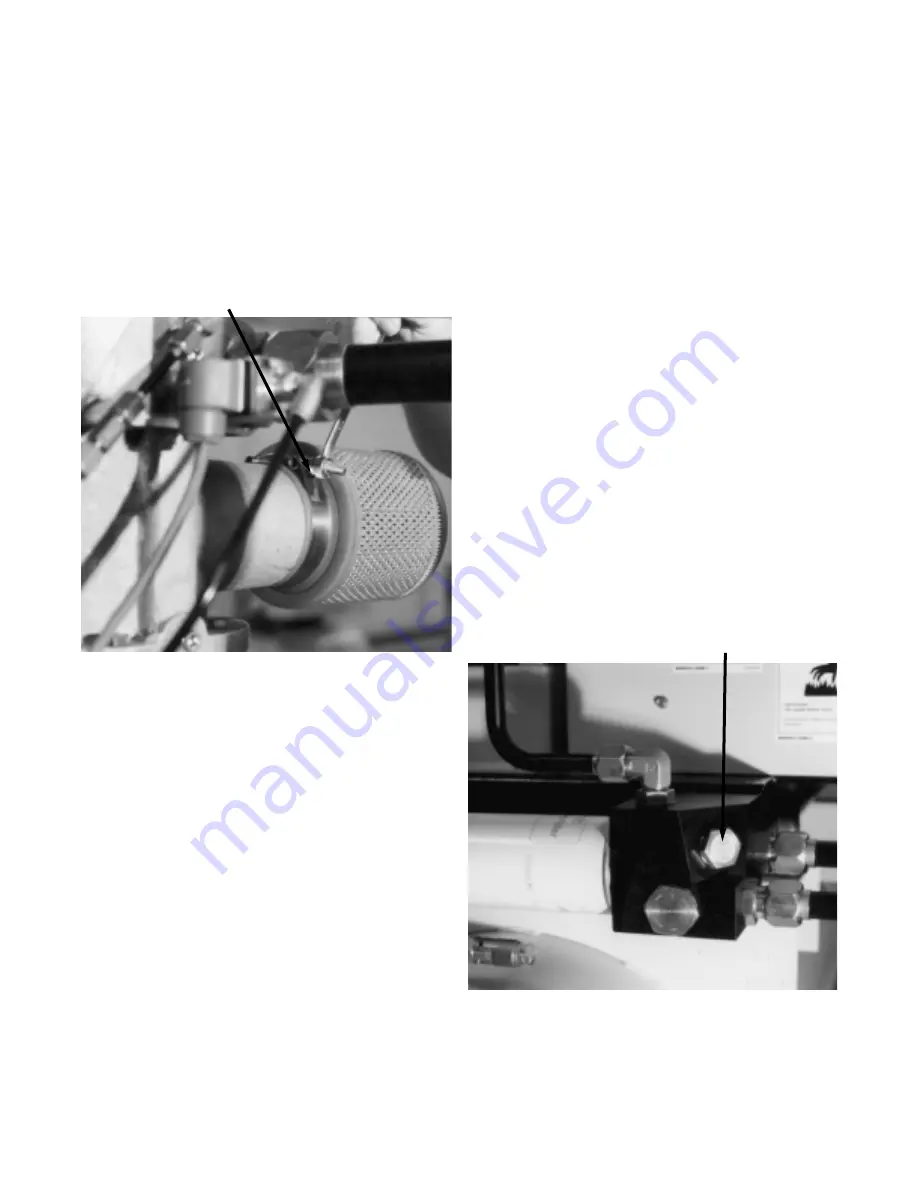
25
4.9 INLET AIR FILTER ELEMENT
The inlet air filter should be changed at the interval
shown in the maintenance chart or any time the filter
becomes dirty.
The filter element is not washable and must be
replaced. Remove the filter by loosening the clamp on
the filter assembly located on the Inlet Control Valve.
Remove and discard the old filter element. Install a
new filter element. Tighten clamp (See Figure 4.9-1).
FIGURE 4.9-1 INLET AIR FILTER
4.10 COOLANT FILTER
Time of change - after the first 150 hours and every
1000 hours thereafter, or when the coolant is being
changed. In dirty operating environments, the filter
should be changed more frequently.
Before beginning any work on the compressor, open,
lock and tag the main electrical disconnect and close
the isolation valve on the compressor discharge. Wait
2 minutes after stopping to allow internal pressure to
dissipate. Vent residual pressure from the unit by slow-
ly unscrewing the coolant fill plug one turn.
Unscrewing the fill plug opens a vent hole, drilled in
the plug, allowing the pressure to release to atmos-
phere (See Figure 4.3-1). A slight mist or oil droplets
may be visible during venting. Do not remove fill plug
until all pressure has vented from the unit. Also vent
piping by slightly opening the drip leg valve . When
opening the drain valve or removing the coolant fill
plug, stand clear of the valve discharge, wear work
gloves and appropriate eye protection.
SPECIAL TOOLS
Suitable clean drain pan or container to hold coolant
drained from unit.
A quantity of proper coolant sufficient to top off the
coolant level in the compressor.
One genuine IR replacement coolant filter of the prop-
er type for the unit.
1. Place a clean pan under the coolant filter.
2. Using a filter wrench, remove the coolant filter.
Remember that the filter and coolant may be hot!
3. Discard the old filter.
4. Wipe the sealing surface of the filter head with a
clean lint-free rag to prevent entry of dirt into the sys-
tem.
5. Remove the replacement filter from its protective
package.
6. Apply a small amount of clean coolant on the rubber
seal of the filter.
7. Screw filter on until the seal makes contact with the
seat on the filter header. Tighten approximately one
half to three quarters turn additional.
8. Remove coolant fill plug (See Figure 4.10-1).
FIGURE 4.10-1 FILL PLUG
CLAMP
FILL PLUG
Summary of Contents for EP 20-ESP
Page 35: ...33 6 0 REFERENCE DRAWINGS 6 1 ELECTRICAL SCHEMATIC FULL VOLTAGE 39884143 REV 01...
Page 36: ...34 6 2 ELECTRICAL SCHEMATIC STAR DELTA 39884150 REV 01...
Page 38: ...36 6 4 FOUNDATION PLAN TANK MOUNTED CONTINUED 39871975 REV 03...
Page 39: ...37 6 4 FOUNDATION PLAN TANK MOUNTED 39871975 REV 03...
Page 40: ...38 6 5 FOUNDATION PLAN BASE MOUNTED CONTINUED 39872835 REV 03...
Page 41: ...39 6 5 FOUNDATION PLAN BASE MOUNTED 39872835 REV 03...
Page 44: ...42 39876461 REV 02...
Page 46: ...44 39880844 REV 01...
Page 48: ...46 39872031 REV 01 SEE PIPING ASSEMBLY OPTIONS...
Page 52: ...50 39872023 REV 02 TO AFTERCOOLER TO AFTERCOOLER...
Page 57: ...55 DATE RUN TIME WORK DONE QTY UNIT WORK HOURS MEASURE BY 8 0 MAINTENANCE RECORD...
Page 58: ...56 DATE RUN TIME WORK DONE QTY UNIT WORK HOURS MEASURE BY MAINTENANCE RECORD...