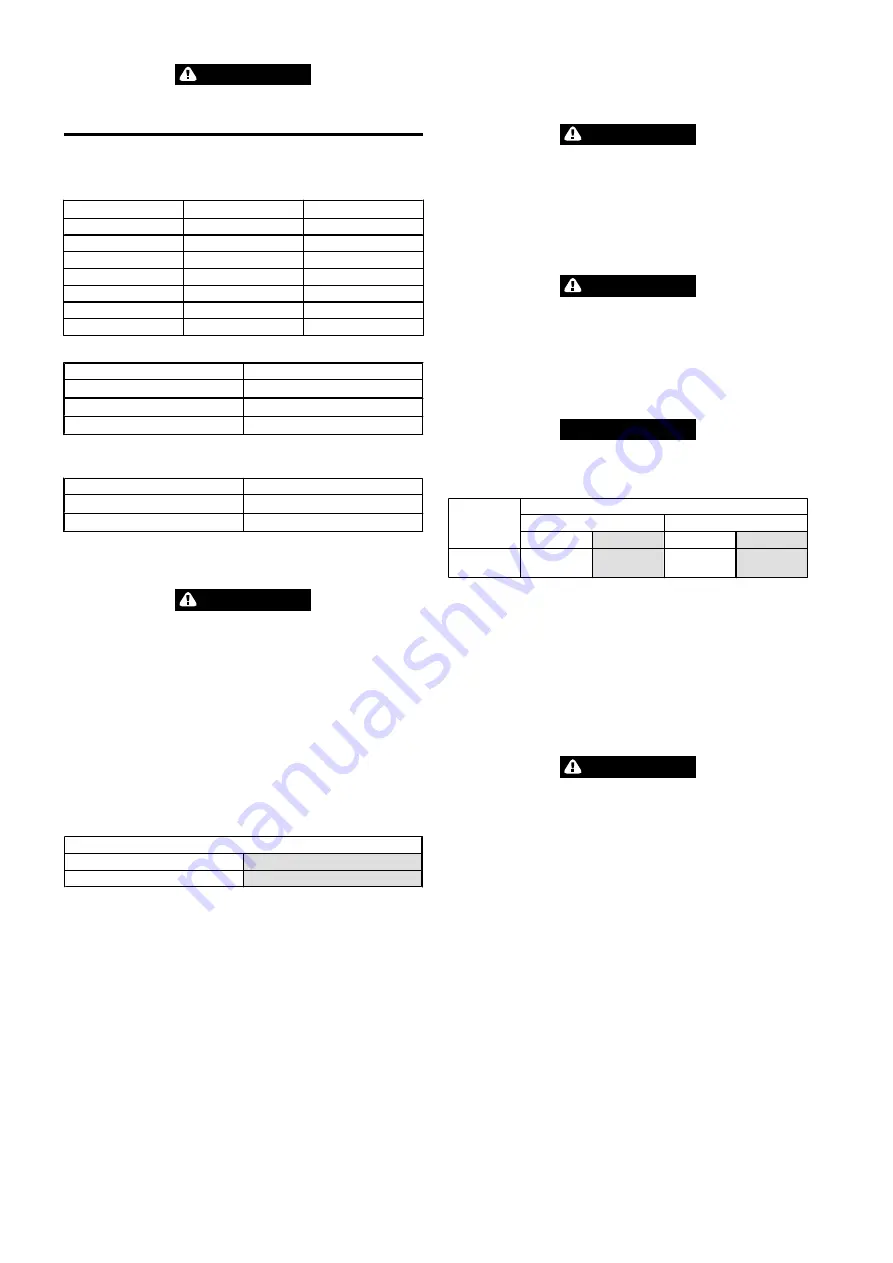
WARNING
•
Pneumatic products use oil to prevent excessive heat buildup and to
prevent wear that could cause sparks. Oil levels must be properly
maintained.
n
Recommended Lubricants
Table 10: Synthetic Lubricants Recommended for the Reduction Gear and Disc
Brake
Ambient Temperature
0
°
C/+20
°
C
+20
°
C+40
°
C
SHELL
TIVELA S150
TIVELA S220
AGIP
BLASIA S150
BLASIA S220
ESSO
GLYCOLUBE 150
GLYCOLUBE 220
IP
PONTIAX HDS
PONTIAX HDS
KLUBER
SYNTHESO D150 EP
SYNTHESO D220 EP
MOBIL
SHC 629
SHC 630
BP-MACH
ERNESYN HTX 220
Table 11: Air Motor Recommended Lubricant Grade
Temperature
Grade Type
Below 32
°
F (0
°
C)
ISO VG 32 (SAE 10W)
32
°
to 80
°
F (0
°
to 27
°
C)
ISO VG 68 (SAE 20W) *
Above 80
°
F (27
°
C)
ISO VG 100 (SAE 30W)
* Units are shipped from factory with ISO VG 68 (SAE 20W) lubricant.
Table 12: Recommended Grease Grade
Temperature
Grade Type
-20
°
to 50
°
F (-30
°
to 10
°
C)
EP 1 multipurpose lithium based grease
30
°
to 120
°
F (-1
°
to 49
°
C)
EP 2 multipurpose lithium based grease
n
Motor Assembly
Refer to Dwg. MHP0222 on page 13, A. Level Plug; B. Drain Plug; C. Fill Plug.
CAUTION
•
Do not use synthetic or detergent lubricants in air motor. Synthetic
lubricants will result in oil blowing by piston rings.
The motor is splash lubricated by oil in motor housing and has no other means of
lubrication. It is therefore important to use only good quality, non-detergent motor
oil to ensure maximum performance and minimum downtime for repairs. Refer to
‘Recommended Lubricants’ on page 10.
Add oil through filler opening until oil flows from level plug hole. Add oil slowly to
prevent spilling. Refer to ‘Recommended Lubricants’ on page 10.
The motor should be level-checked daily or at the start of each shift after any
accumulated water has been drained off. When motors are operated in temperatures
below freezing, wait long enough at the end of shift for water to separate from oil
but not long enough for it to freeze. Drain water then refill to level plug, located on
side of motor housing. If desired, all oil may be drained at end of shift and motor
refilled with new oil.
Table 13: Motor Oil Capacity
Capacity
quarts
litres
3/8
0.35
n
Reduction Gear Assembly
Refer to Dwg. MHP0140 on page 14, A. Fill Plug Position; B. Drum; C. Reduction
Gear Assembly; D. Inboard Upright; E. Level Plug Position.
The reduction gear is filled to the correct levels prior to shipment from the factory.
Check oil level before initial winch operation. This component is splash lubricated
by oil in the housing and has no other means of lubrication. It is therefore important
to use high quality Extreme Pressure (EP) rust and oxidation inhibited gear oil to
ensure maximum performance and minimum down time for repair.
CAUTION
•
Do not over fill. Excess oil will reduce operating efficiency and increase oil
temperature.
•
Only use synthetic lubricant in reduction gear.
To ensure correct performance, highest efficiency and long life, it is essential that
lubricating oil be maintained at correct level. Rotate drum until fill plug is located at
top dead center then add oil up to level plug hole. Refer to Table 14 ‘Reduction Gear
and Disc Brake Capacities’ on page 10 for capacities.
n
Disc Brake Assembly
CAUTION
•
Do not attempt to lubricate disc brake with grease. The breather plug on
top of the brake housing must not be used as a grease fitting.
•
Only use synthetic lubricant in disc brake.
Refer to Dwg. MHP1348 on page 12, A. Breather Plug; B. Drain Plug; C. Level Plug.
The friction plates and drive plates are in a self contained oil bath and have no other
means of lubrication. After an oil change or winch overhaul remove the breather
plug and pour a small amount of oil through breather hole in brake housing. Allow
oil to fully settle between fillings. Refer to Table 14 ‘Reduction Gear and Disc Brake
NOTICE
•
If too much oil is added excess oil will be discharged through breather plug
when control valve is actuated.
Table 14: Reduction Gear and Disc Brake Capacities
Models
Capacity
Reduction Gear
Disc Brake
quarts
litres
ounces
litres
FA2i-MR &
FA2i-MR-CE
1-1/2
1.4
4 to 6
0.2
n
Seals and Bearings
If product is disassembled, clean all parts thoroughly and coat bearings and seals
with clean grease. Refer to ‘Recommended Lubricants’ section on page 10. Use
sufficient grease to provide a good protective coat. Lubricate grease fittings monthly
with 2 or 3 pumps of a grease gun.
n
Wire Rope
Follow the wire rope manufacturer’s instructions. At a minimum, observe the
following guidelines.
1. Clean with a brush or steam to remove dirt, rock dust or other foreign material
on the surface of the wire rope.
CAUTION
•
Do NOT use an acid-based solvent. Only use cleaning fluids specified by the
wire rope manufacturer.
2. Apply a wire rope lubricant.
3. Brush, drip or spray lubricant weekly, or more frequently, depending on severity
of service.
10
Form MHD56437 Edition 7