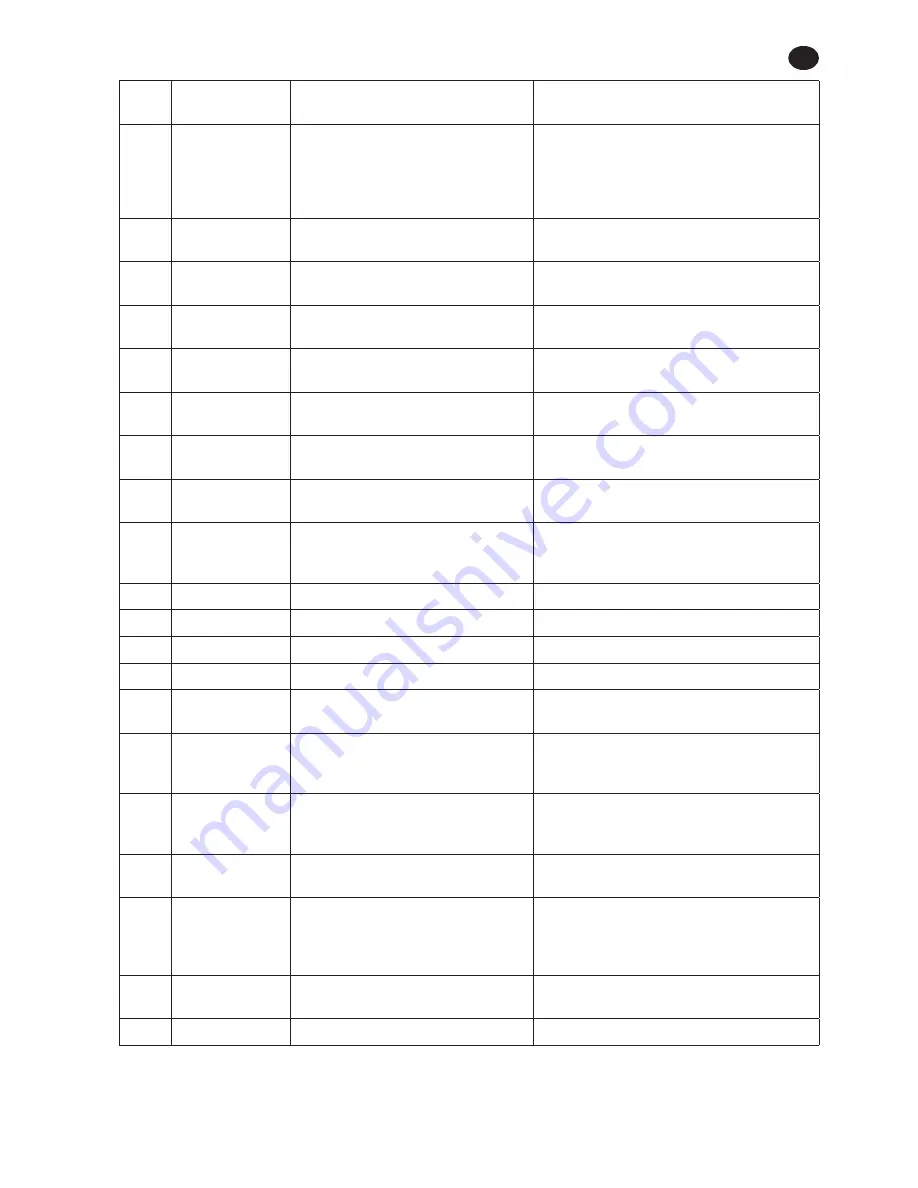
48619852_ed3
EN-22
EN
Fault
Code
Category
Notes
Actions/Solutions
E-02
Motor Controller Fault
I2T Fault.
Too much current being drawn over an extended
amount of time. Add a 10 second delay between
cycles to try and remedy. If it is a very soft joint,
try raising the shift down point so that the
majority of the cycle is run at high speed.
E-03
Motor Controller Fault
Motor Stall.
Possible damaged electronics hardware.
Contact the IR Service Center for service.
E-04
Motor Controller Fault
Motor current.
Possible damaged electronics hardware.
Contact the IR Service Center for service.
E-05
Motor Controller Fault
Over temperature.
Add a delay between cycles to allow time for
the tool to cool.
E-06
Motor Controller Fault
Current Offset.
Possible damaged electronics hardware.
Contact the IR Service Center for service.
E-0
Motor Controller Fault
Shunt Calibration.
Faulty transducer or transducer wire. Contact
the IR Service Center for service.
E-08
Motor Controller Fault
Torque Offset Fault.
Faulty transducer or transducer wire. Contact
the IR Service Center for service.
E-09
Motor Controller Fault
Transducer Fault.
Faulty transducer or transducer wire. Contact
the IR Service Center for service.
E-10
Motor Controller Fault
Under Angle.
Angle low limit is too high or the user released the
trigger before the cycle was complete. The user should
keep the trigger engaged until the cycle is complete.
E-11
Motor Controller Fault Current Plausibility Low.
Current Plausibility Low Failure.
E-12
Motor Controller Fault
Early Trigger Release.
The trigger was released before the cycle completed.
E-13
Motor Controller Fault Motor Controller Watchdog Reset.
Motor Controller Watchdog Reset.
E-14
Motor Controller Fault Motor Controller Stop Timeout.
Motor Controller Stop Timeout.
E-18
Motor Controller Fault
Multi-step configuration did not
complete due to early trigger release.
Cycle failed during one of the early stages of a prevailing
torque strategy. Retry or check the joint for problems.
E-81
Motor Controller Fault
The configuration ID in the Motor
controller’s EOR did not match the
currently selected configuration.
Configuration data in EOR does not match
currently selected configuration.
E-0A
Motor Controller Fault
Step Execution Timeout.
Check the joint for stripped threads. If the joint
is a soft joint, extend the step timeout parameter
for the fastening configuration being run.
E-0B,
E-15
Motor Controller Fault
Communication message timeouts.
Try pulling the trigger again.
E-0C
Motor Controller Fault
Over Torque limit.
Torque high limit is too low or the joint is too
hard for the fastening settings. For a hard
joint, try lowering the free speed to 0% and/
or lowering the shift down torque.
E-0D
Motor Controller Fault
Over Angle Limit.
Check the joint for stripped threads. Angle limit is too
low or the joint is too soft for the fastening settings.
E-0E
Motor Controller Fault Current Plausibility High.
Current Plausibility High Failure.
RELEASED 18/Apr/2014