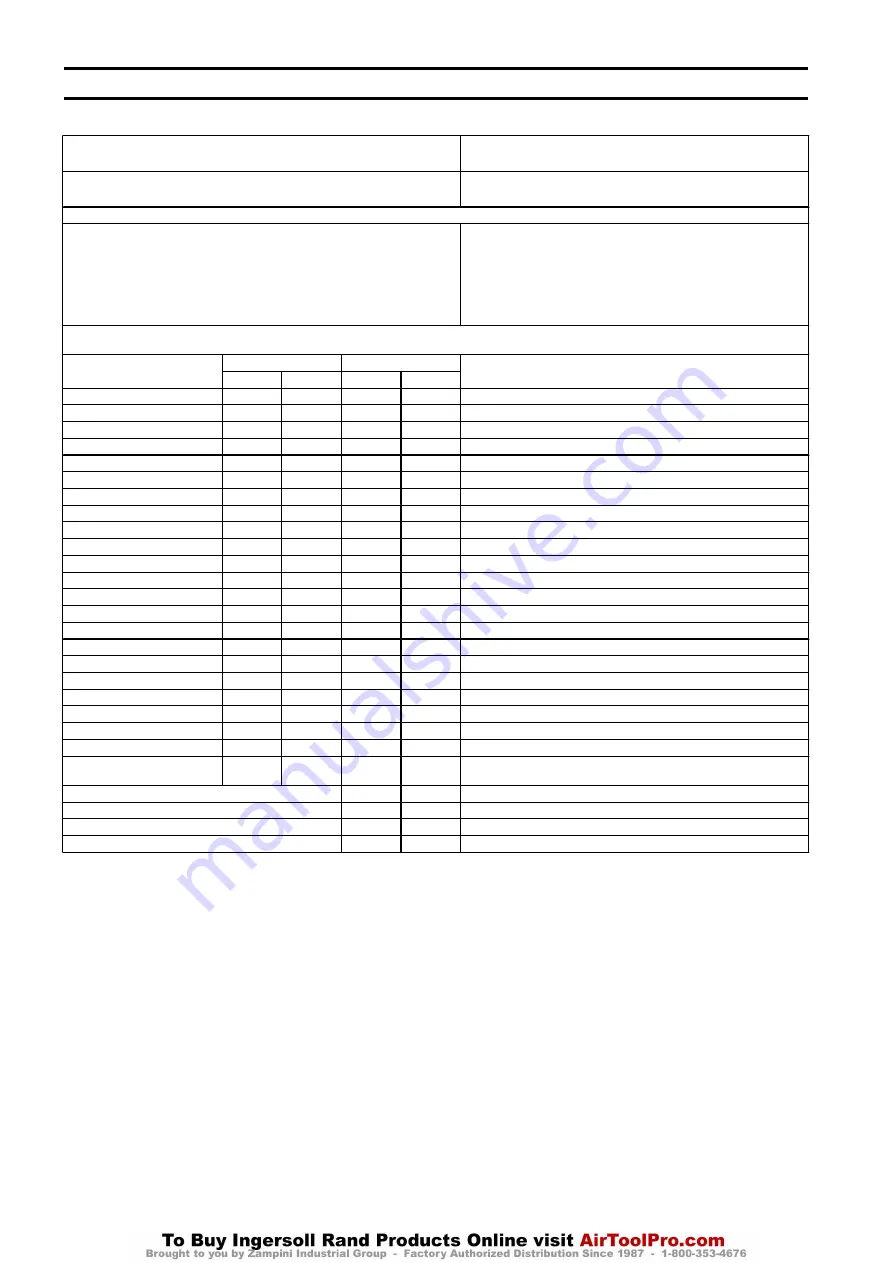
INSPECTION REPORT
Ingersoll Rand Force 5 Infinity Series Models FA2i, FA2.5i, FA5i or FA5Ti Air Winches
Model Number:
Date:
Serial Number:
Inspected by:
Reason for Inspection: (Check Applicable Box)
1. Scheduled Periodic Inspection:
(_____ Months _____ Years)
Operating Environment:
Normal ____ Heavy____ Severe ____
2. Discrepancy(s) noted during Frequent Inspection
3. Discrepancy(s) noted during maintenance
4. Other: ___________________________
Refer to the Product Information Manual and Product Parts Information Manual and “INSPECTION” section for general inspection criteria. Also, refer to appropriate National
Standards and Codes of practice. If in doubt about an existing condition, contact the nearest Ingersoll Rand Distributor or the factory for technical assistance.
COMPONENT
CONDITION
CORRECTIVE ACTION
NOTES
Pass
Fail
Repair
Replace
Uprights and Siderails
Drum Band Brake (125% Load Test)
Drum Locking Pin
Disc Brake (125% Load Test)
Drum Band Brake (Visual Inspection)
Disc Brake (Visual Inspection)
Motor
Limit Switches
---
Controls
Constant Tensioning Manifold
---
Air System
Fasteners
Reduction Gears
Labels and Tags
---
Shafts
Winch Guard
Wire Rope Wedge
---
Emergency Stop Valve
Overload Device
---
Press Roller
Wire Rope
---
Drum Locking Pin
---
Other Components (list in NOTES
section)
TESTING
Pass
Fail
NOTES
Operational (No Load)
Operational (10% Load)
Operational (Maximum Test Load*)
*
Maximum test load is 125% of rated line pull. Testing to more than 125% of rated load may be required to comply with standards and regulations set forth in areas
outside the USA.
This form may be photo copied and used as an inspection record.
4
Form MHD56303 Edition 2