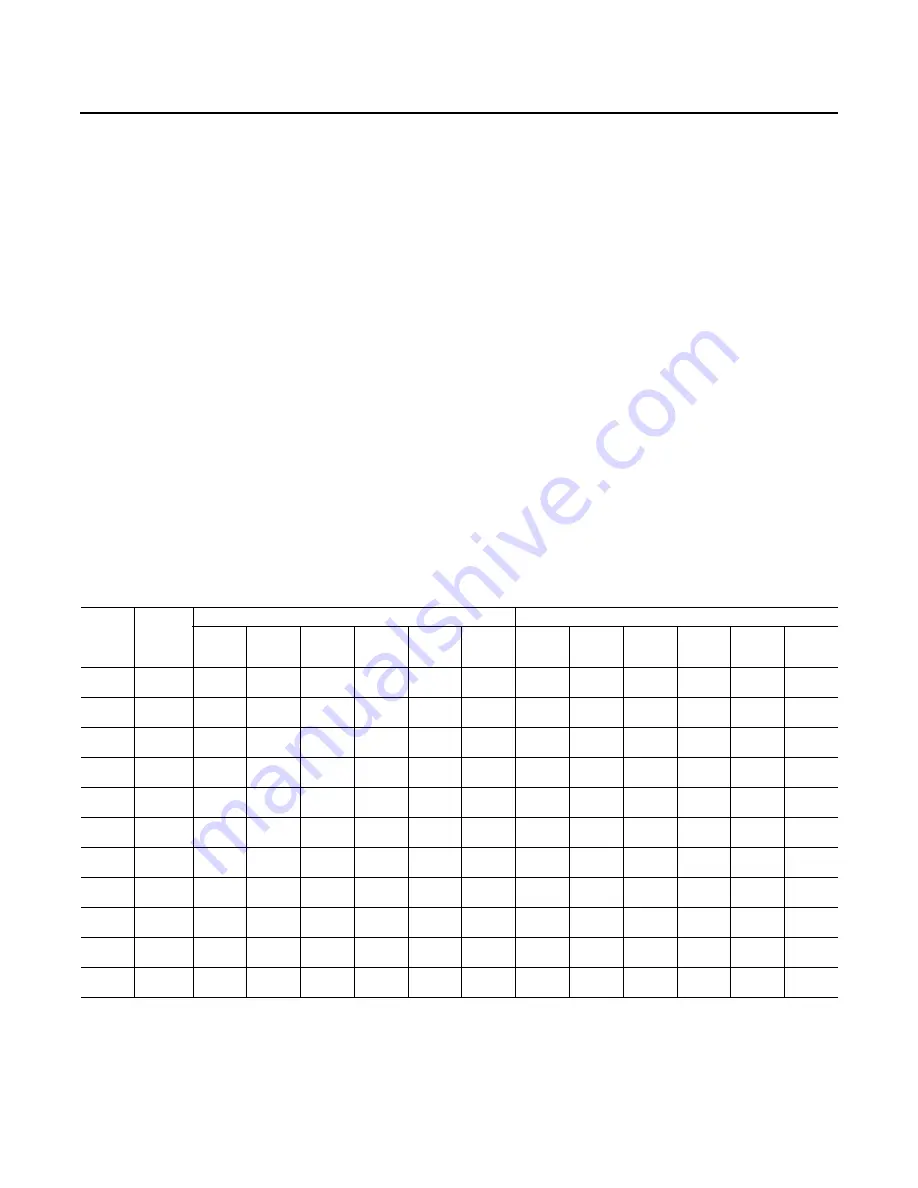
Maintenance
RT-SVX51B-EN
31
Due to the soft material and thin walls of the MCHE coils,
the traditional field maintenance method recommended
for Round Tube Plate Fin (RTPF) coils does not apply to
microchannel coils.
Moreover, chemical cleaners are a risk factor to MCHE due
to the material of the coil. The manufacturer does not
recommend the use of chemical cleaners to clean
microchannel coils. Using chemical cleaners could lead to
warranty claims being further evaluated for validity and
failure analysis.
The recommended cleaning method for microchannel
condenser coils is pressurized water or air with a non-
pinpoint nozzle and an ECU of at least 180 with pressure no
greater than 600 psi. To minimize the risk of coil damage,
approach the cleaning of the coil with the pressure washer
aimed perpendicular to the face of the coil during cleaning.
Optimum clearance between the sprayer nozzle and the
microchannel coil is 1”–3”.
Final Process
For future reference, you may find it helpful to record the
unit data requested below in the blanks provided.
(1) Complete Unit Model Number:
_____________________________________________________
(2) Unit Serial Number:
_____________________________________________________
(3) Wiring Diagram Numbers (from unit control panel)
— schematic(s)
_____________________________________________________
_____________________________________________________
— connection(s)
_____________________________________________________
____________________________________________________
Table 10.
Sample maintenance log
Date
Current
Ambient
Temp F/C
Refrigerant Circuit #1
Refrigerant Circuit #2
Compr.
Oil Level
Suct.
Press.
Psig/kPa
Disch.
Press
Psig/kPa
Liquid
Press
Psig/kPa
Super-
heat F/C
Sub-cool
F/C
Compr.
Oil Level
Suct.
Press.
Psig/kPa
Disch.
Press
Psig/kPa
Liquid
Press
Psig/kPa
Super-
heat F/C
Sub-cool
F/C
- ok
- low
- ok
- low
- ok
- low
- ok
- low
- ok
- low
- ok
- low
- ok
- low
- ok
- low
- ok
- low
- ok
- low
- ok
- low
- ok
- low
- ok
- low
- ok
- low
- ok
- low
- ok
- low
- ok
- low
- ok
- low
- ok
- low
- ok
- low
- ok
- low
- ok
- low