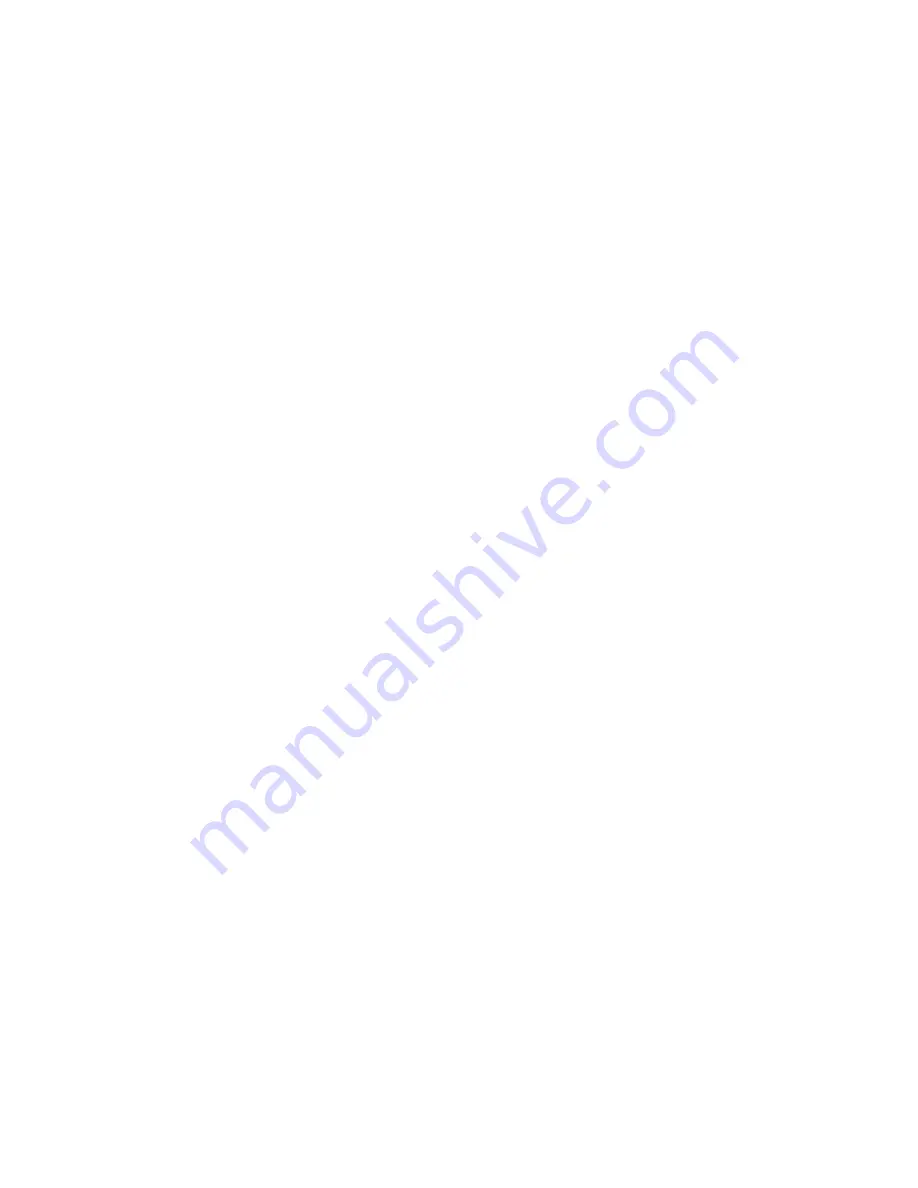
14
2. Check coolant level. To check coolant level, slowly
loosen the fill plug one complete turn. As the fill plug is
unscrewed approximately one turn, a small amount of
pressure may be released. Do not remove the fill plug
until all pressure has been vented. Once pressure is
vented, finish removing the fill plug. The proper coolant
level is when the coolant is at the top of the fill port.
Add coolant if necessary.
3. Replace and tighten the fill plug.
4. Close the main disconnect switch (ON position).
5. Verify that the main isolation valve is open.
Starting
1. Pull the Start/Stop button to the ON position and
release. The compressor will start and then load auto-
matically if line pressure is below the lower setting of
the pressure switch.
Stopping
1. Depress the Start/Stop button to the OFF position.
Compressor will stop immediately.
2. Open the main disconnect switch (OFF position).
3.0 SYSTEMS
3.1 GENERAL SYSTEM INFORMATION
The compressor is an electric motor driven, single
stage, rotary screw compressor, complete with sup-
porting components to make a fully functional unit. A
standard compressor is composed of the following:
Inlet air filter
Drive motor
Airend
Pressurized coolant system with cooler & filter
Separation system
Capacity control
Instruments
Safety devices
Compression in the rotary screw type air compressor
is created by the meshing of two helical rotors (male
and female) on parallel shafts, enclosed in a heavy
duty iron housing, with air inlet and outlet ports located
on opposite ends. The grooves of the female rotor
mesh with and are driven by the male rotor. Bearings
on both ends of the rotors are used to support the
rotor both laterally and axially.
3.2 COOLANT SYSTEM
The coolant system consists of a “L” shaped tube sep-
arator, thermostatic element, coolant filter, coolant
cooler with fans, and a separator element. When the
unit is operating, the coolant is pressurized and forced
to the compressor bearings. The compressor is provid-
ed with a temperature switch which will shut the unit
down in case of excessive temperature, 228°F
(109°C). Effective coolant filtration is provided by the
use of a screw on, automotive type, heavy duty
coolant filter.
The compressor is designed for operation in an ambi-
ent range of 35°F to 115°F (2°C to 46°C).
COOLANT
Rotary screw compressor fluids have a triple function
to perform. They lubricate the bearings and contacting
surfaces of the rotors, seal internal clearances within
the rotor chamber, and provide for the cooling of the
compression process. The bulk of the fluid is actually
used for cooling, with only small amounts used for
lubrication and sealing.
ESP air compressors are factory filled with 1000
ROTALUBE
TM
1000 COOLANT. ROTALUBE
TM
1000
COOLANT is designed to operate for 1,000 hours
or one year, whichever comes first. The coolant
must be changed at these intervals to avoid break-
down and equipment damage.
CIRCULATION OF COOLANT
Coolant is forced by air pressure from the tube separa-
tor to the thermostatic element. The temperature rating
of the element will determine whether the coolant cir-
culates through the cooler, bypasses the cooler, or
mixes the two paths together to maintain an optimum
compressor injection temperature. This temperature is
controlled to preclude the possibility of water vapor
condensing. By injecting coolant at a sufficiently high
temperature, the discharge air coolant mixture temper-
ature will be kept above the dew point.
Before being injected into the airend, all coolant flows
through the coolant filter. It is an automotive type full-
flow filter with a single replacement spin-on element,
rated at 10 micron. There is a differential-pressure
bypass valve set to open in the event that the pres-
sure drop across the filter rises to as high as 35 psi
(2.5 bar), which indicates an excessively fouled ele-
ment as well as poor maintenance practice.
Summary of Contents for EP 20-ESP
Page 35: ...33 6 0 REFERENCE DRAWINGS 6 1 ELECTRICAL SCHEMATIC FULL VOLTAGE 39884143 REV 01...
Page 36: ...34 6 2 ELECTRICAL SCHEMATIC STAR DELTA 39884150 REV 01...
Page 38: ...36 6 4 FOUNDATION PLAN TANK MOUNTED CONTINUED 39871975 REV 03...
Page 39: ...37 6 4 FOUNDATION PLAN TANK MOUNTED 39871975 REV 03...
Page 40: ...38 6 5 FOUNDATION PLAN BASE MOUNTED CONTINUED 39872835 REV 03...
Page 41: ...39 6 5 FOUNDATION PLAN BASE MOUNTED 39872835 REV 03...
Page 44: ...42 39876461 REV 02...
Page 46: ...44 39880844 REV 01...
Page 48: ...46 39872031 REV 01 SEE PIPING ASSEMBLY OPTIONS...
Page 52: ...50 39872023 REV 02 TO AFTERCOOLER TO AFTERCOOLER...
Page 57: ...55 DATE RUN TIME WORK DONE QTY UNIT WORK HOURS MEASURE BY 8 0 MAINTENANCE RECORD...
Page 58: ...56 DATE RUN TIME WORK DONE QTY UNIT WORK HOURS MEASURE BY MAINTENANCE RECORD...