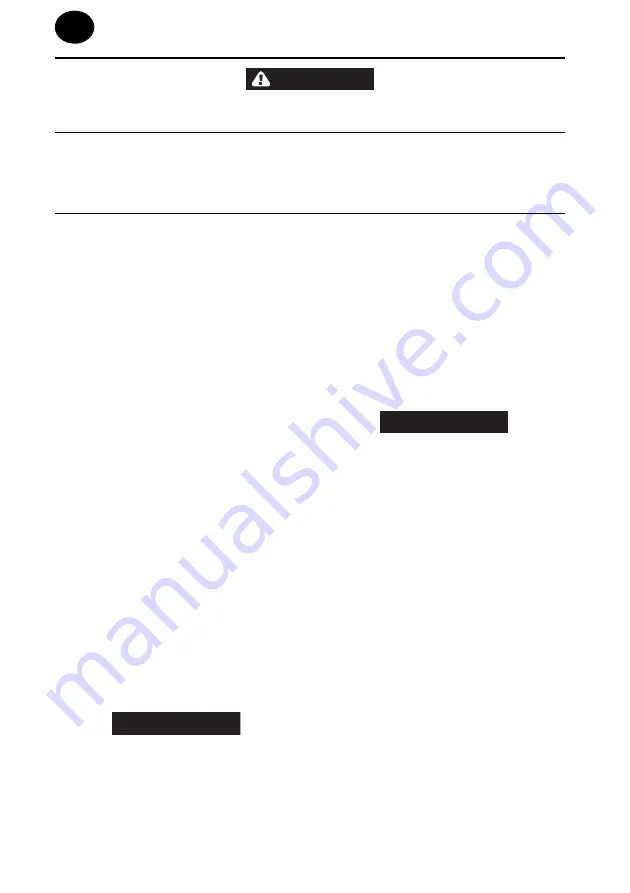
EN-1
16575003_ed1
EN
WARNING
Always use protective eye wear when performing maintenance on a tool or operating tool.
Always turn of the air supply and disconnect the air supply hose before installing, removing or adjusting any accessory
on this tool, or before performing any maintenance on this tool. Failure to do so could result in injury.
Lubrication
Each time model HDS and TDS Sanders and Polishers are
disassembled for maintenance, repair or replacement of
parts, lubricate the tools:
1. Always wipe the Vanes (17) with a light film of oil before
inserting them into the vane slots.
2. Inject 0.5 to 1.0 cc of
Ingersoll Rand
No. 10 Oil into the
air Inlet Assembly (1) after assembly.
3. Moisten all O-Rings with O-Ring lubricant.
Disassembly
General Instructions
1. Do not disassemble the tool any further than necessary
to replace or repair damaged parts.
2. Do not press any needle bearing from a part unless you
have a new needle bearing on hand for installation.
Needle bearings are always damaged during the removal
process.
3. When grasping a tool or part in a vise, always use
leather-covered or copper-covered vise jaws to protect
the surface of the part or tool and help prevent distortion.
This is particularly true of threaded members and
housings.
4. Do no remove any part which is a press fit in or on a
subassembly unless the removal of that part is necessary
for repairs or replacement.
5. Do not disassemble the tool unless you have a complete
set of new gaskets and O-Rings for replacement.
Disassembly of Extension Assembly
1. Using the Collet Body Wrench (82) on the flats of the
Collet Body (58) and the Collet Nut Wrench (81) on the
Collet Nut (60), unscrew the Collet Nut and remove the
Collet (59).
2. Loosen the Mounting Screw Nut (64) and slide the
assembled handle off the Collet end of the Extension
Housing (51).
3. Using snap ring pliers, remove the Shield Retainer (57)
and slide the Spindle Bearing Shield (56) out of the
Extension Housing.
4. Using a thin blade screwdriver, pry the Extension
Housing Plug (52) out of the Extension Housing. Insert a
5/32" steel rod into the opening and through the hole in
the Spindle (44) to prevent it from rotating and using the
Collet Body Wrench, unscrew and remove the Collet
Body.
5. Remove the Seal Cup Assembly (55) from the Collet
body.
6. Grasp the tool in copper-covered vise jaws with the
Spindle upward and using the Gear Case Adapter
Wrench (83) on the flats of the Gear Case Adapter (32)
and a 1-1/2" wrench on the flats of the Extension
Housing, unscrew and remove the Housing. This is a
left-hand thread
and must be rotated
clockwise
to
remove the Housing.
NOTICE
Some of the gears will be free to fall from the spindle
gear shafts when the Housing is separated from the
Adapter. Make certain they do not fall on a hard surface
which could damage them.
7.
For HDS30, HDS45, TDS30 or TDS45,
remove the
Spindle Planet Gears (45 or 47), Planet Gear Bearings
(46), the Ring Gear (34) and the Ring Gear Clamp (43)
from the motor end of the Extension Housing.
For HDS10 or TDS15,
remove the Gear head (39), Gear
Head Planet Gears (40), Bearings (41), Gear Head
Spacer (42), Spindle Planet Gears (45 or 47), Bearings
(48), Ring Gear (34) and the Ring Gear Clamp (43) from
the motor end of the Extension Housing.
For HDS60, HDS90, TDS90 or TDS120,
pull the
assembled Gear Frame (25) off the spline of the Spindle
(44).
8.
For HDS60, HDS90, TDS90 or TDS120,
if the Spur
Gears (36), Spur Gear Bearings (37) or Spur Gear Pins
(38) do not need to be replaced, set the assembled Gear
Frame aside. If any of the components must be replaced,
proceed as follows:
NOTICE
The Spur Gear Bearings will be damaged during
removal. Make certain a new set of bearings is available
before attempting to disassemble the Gear Frame.
a. Stand the assembled Gear Frame on the table of an
arbor press and using a pressing plug having a
diameter equal to the size of the Spur Gear Pin, press
the Bearing from the Gear Frame.
b. Push the Pin from the Spur Gear and lift the Spur
Gear out of the Gear Frame.
c. Repeat step (a) and (b) for the remaining two Spur
Gears.
d. Turn the Gear Frame end for end and press the
remaining Bearings from the Gear Frame.
9. Grasp the gear end of the assembled Spindle and pull it
out of the Extension Housing.
10. If the Front Bearing Spindle Seal (54) is nicked or
damaged and must be replaced, remove it from the
internal groove near the output end of the Extension
Housing.
11. If the Front Spindle Bearing (53) must be replaced, use a
bearing puller to pull the Bearing off the front end of the
Spindle.
12. If the Rear Spindle Bearing (49) must be replaced, use
snap ring pliers to remove the Rear Spindle Bearing
Retainer (50) and using a bearing puller, pull the Bearing
from the Spindle.
13.
For HDS60, HDS90, TDS90 or TDS120,
if the Rear
Spindle Bearing Seal (49A) is nicked or damaged and
must be replaced, remove it from the groove in the
spindle shaft where the Rear Spindle Bearing was
located.
14. Using the Gear Case Adapter Wrench, unscrew and
remove the Gear Case Adapter. This is a
left-hand
thread
; rotate the Adapter
clockwise
to remove it.
15. Remove the Clamp Sleeve (30) and if the Wick (29) must
be replaced, pull it from the motor end of the spacer.