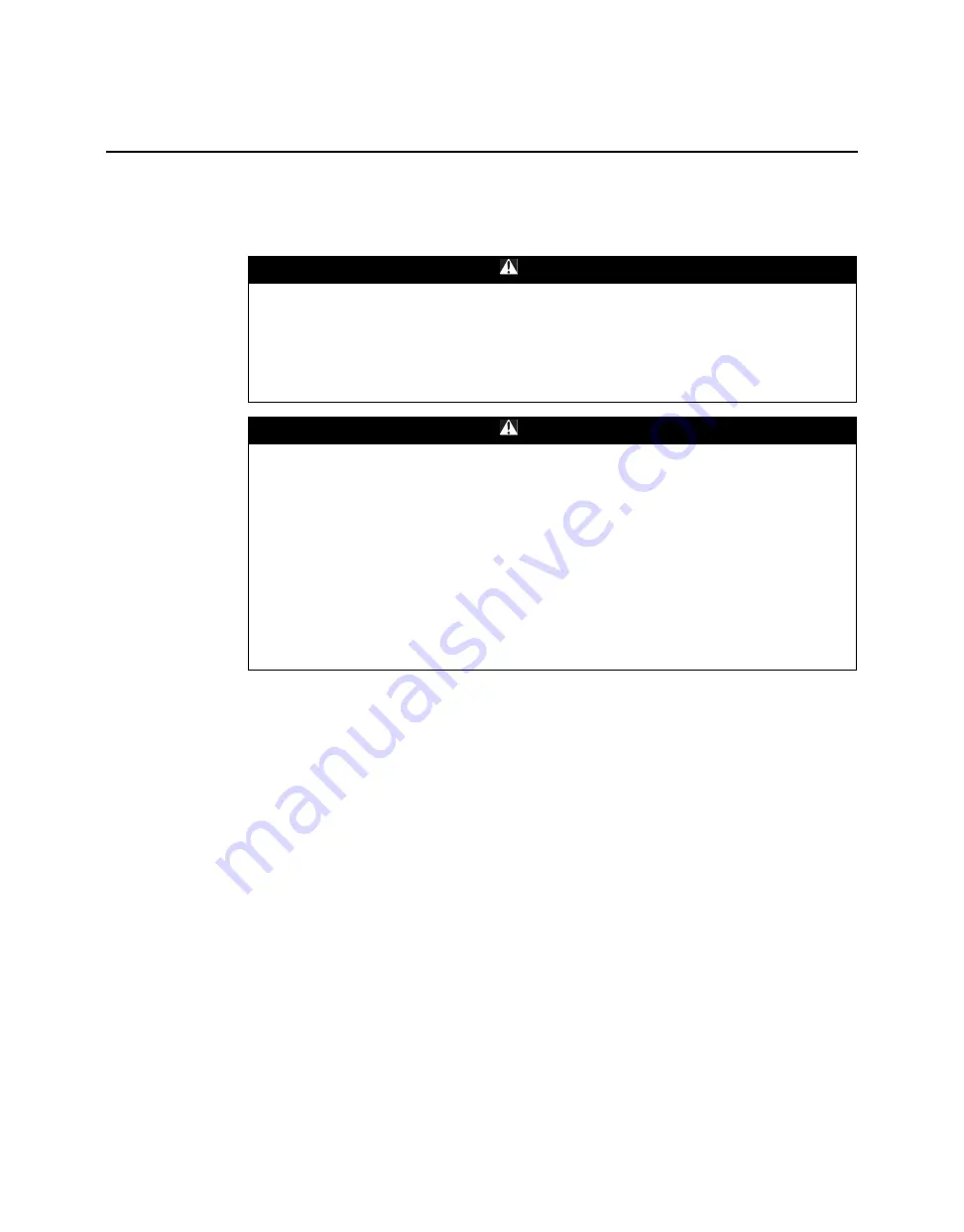
14
Installation
Leak Testing Pipe Connections
WARNING
Confined Space Hazards!
Do not work in confined spaces where refrigerant or other hazardous, toxic or flammable gas
may be leaking. Refrigerant or other gases could displace available oxygen to breathe, causing
possible asphyxiation or other serious health risks. Some gases may be flammable and or
explosive. If a leak in such spaces is detected, evacuate the area immediately and contact the
proper rescue or response authority. Failure to take appropriate precautions or to react properly
to such potential hazards could result in death or serious injury.
WARNING
Explosion Hazard!
Never use an open flame to detect gas leaks. It could result in an explosion. Use a leak test
solution for leak testing. Failure to follow recommended safe leak test procedures could result
in death or serious injury or equipment or property-only-damage.
Use only dry nitrogen with a pressure regulator for pressurizing unit. Do not use acetylene,
oxygen or compressed air or mixtures containing them for pressure testing. Do not use
mixtures of a hydrogen containing refrigerant and air above atmospheric pressure for pressure
testing as they may become flammable and could result in an explosion. Refrigerant, when
used as a trace gas should only be mixed with dry nitrogen for pressurizing units. Failure to
follow these recommendations could result in death or serious injury or equipment or
property-only damage.
Do not exceed unit nameplate design pressures when leak testing system. Failure to follow
these instructions could result in an explosion causing death or serious injury.
Notes:
• All required piping pressure tests must be completed in accordance with national and/or
local codes.
• When leak-testing refrigerant systems, observe all safety precautions.
• Leak test to 590 psig to minimize system exposure to potentially harmful moisture in the
air.
• Use R-410A refrigerant gas as a tracer for leak detection and use oil-pumped dry nitrogen
to develop required test pressures.
1.
Close liquid line angle valve.
2. Connect R-410A refrigerant cylinder to high side charging port (at condenser or field supplied
discharge line access port). Add refrigerant to reach pressure of 12 to 15 psig.
3. Disconnect refrigerant cylinder. Connect dry nitrogen cylinder to high side charging port and
increase pressure to 150 psig. Do not exceed high side (discharge) unit nameplate design
pressure. Do not subject low side (suction) components to high side pressure.
4. Check all piping joints, valves, etc. for leaks. Recommend using electronic detector capable of
measuring 0.1 oz/year leak rate.
5. If a leak is located, use proper procedures to remove the refrigerant/nitrogen mixture, break
connections and make repairs. Retest for leaks.
6. Make sure all service valves are open.